Three of the twelve 3D-printed components for GE’s Advanced Turboprop engine integrate high tech and thermal capabilities into very small spaces.
Additive technology helped reduce 855 conventional components to just 12 on the Advanced Turboprop, GE’s clean-sheet engine that will power the new Cessna Denali from Textron Aviation. Among these 3D-printed components, the heat exchanger carries a high level of engineering complexity.
“We have never designed entire heat exchangers at Avio Aero in the past," says Antonio Caimano, technical leader for exchangers. "The heat exchangers are assemblies. We start from built-in additive with DMLM technology (Direct Metal Laser Melting), then treat it, machine it and add the necessary parts.”
Heat exchangers are essentially liquid or gas cooling systems for an aircraft engine as air, oil and fuel are suitably mixed according to the heat exchange that is performed. The Advanced Turboprop contains three heat exchangers: the air-to-air heat exchanger (called High Pressure B Sump Heat Exchanger, HPBS HX), the Air-Cooled Oil Cooler (ACOC), and the Fuel Heater (FH).
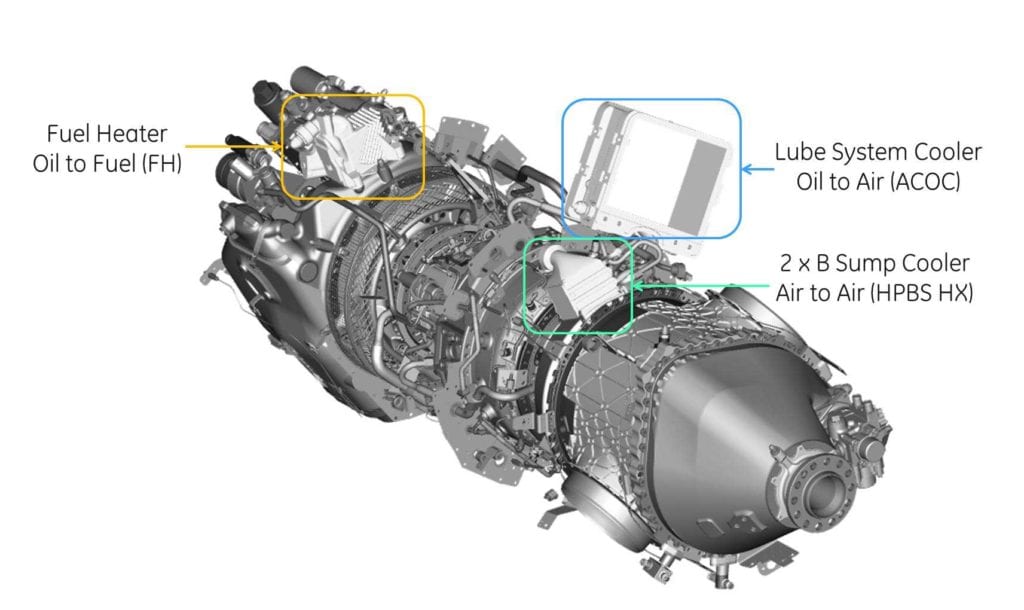
The High Pressure B Sump Heat (HPBS) exchanger, which is air-to-air, is the first to be installed on a GE Aviation engine. In the case of the Advanced Turboprop, it functions to cool the B Sump, the part that houses the turboshaft bearings, as well as the Power Turbine (PT) assembly. It cools these parts by using air extracted partially from a compressor air intake and partially from the cold air circuit passing through the engine. This heat exchanger utilizes the cold air coming from two different airflows to cool the engine's hot parts. Its task is to maintain the air temperature at acceptable levels for a running engine.
The air-cooled oil cooler (ACOC) exchanger is a different story: this accessory is usually the airframer's responsibility and functions to cool the oil passing through the various lines of the entire engine. The ACOC draws cold air from the nacelle (the outer casing of the engine, on the fuselage) through the air vents and by means of special ejectors located on the heat exchanger terminal itself when the aircraft is stationary. The latter has wings and flat parts that are among the thinnest ever designed and manufactured at GE.
The Fuel Heater, the oil-to-fuel heat exchanger, does not cool but rather heats the fuel if its temperature drops below the 90°F (32°C) threshold by using the transmission gear oil. The oil heats the fuel, which can hit temperatures of 185°F, or 85°C, to optimize the fuel system performance.
The Advanced Turboprop’s heat exchangers are designed by CAD and made with additive manufacturing. Small parts such as valves, joints or inserts are then added to the heat exchangers. Avio Aero's engineering unit (in particular, the resident teams of Brindisi, Rivalta and Bari), work with the Aviation Technology Center in West Chester, Ohio, to coordinate the design of these small thermomechanical masterpieces. Besides making the Advanced Turboprop’s heat exchangers, Avio Aero is also involved in Engine Systems, Controls and Accessories, Combustion System and both power and accessories gearboxes for this first engine fully developed in Europe.
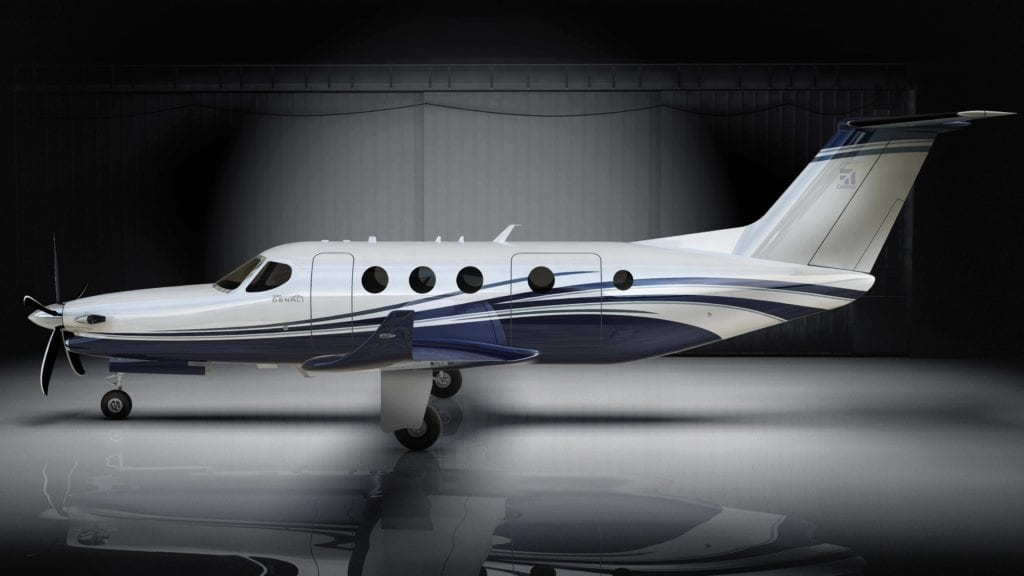