Landmark technologies
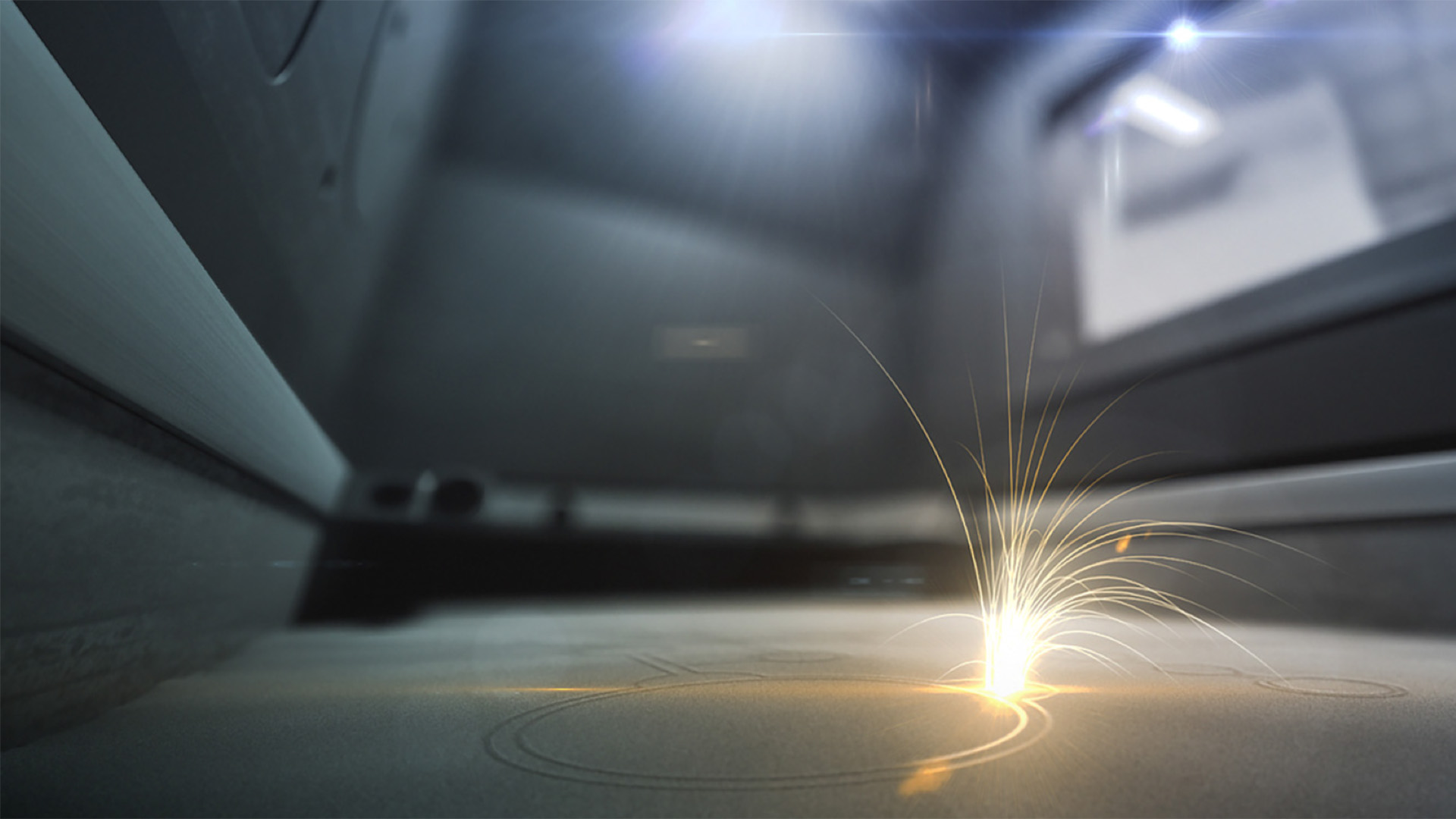
Moving innovation
Technologies introduced by GE and Safran Aircraft Engines through our 50-50 joint company CFM International has resulted in today’s commercial aircraft engines consuming 40% less fuel compared to engines manufactured in the 1970s and 1980s.
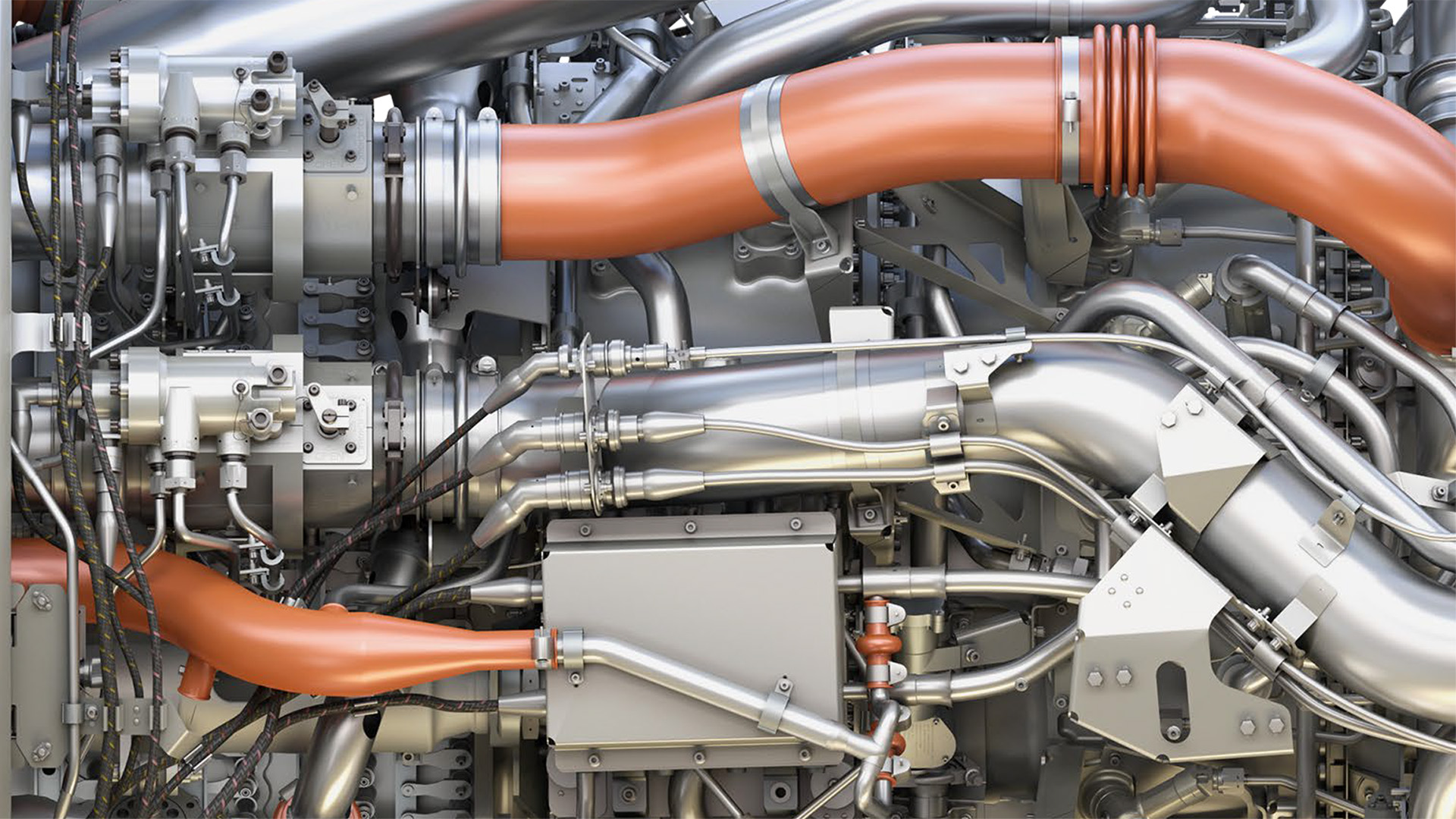
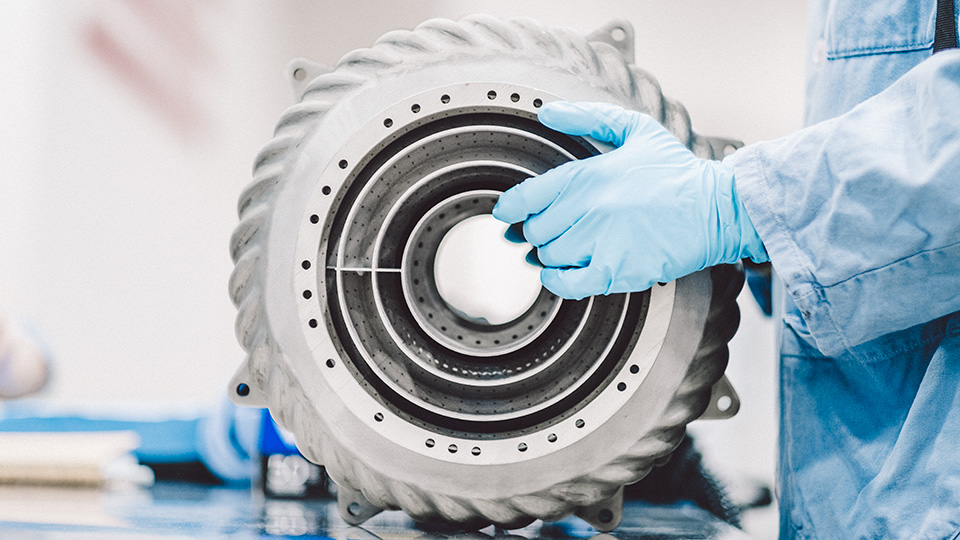
Additive manufacturing
Additive manufacturing involves using computer aided designs to "print" a part from metal powder, layer by layer. Unlike traditional manufacturing methods that mill or cut away from a slab of metal to produce a part, additive manufacturing (also known as 3D printing) grows parts directly from a computer-designed file using layers of fine metal powder and an electron beam or laser. The resulting part can be lighter weight with less waste, manufactured in a fraction of the time it would take using traditional methods. The ability to grow parts with additive manufacturing also allows for the elimination of joints and improvement of designs by creating a single, integrated part to replace an assembly.
In Auburn, Alabama, GE Aerospace opened the aviation industry’s first site for mass-producing aircraft engine parts using additive manufacturing. Employees in Auburn began producing additive fuel nozzle tips in 2015. Today, GE Aerospace and CFM International have more than 10 additively-made parts approved by the U.S. Federal Aviation Administration (FAA) for commercial aviation use for GE90, CFM LEAP, GEnx and GE9X engines. Upon certification of GE’s Catalyst turboprop engine, GE Aerospace could have more FAA-certified additive parts in commercial operation, including engine structural parts.
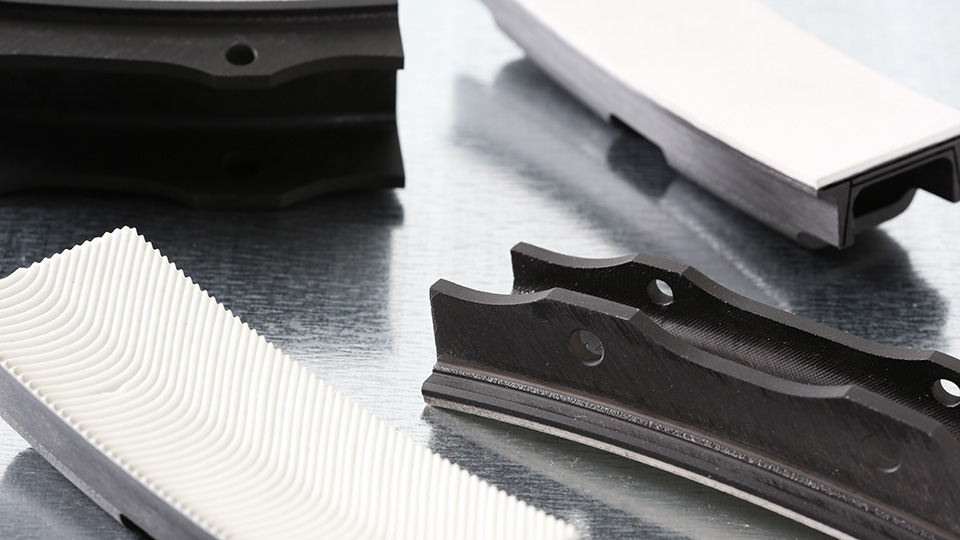
Breakthrough materials
Since introducing carbon fiber composite fan blades to service with the GE90-94B engine in 1995, GE Aerospace has accumulated more than 25 years and over 100 million engine flight hours of experience with composite fan blades. Today, GE and CFM International remain the only aircraft engine manufacturers with composite fan blades in commercial service.
Carbon fiber composite fan blades are higher strength and lighter weight than the traditional titanium fan blades they replaced, helping improve fuel efficiency in GEnx, CFM LEAP and GE9X engines compared to their predecessors. When the GEnx entered service in 2011, carbon fiber composite materials were expanded to the fan case, as well as the fan blades, helping the GEnx reach up to 15% better fuel efficiency than the CF6 engine.
Ceramic Matrix Composites (CMCs), another type of composite material, are lighter weight than traditional material alloys and more heat resistant, allowing engines made with CMCs to operate at higher temperatures with less cooling air. The CFM LEAP engine, which entered service in 2016, was the first to contain a CMC part in the engine’s hot section and is 15% more fuel efficient than the CFM56 engine.
GE Aerospace continues to advance carbon fiber composite and CMC materials for next-generation aircraft engines, including looking at expanding composite materials to more areas of an engine.
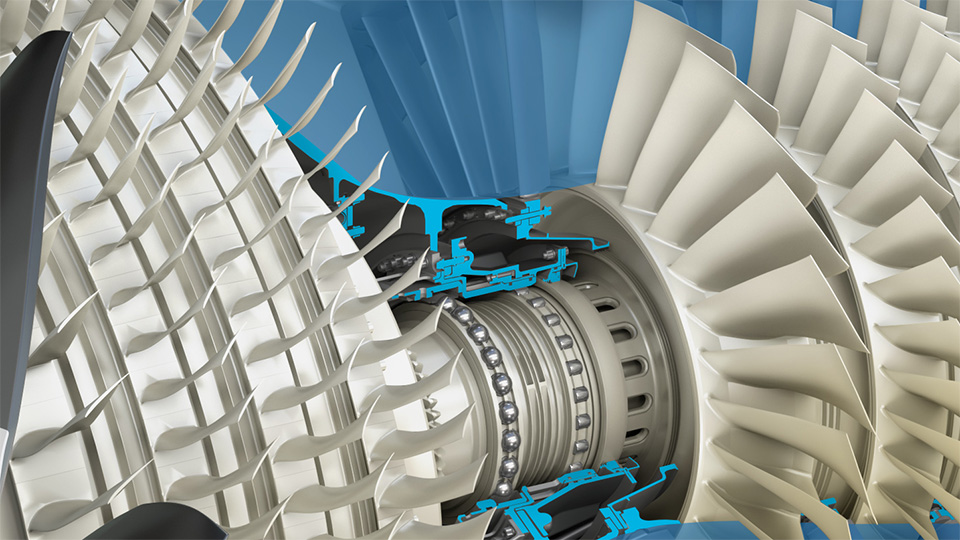
Advanced aerodynamics
Carbon fiber composites materials, along with 3D aerodynamic design have allowed GE Aerospace to improve the design of fan blades and reduce the number of fan blades in the front of turbofan engines. These advances and larger fan diameters allow the fan to pull in more air, increasing bypass ratio and air pressure throughout the engine, including in the engine core. More air flow and higher operating pressures help drive the rotor with less energy, improving fuel efficiency. GE Aerospace is a leader in aerodynamic technologies and high bypass engines, leading to the world’s largest and most fuel efficient certified engine in its thrust class—the GE9X. The GE9X engine has an unprecedented bypass ratio of 10:1 compared to its predecessor, the GE90, which has a bypass ratio of 9:1.
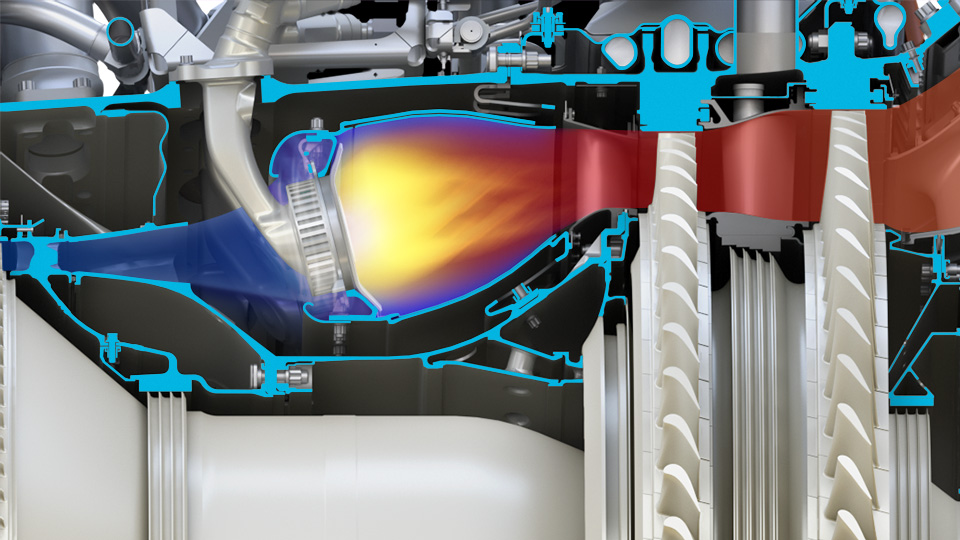
Lean burn combustion
Lean-burn combustion technologies accommodate the increased temperatures associated with higher pressure ratios while reducing emissions of nitrous oxide (NOx) by using a twin-annular pre-mixing swirler to optimize the air and fuel mixture. The GE9X engine, which received U.S. FAA certification in 2020, is designed to deliver NOx emissions 55 percent below current regulatory requirements using lean burn combustion
Beyond engines, GE Aerospace’s Systems business continues to bring additional efficiencies to aircraft performance. Software solutions that can help deliver immediate carbon reductions are available today and already in use.
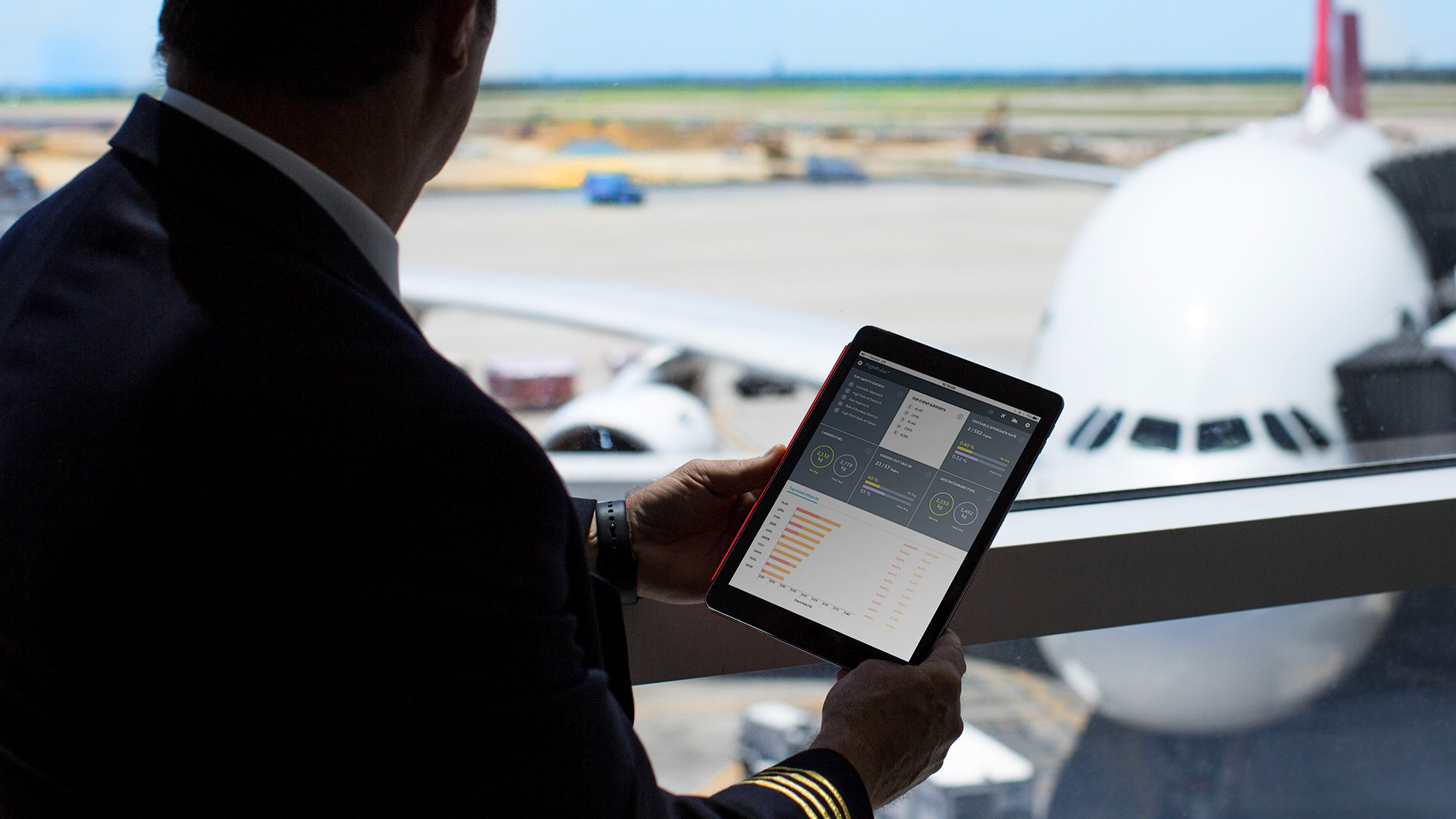
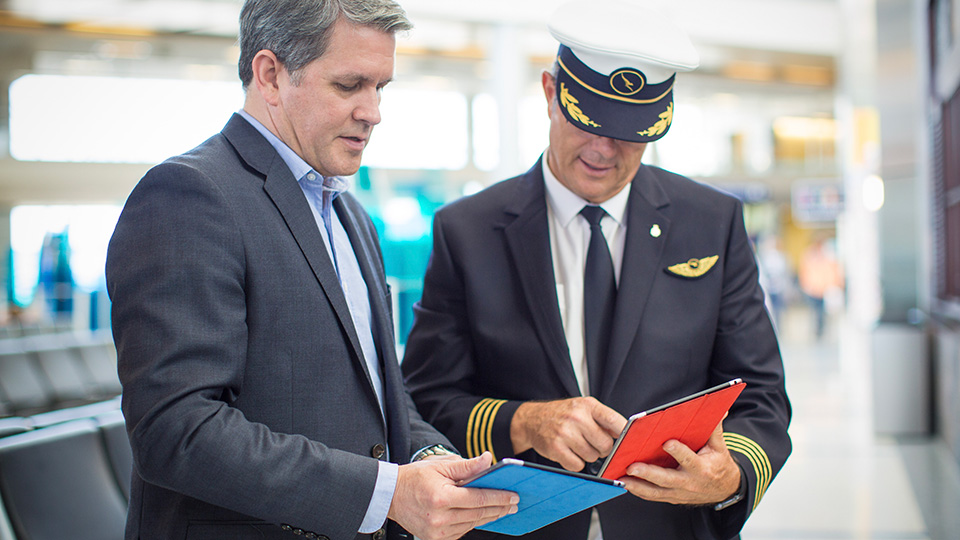
Digital tool to save fuel
GE Digital has developed a number of software applications to help aircraft operators to reduce CO2 emissions and drive operational efficiencies. For example, FlightPulse® is a flight analytics tool that helps airline pilots improve safety and operational decision-making, including recommendations for fuel savings. Fuel Insight helps airlines identify areas of opportunity to improve their fuel consumption, while Airspace Insight offers flight path design and maintenance to assist aircraft operators in ensuring routes are optimally designed to minimize time, fuel, and emissions
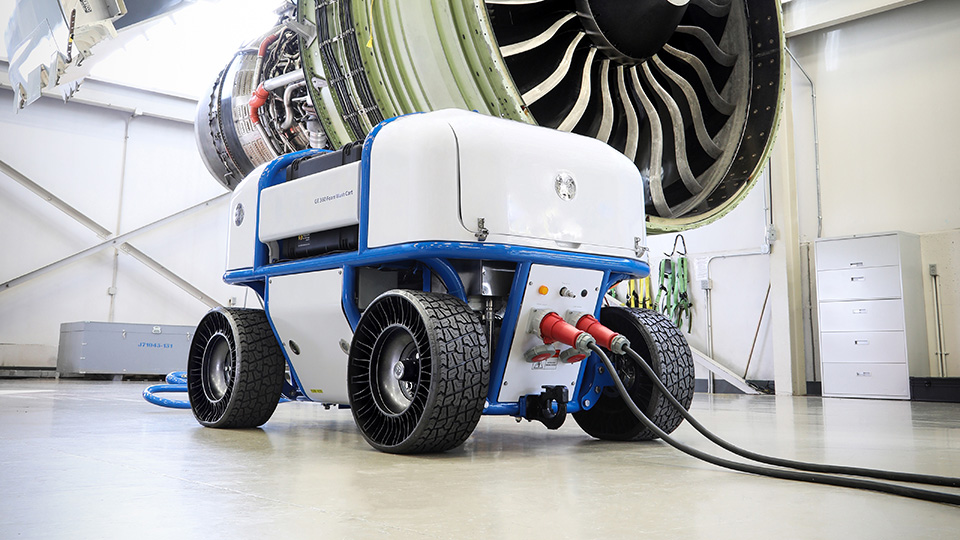
360 Foam Wash
GE’s proprietary 360 Foam Wash is an advanced on-wing cleaning technology to help ensure that engines continue to operate efficiently. In the Middle East, GE’s 360 Foam Wash has been found to improve engine performance by reducing build-up of deposits in the engine, lowering engine exhaust temperatures, and improving engine compressor efficiency. These improvements led to reduced fuel consumption, lower CO2 emissions, and increased engine time on wing.
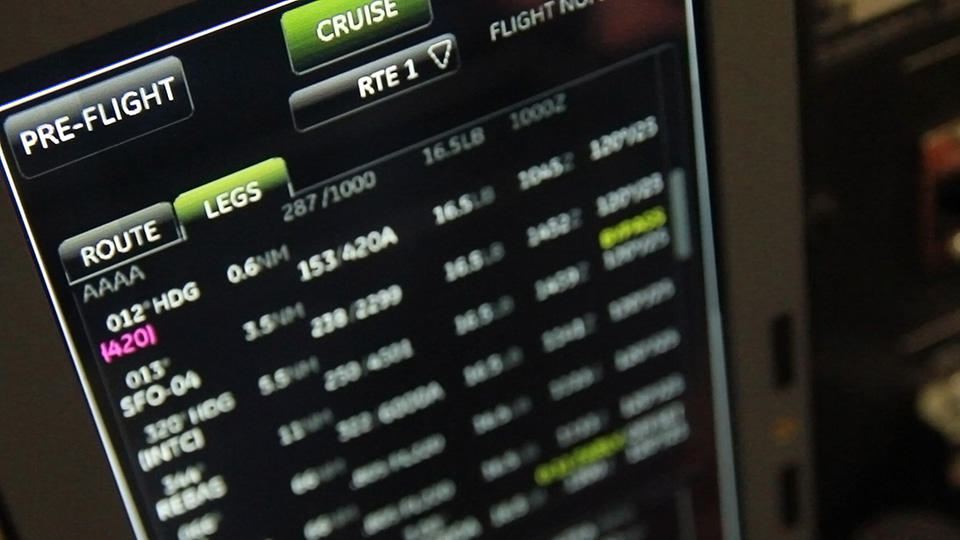
Optimized flight paths
GE Aerospace’s Flight Management System (FMS) provides increased situational awareness and operation efficiencies on more than 12,000 aircraft worldwide including models of the Boeing 737, the Boeing 737 MAX and military aircraft. FMS is designed to allow an airplane to fly higher longer and allows for an optimized descent that is a more gradual approach to the airport than a stairstep approach. Flying at higher altitudes longer can reduce carbon and noise emissions. GE Aerospace’s FMS-optimized descents offers a potential 6% to 12% fuel savings and roughly 20% lower NOx emissions for operators compared to traditional approaches.
The next suite of engine technologies in development – including advanced architectures like the open fan, hybrid-electric capability, and advanced thermal management concepts – have the potential to achieve at least a 20% additional improvement in fuel efficiency compared to today’s state-of-the-art single-aisle
aircraft engines.
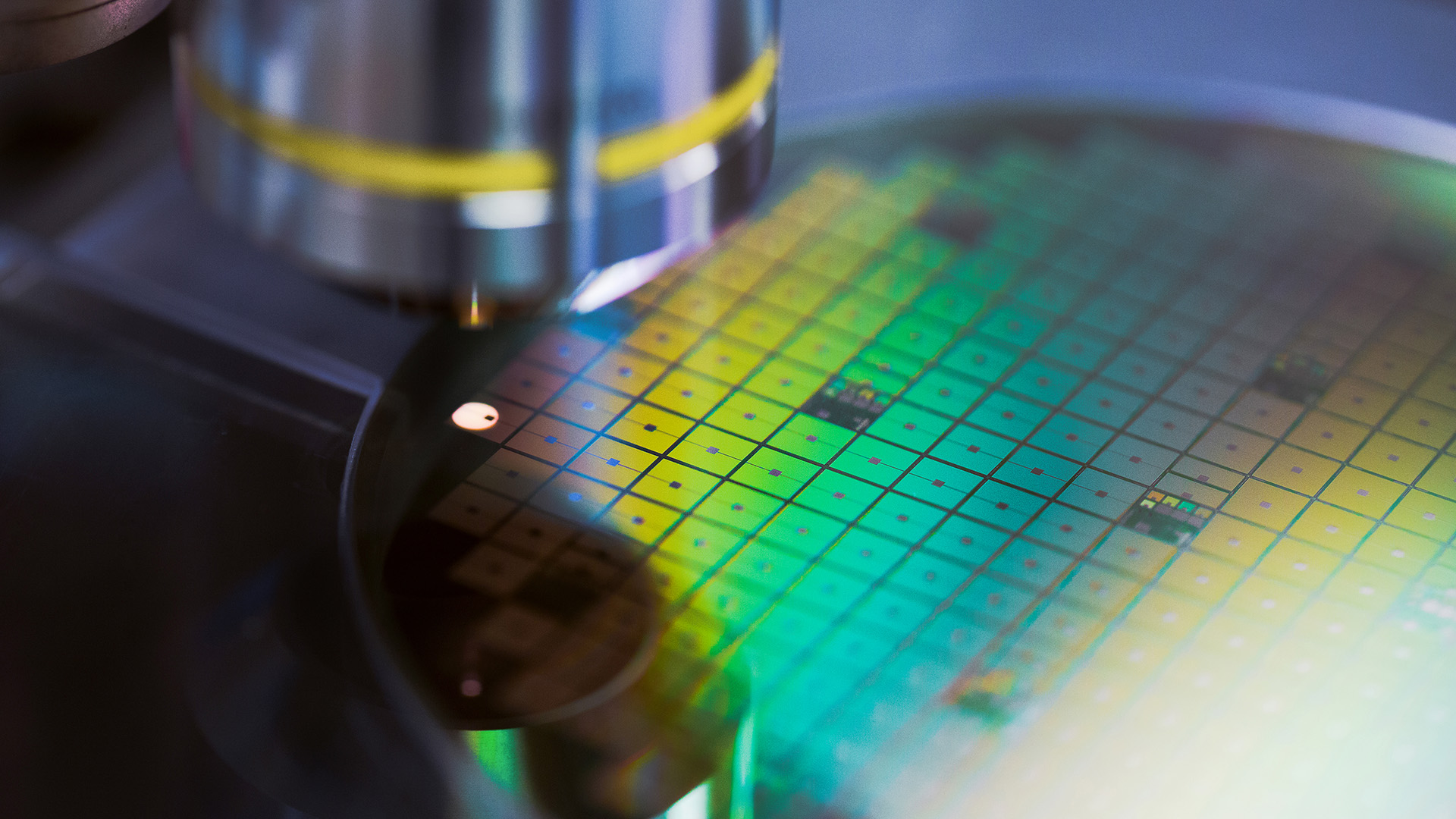
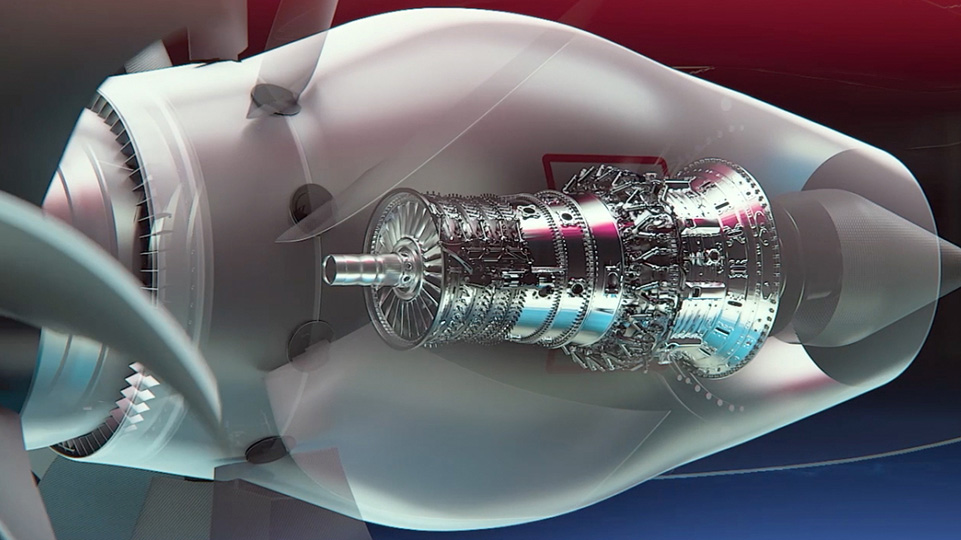
Compact engine core
GE Aerospace is working with NASA to research advanced engine cores for single aisle aircraft. As part of NASA’s Hybrid Thermally Efficient Core (HyTEC) project, GE Aerospace was awarded in 2021 multiple cost-share contracts for engine core development valued at more than $20 million when including both NASA and GE investments.
GE Aerospace will test and mature compact jet engine core designs, including compressor, combustor and high-pressure turbine technologies to improve thermal efficiency. Continued development of Ceramic Matrix Composites (CMCs), an advanced, heat-resistant material, is also a key part of the effort to improve fuel efficiency and reduce emissions. Plans are to ground test a new compact engine core by the mid-2020s.
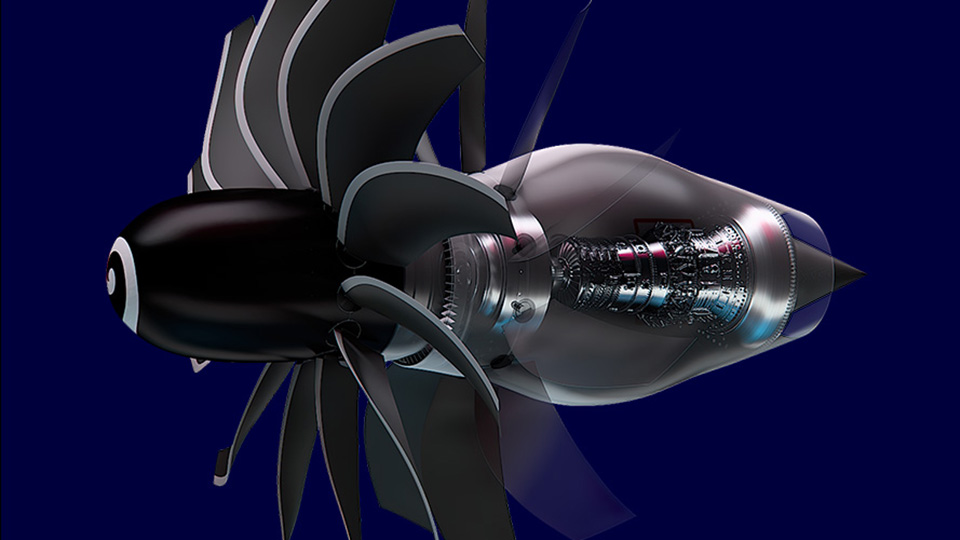
Advanced open fan
GE Aerospace has continually advanced state of-the-art open fan systems by increasing propulsive efficiency. In the 1980s, GE successfully flight tested the GE36 engine, an open fan jet engine demonstrating significant fuel savings compared with conventional ducted front fan engines in the same size class.
Since then, GE collaborated with the U.S. FAA and NASA on sub-scale wind tunnel test campaigns through the CLEEN Program demonstrating better fuel efficiency compared to the CFM56-7B engine and significant margin to noise requirements.
GE Aerospace’s Italian entity, Avio Aero, contributed to the development and testing of counter rotating open fan architectures under Europe’s Clean Sky research program. Under the Clean Sky 2 program, Avio Aero supported optimization of open fan architectures through design and integration studies conducted with airframers.
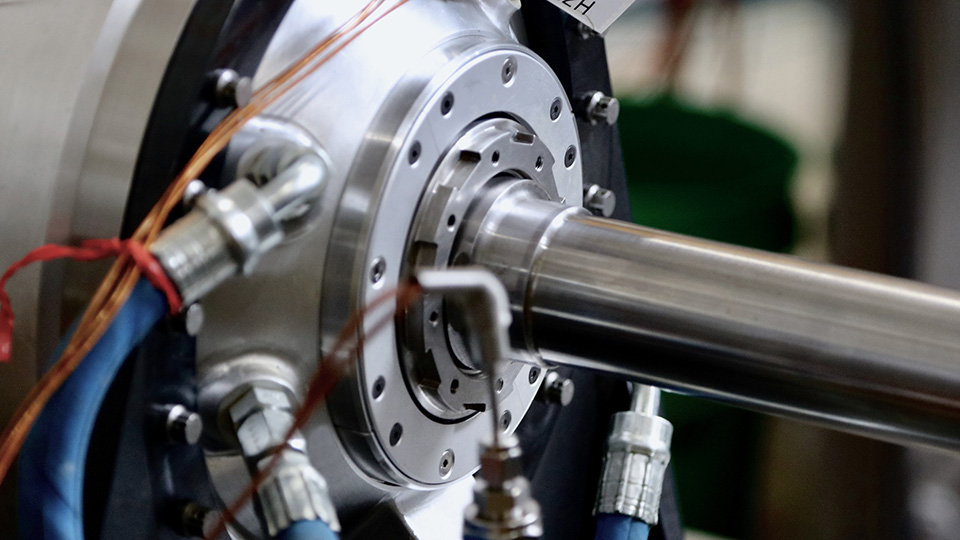
Electrification for aircraft and propulsion systems
Hybrid electric propulsion technologies that save fuel and optimize engine performance are key to GE Aerospace’s commitment to help reduce carbon emissions for a more sustainable future of flight. Hybrid electric technologies are highly compatible with Sustainable Aviation Fuel (SAF) and hydrogen, as well as advanced engine architectures like open fan and new advanced engine core designs.
In 2021, NASA and GE Aerospace launched a hybrid electric technology demonstrator program. After years of developing individual components of a hybrid electric system—motors, generators and power converters—GE will systematically mature a megawatt class (MW) integrated hybrid electric powertrain to demonstrate flight readiness for single-aisle aircraft. Plans are to conduct ground and flight tests of the hybrid electric propulsion system by the mid-2020s using a modified Saab 340B testbed and GE’s CT7-9B turboprop engines.
Our systems business has designed and manufactured power conversion, distribution, and control systems for commercial aircraft for over 30 years. GE Aerospace Systems continues to advance these products with technology including GE-developed silicon carbide transistors to increase efficiency, power density, thermal performance and reliability. These technologies are integral to the development of GE Aerospace’s hybrid electric powertrain demonstrator with NASA.