Bring Them Home
Safely
Safely
Around 950,000 people are flying on aircraft right now powered by GE Aerospace and its joint venture partners' technology. It’s a tremendous responsibility and why safety comes first.
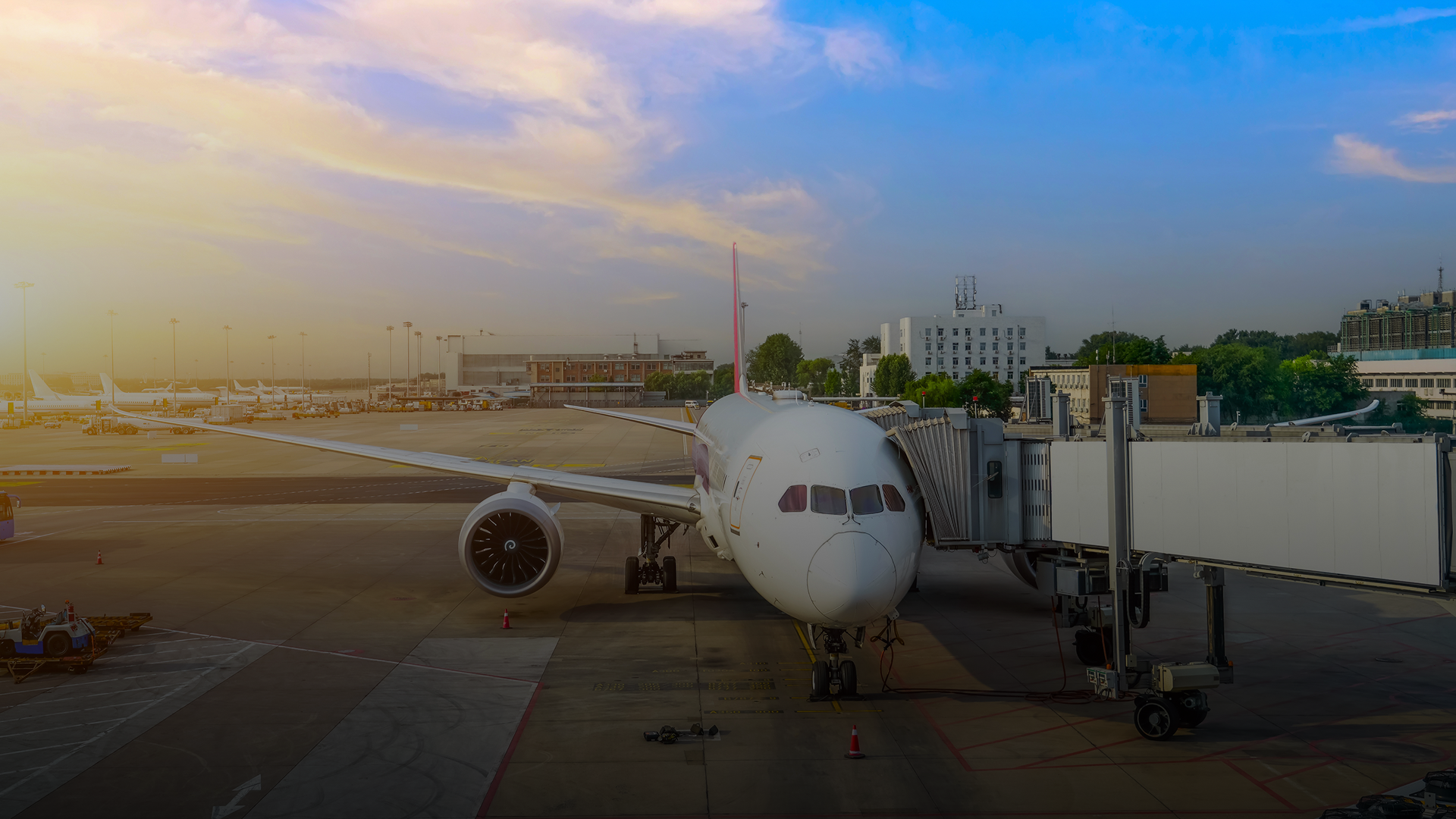
Laying a solid safety
foundation
FLIGHT DECK
Proprietary lean operating model
Our lean proprietary operating model is how we operate the business and helps keep our employees, customers, passengers, and everyone who counts on us safe.
Product Safety →
Worker Safety →
SQDC
Safety, Quality, Delivery, and Cost — always in that order
Safety comes first at GE Aerospace, and the company encourages employees to report safety concerns voluntarily and confidentially without fear of retaliation.
Report a safety concern →
First
Manufacturer with accepted Safety Management System
Ten years before the FAA proposed requiring Safety Management Systems for aerospace manufacturers, GE Aerospace established one.
See how our SMS is working →
View a timeline of other key safety milestones for GE Aerospace →
Maintaining Quality
Throughout an engine’s life, we have innovative technologies to help ensure quality and safety is properly maintained. Watch short videos to learn more.
Partnership for safety
Raw material suppliers for safety-critical parts share quality data to detect defects early and continuously improve.
Real-time monitoring
We constantly review data from customers’ fleets to spot immediate issues and any potential risks.
Our work is never done
See current stories about how we are using FLIGHT DECK to keep our people and products safe.