TrueChoice Defense
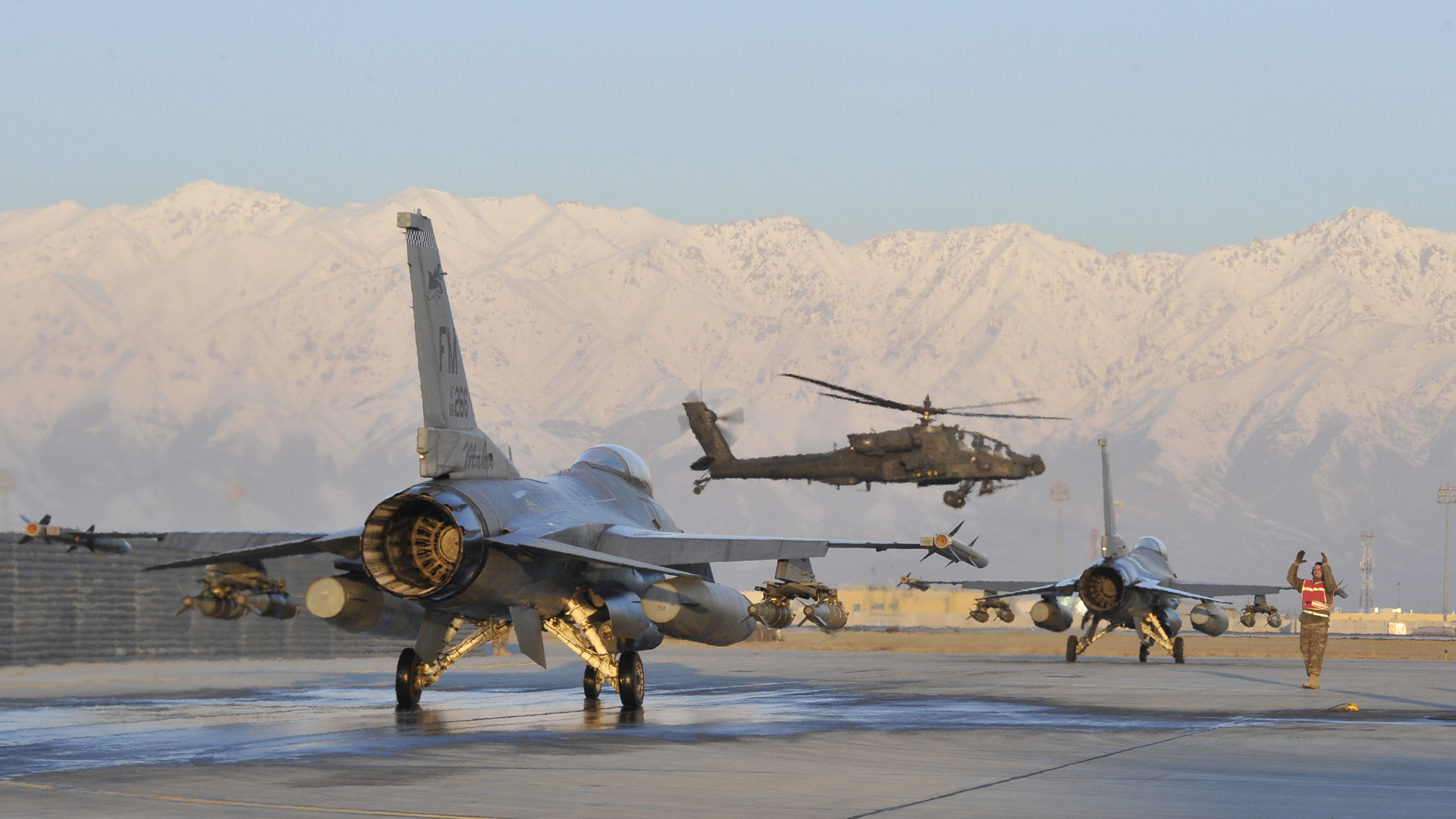
It’s all about
choice
GE Aerospace offers TrueChoice Defense services for military operators.
TrueChoice Defense accommodates a full range of customer needs and operational priorities with an unmatched level of service and support
TrueChoice Defense accommodates a full range of customer needs and operational priorities with an unmatched level of service and support
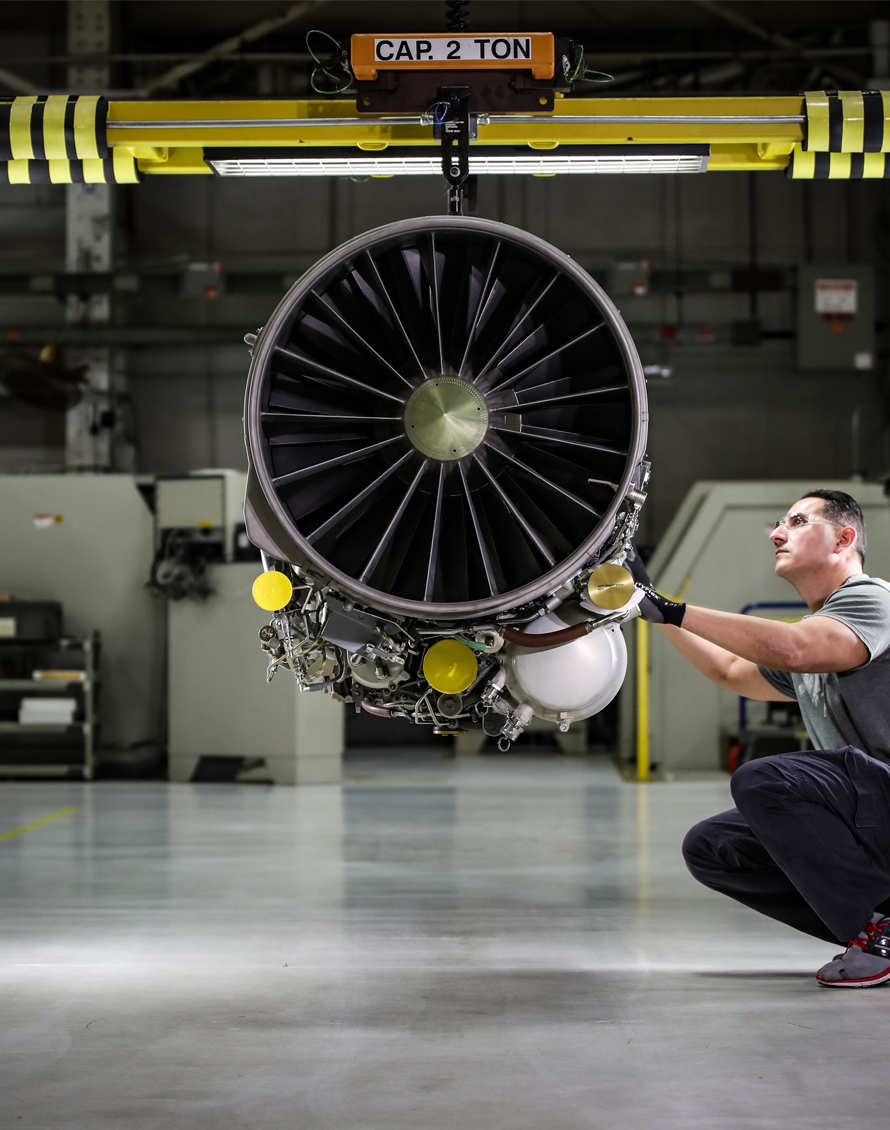
We understand that readiness matters. From parts supply to total logistics support, GE has the right program to support your maintenance and operational needs. Combining GE Aerospace’s material, logistics, and technical support with in-country maintenance capabilities optimizes customer engine performance and fleet availability at predictable costs and reduced financial risk.
GE Aerospace has more than 20 years of experience implementing customized service solutions to address the unique requirements of military customers. Our comprehensive service solutions have helped our customers to reduce operating cost by more than 10% and increase asset availability to more than 95%. Together, we will find a solution to keep your engines on wing, right where they belong.
TrueChoice Defense offers a stand-alone Entry into Service Package for new customers and a choice of four distinct service levels to support your fleet.
GE Aerospace has more than 20 years of experience implementing customized service solutions to address the unique requirements of military customers. Our comprehensive service solutions have helped our customers to reduce operating cost by more than 10% and increase asset availability to more than 95%. Together, we will find a solution to keep your engines on wing, right where they belong.
TrueChoice Defense offers a stand-alone Entry into Service Package for new customers and a choice of four distinct service levels to support your fleet.
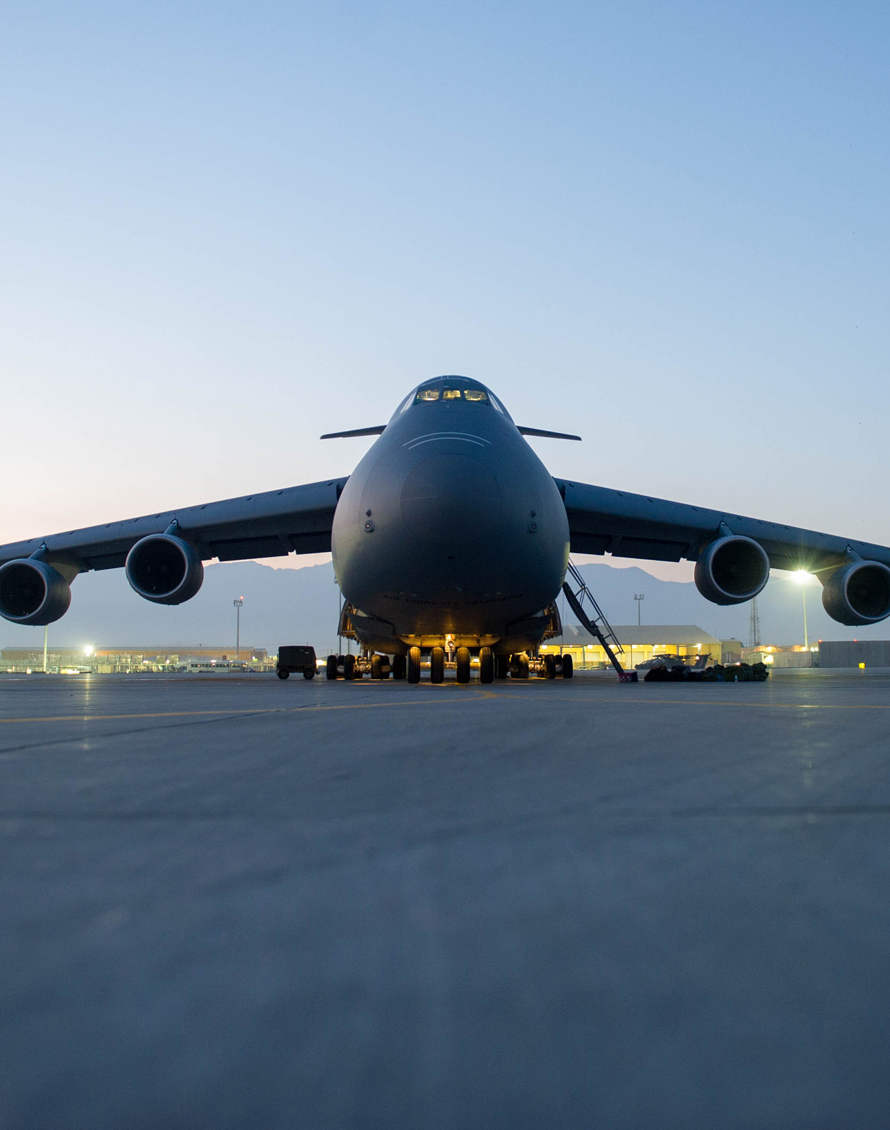
TrueChoice Defense benefits
Flexibility
- Service offerings customized to meet your specific needs
Increased readiness
- Optimized engine availability and performance, enhanced through in-country capabilities
Reduced financial risk
- Consistent, predictable costs; risk mitigation through GE Aerospace capability and expertise
World-class support
- Expert training, publications, field support, provisioning, and fleet management delivered by GE Aerospace
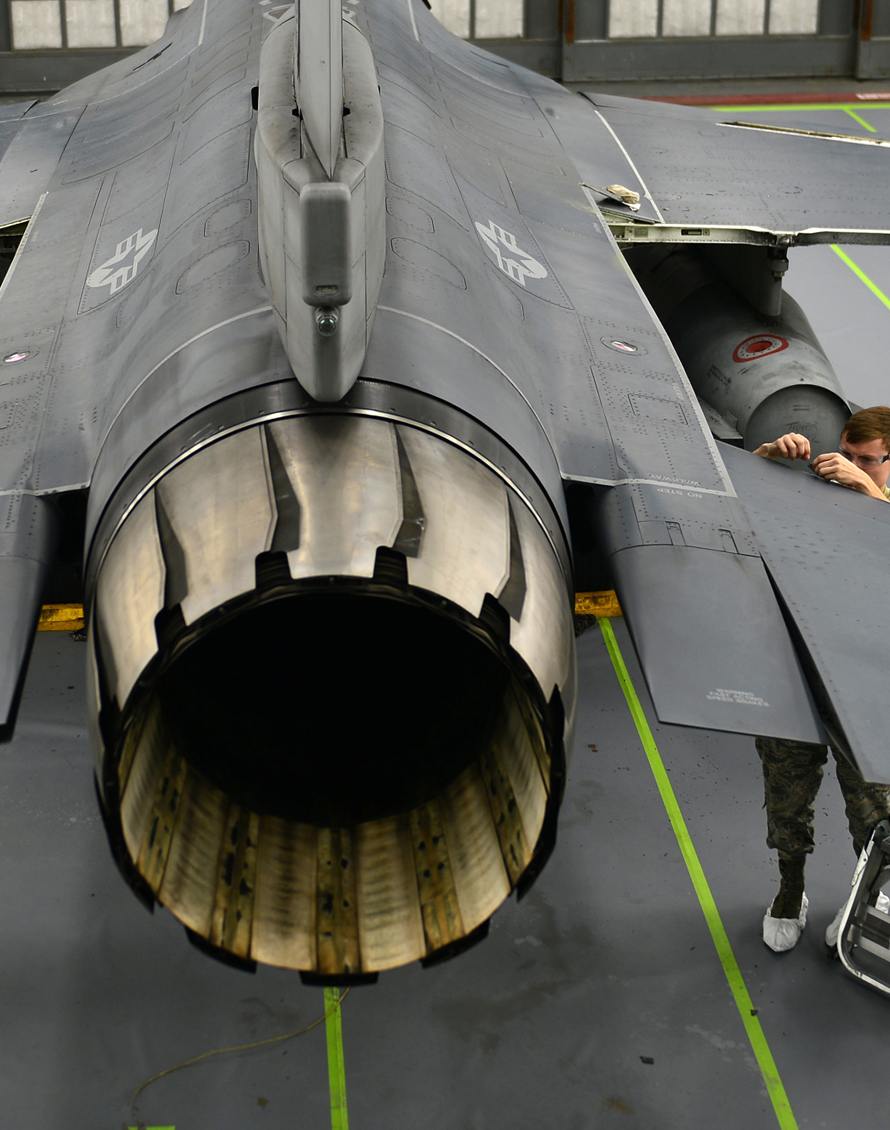
Entry Into Service (EIS)
The Entry Into Service (EIS) package is the ideal solution for new operators who seek the expert support and guidance of GE Aerospace as they provision and launch their engine fleet. The EIS package provides all the necessary elements for the effective operation and management of an engine fleet.
- Package elements include: site survey with facility suitability and test cell assessments, initial material provisioning, field service representatives, technical support, publication delivery, and support equipment selection
- EIS package directly supports O-Level (Flight Line & On-Wing) as well as I-Level (Operating Base) maintenance
- Additional support can include D-Level (Overhaul & Repair) facility recommendations and equipment outfitting as requested
- EIS package can be combined with other service level options to maximize fleet readiness and control engine Life Cycle Costs (LCC).
- EIS package selection leads to a TrueChoice Defense Service Activation
Additional Services available
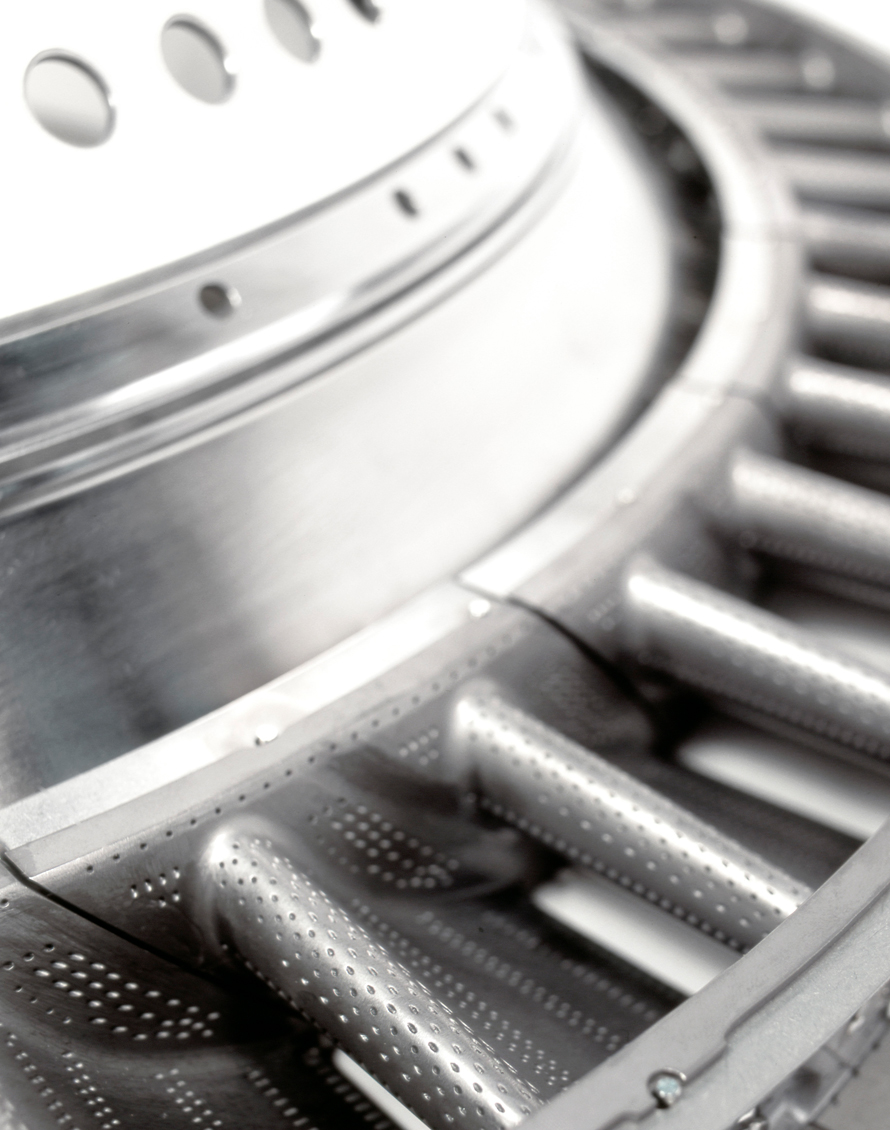
Basic Spares Support (Basic)
Basic Spares Support is a transactional level of spare parts support delivered at standard lead-time with options to supplement with additional Integrated Logistics Support (ILS) services.
- Basic Support includes access to Material Catalog with fixed pricing and standard lead times
- Entering into a Basic Ordering Agreement (BOA) with GE Aerospace allows seamless material ordering with direct access to the OEM Material Stream
- Other ILS related services can be added under the General Terms contained in the BOA
- Customers can combine Basic Support with engine upgrade packages, overhaul kits, material life-time buys, and deployment kits.
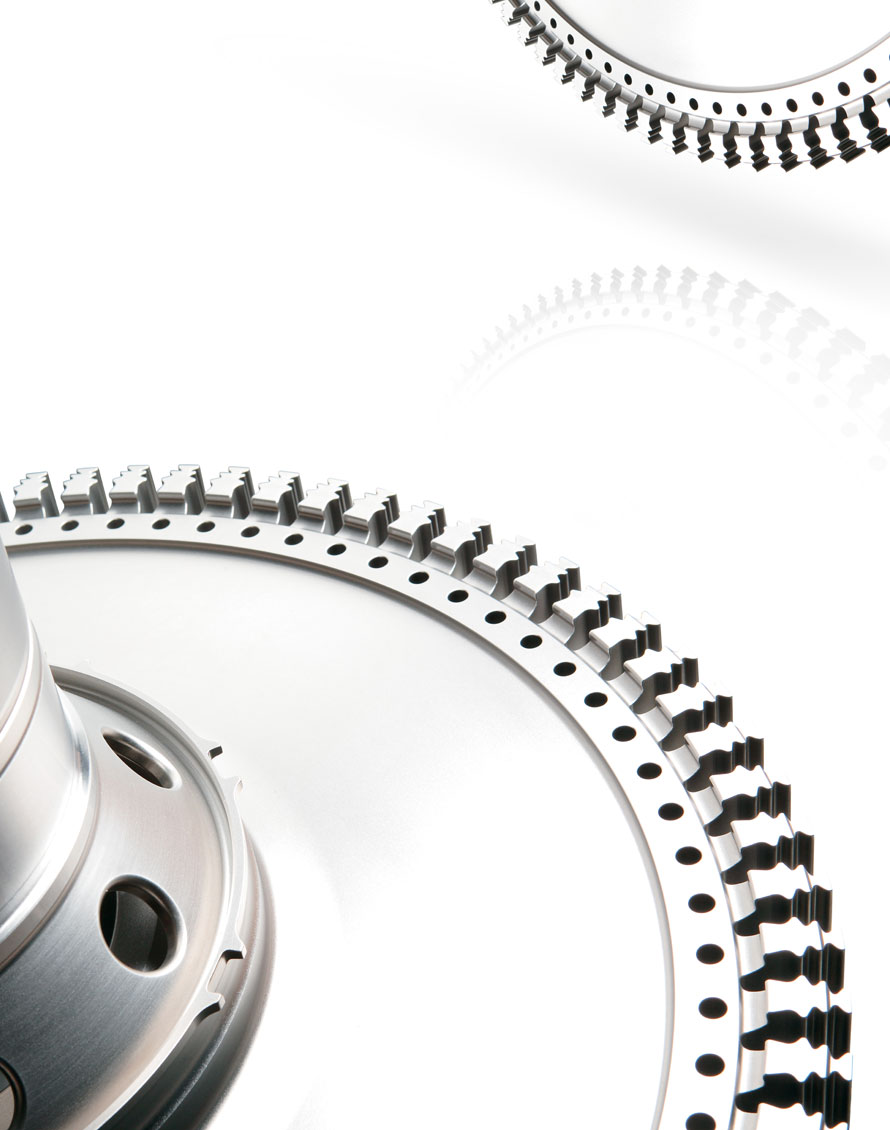
Material Support Agreement (MSA)
A Material Support Agreement (MSA) features proactive forecasting, provisioning, inventory right-sizing, and configuration control. MSA contracts enable higher fleet readiness and minimize the disruption associated with delayed material delivery.
- A MSA includes comprehensive material planning for lay-in and replenishment of spare piece parts and consumables
- Forecasting support provides right-sized inventory based on shop visit forecast, customer maintenance plans, and technical data
- Demand analysis generates a rotable pool of critical components and reduces engine turnaround time
- Logistics management and inventory control between warehouses, shops and bases assures optimal spares usage
Additional Services available
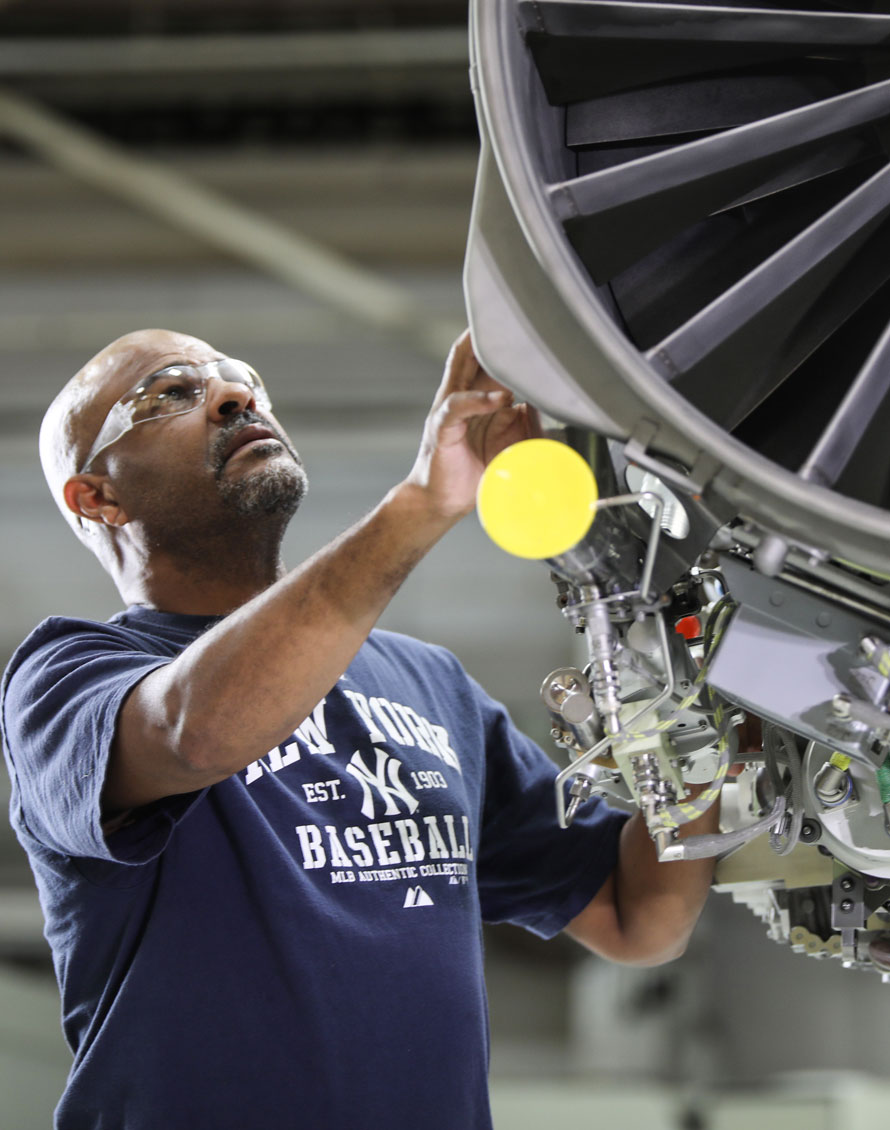
Performance Based Logistics (PBL)
Performance Based Logistics (PBL) is a long-term services agreement that optimizes customer resource utilization, rotable pool management, and MRO operations with data-driven material, logistics, and fleet management. PBL agreements drive optimal fleet readiness at a predictable operational expense.
- Flexible maintenance and repair with data-driven solutions optimize your resource utilization and reduce operational expenses
- Fleet readiness is directly related to repair Turn Around Time (TAT) and material availability
- Repairs linked with Material solutions provide cost-saving repairs
- Tech transfer is available for repair processes
- Engineering Query Service is provided with Field Service Rep (FSR) and Customer Support Manager (CSM) support
- PBLs offer low total cost of ownership with mid-term or long-term view
- Optional Foreign Object Damage (FOD) and Line Replaceable Unit (LRU) coverage are also available
Additional Services available
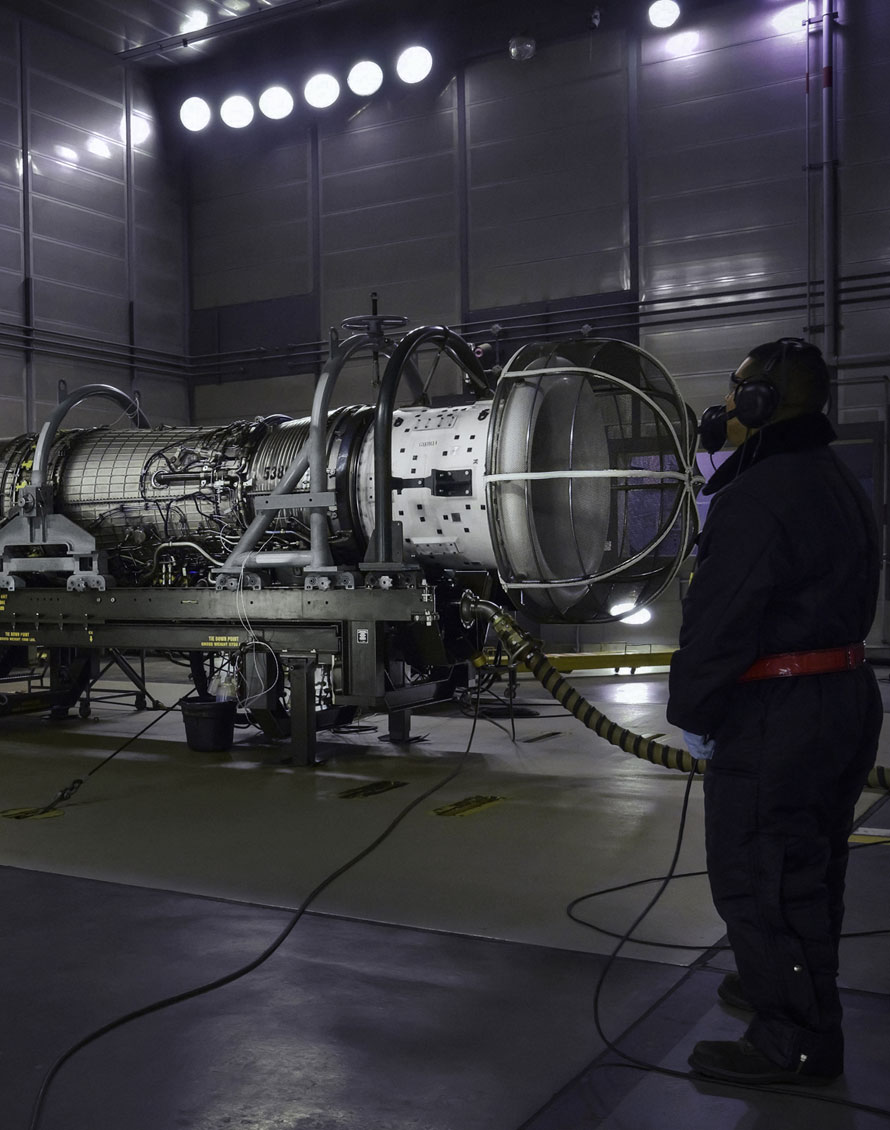
Total Logistics Support (TLS)
Total Logistics Support (TLS) is a long-term contract that provides full maintenance and logistics management services through GE Aerospace’s extensive Depot network, advanced repair technology, and integrated logistics support. These comprehensive GE Aerospace capabilities lower your resources needs, reduce Life Cycle Costs (LCC), and reduce financial risk via fixed cost contracting.
- TLS is a turnkey value with all aspects of on-wing support and MRO in single solution
- Each TLS is tailored to specific customer needs to lower cost of ownership, minimize maintenance burden, and maximize fleet availability.
- It is a full risk transfer engine maintenance with cost based on dollar per engine flight hour or cycle
- TLS includes:
- Scheduled and unscheduled removals
- New, used serviceable & repaired material
- Tailored work scopes / Service Bulletin coverage
- Fleet Management with Comprehensive remote diagnostics and trend monitoring
- FSR, Tech Data, Training, Support Equipment services
- Optional Foreign Object Damage (FOD) and Flight line LRU coverage available
Additional information
GE Aerospace’s experienced technical advisors will help reduce your sustainment costs. Our global network of Field Service Representatives (FSRs) provides a direct link to the vast experience of our powerplant support engineering team. Providing timely technical interpretations, our FSRs can prevent unneeded engine removals and keep your maintenance operations flowing efficiently.
Our FSRs are also available to conduct onsite training for product operation and maintenance.
GE Aerospace offers technical inquiries services for publicization publication clarification, engineering review, and engine shop guidance.
Several levels of FSR support are available depending on your operational needs.
Our FSRs can be located at main operating bases, repair shops, or depots as required.
The GE Aerospace Customer Technical Education Center (CTEC) located in Cincinnati, Ohio, offers multiple training classes for new and existing engine operators.GE Aerospace has world-class engine training experts who provide comprehensive technical training and hands-on engine maintenance, including real-world application and insights.GE Aerospace’s training experts can also create customized training solutions for operators with unique training needs. Training is also available at the customer location depending on customer needs.
GE Aerospace provides customer access to approved engine manuals.
Available manuals include: Engine Assembly, Disassembly, Cleaning, Inspection, Repair, Standard Practices, IPB, NDI, and Time Compliance Technical Orders (TCTOs). Customized manuals can be developed based on the operator’s specific requirements. Manuals are offered on multiple authoring platforms, including Mil Spec and S1000D.
All GE Aerospace technical publications are available online or on DVD depending on the customer needs. GE Aerospace also offers hosting and viewer solutions if desired.
Operators have access to all online technical inquires and product support engineering services.
GE Aerospace will provide a list of specific support equipment and common tooling recommended for engine fleet maintenance. These lists can be customized based on the customer’s operational needs and the desired level of maintenance capability.
All support equipment will be available through GE Aerospace’s licensed support equipment suppliers.
GE Aerospace will also provide storage and transportation containers for engines, Shop Replaceable Units (SRUs), and Line Replaceable Units (LRUs).
GE Aerospace will conduct an onsite survey to determine the suitability of the existing Maintenance, Repair and Overhaul (MRO) capabilities, facility infrastructure, and engine test cells.
Following the site survey, GE Aerospace will develop a comprehensive report identifying facility sizing, infrastructure gaps, recommended modifications, suggested facility equipment, and fixture updates.
The Site Survey/Facility Suitability report provides the basis for the recommended EIS package elements to achieve fleet maintenance capability.
GE Aerospace offers technology kits to upgrade existing engines. These kits improve Life Cycle Cost, reliability, and time-on-wing with reduced fuel burn, increased performance, or added horsepower (HP) extraction.
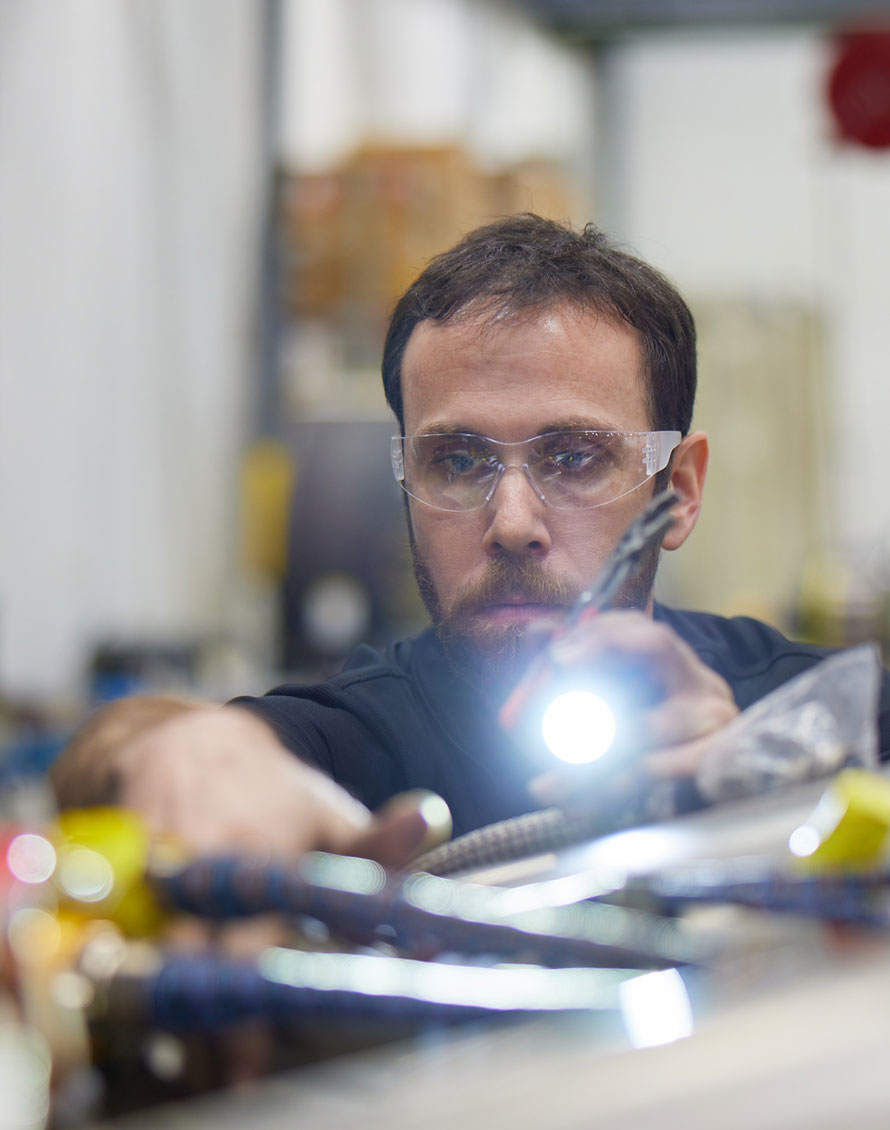
Digital Services
GE Aerospace’s digital solutions support fleet management throughout the engine lifecycle. Based on data and analytics, our outcome-based solutions will reduce operating costs, enable greater aircraft utilization, and increase efficiencies.
GE Aerospace utilizes digital tools to create efficiencies that go beyond the engine. Our digital tools provide a complete picture of your overall fleet through engine utilization, configuration data tracking, demand planning, inventory management, Life Limited Part (LLP) tracking, and repair forecasting.
Additionally, GE Aerospace offers the opportunity to partner and co-develop digital solutions tailored to your specific fleet needs.
GE Aerospace utilizes digital tools to create efficiencies that go beyond the engine. Our digital tools provide a complete picture of your overall fleet through engine utilization, configuration data tracking, demand planning, inventory management, Life Limited Part (LLP) tracking, and repair forecasting.
Additionally, GE Aerospace offers the opportunity to partner and co-develop digital solutions tailored to your specific fleet needs.
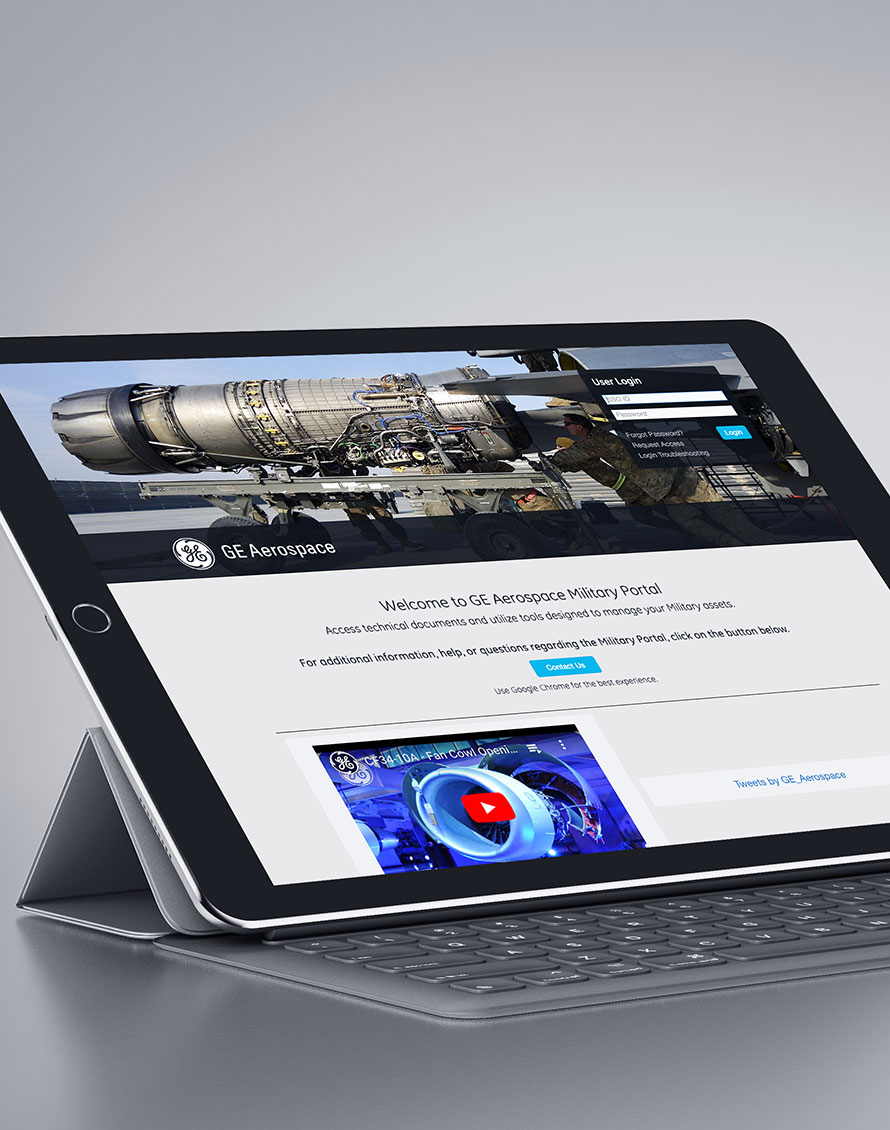
Military Portal
GE Aerospace's customizable military portal provides access to technical documents and tools designed to assist in managing your assets.
- Access includes digital technical publication documents for your fleet, including depot maintenance manuals, field service instructions, and service bulletins
- Prices for spare parts purchases are available with our digital spare parts catalog
The appearance of U.S. Department of Defense (DoD) visual information does not imply or constitute DoD endorsement.