The GE9X has only one fan, but that doesn’t stop it from enjoying some serious star power. When GE brought the world’s largest jet engine to the Paris Air Show in 2019, visitors to its chalet mobbed it like a Hollywood actor and just couldn’t stop taking their picture with it.
At roughly 11 feet in diameter — wide as the body of a Boeing 737 — the giant fan is the engine’s most distinctive feature. It holds 16 sleek fan blades made from the latest generation carbon-fiber composite that is tough but lighter than titanium. The blades are so well engineered that New York’s Museum of Modern Art included its first generation, which GE developed for GE9X’s predecessor GE90 engine, in its design collection. The fan and other technology inside the engine, including 3D-printed parts and space-age materials called ceramic matrix composites, allow it to generate 100,000 pounds of thrust — several times more than many fighter jets and the rocket used in America’s first manned space flight. GE engineers developed the engine for Boeing’s new passenger jet, the 777X.
The GE9X engine and the plane it was designed for, the 777X, will be 20% more fuel-efficient than their predecessors. Recently that powerfully efficient engine got one step closer to service when the Federal Aviation Administration certified it. The certification, a key milestone, means GE can start making GE9X engines for commercial service.
So what is it like to fly one of these giant engines? Jon Ohman, who flew F-18 fighter jets before becoming GE Aviation’s chief test pilot, has firsthand experience with the GE9X. He spent 2018 and 2019 testing it in the skies above Victorville, California. It’s where GE keeps its Flying Test Bed, a modified Boeing 747 powered by three GE CF6 jet engines and, right now, the giant GE9X.
So, how exactly do Ohman and the test engineers account for the size, weight and thrust differentials? It’s one of the questions GE Aviation’s social media followers most wanted to know. We sat down with Ohman, the first person to fly a GE9X-powered jet, to find out the answer to this and other inquiries. Here’s an edited version of our conversation.
How do you balance the test plane with something as big as the GE9X engine on the wing? (The GE9X features world’s largest fan ever produced for a commercial aircraft at 134 inches (3.35 meters) in diameter.)
We use fuel as ballast to balance the weight of the GE9X and the unique pylon that mounts it to the wing. Our 747-400 is modified with a manual fuel transfer system that we can control from the cockpit. With the GE9X on the left wing we keep the number 3 reserve tank (in the right wing) full and the number 2 reserve tank (in the left wing) empty. This keeps weight relatively balanced laterally.
Why does GE Aviation test engines on a 747?
The 747 is an ideal test platform for our developmental jet engines, both big and small. With a test engine on the number 2 station, the three production CF6 engines and their associated engine driven systems (fuel pumps, hydraulic pumps, bleed air, electrical generators) provide plenty of redundancy for safe operations. With a small test engine, the three production engines provide enough power to reach all parts of the operational envelope. With a large test engine, we can use the two production engines on the opposite wing to counter the thrust of the large test engine and keep the overall thrust relatively symmetrical. Likewise, the large tail of the 747 combined with the long length of the fuselage (therefore a longer lever arm) allows us to better control the aircraft during situations with asymmetric thrust from a large engine like the GE9X.
The GE9X is the largest commercial aircraft engine in the world. Is it louder than other engines?
Although the GE9X is the world’s largest aircraft engine, it is designed to be quieter, cleaner, and 10 percent more efficient than its predecessor, the GE90, which currently powers the Boeing 777. The massive fan of the GE9X actually helps keep it quieter.
How do you balance performance calculations with one engine producing differential thrust?
For planning purposes, Boeing provides us with performance calculations for the unique configuration of our 747 with the variety of test engine we fly. With the GE9X producing significantly more thrust than a production CF6 engine, our takeoff and climb performance is excellent. With the GE9X and full takeoff thrust we actually have to reduce the thrust of the number 1 engine to ensure adequate directional control in the event of a failure of the number 4 engine. Cruise performance with respect to overall fuel burn is slightly higher than normal mainly due to additional drag from our asymmetric configuration.
Is it possible for a 747-8 to operate on two GE9Xs? Are the GE9Xs more powerful than four of the 747-8 GEnx engines?
The GE9X is currently rated at 105,000 lbs thrust. The four GEnx-2B engines on the 747-8 are rated at 66,500 lbs thrust each, so two GE9Xs would not provide the same thrust. Also, the 747-8 is designed as a four-engine airplane with redundant electrical, hydraulic, and bleed air systems powered by each of the four engines.
The GE9X engine hangs low on the test plane, how does ground clearance work with this configuration?
Mounting an engine of this size to our 747-400 is a challenge. The engine is mounted on a unique pylon that cantilevers the engine out in front of the wing and tilts it upward by approximately 7 degrees. Also, we over-service our landing gear struts to extend them more than normal and provide an additional 4 inches of clearance. The result is about 18 inches of clearance between the bottom of the nacelle and the ground when the airplane is sitting stationary. Given the relatively small clearance we are very careful during landings, particularly in crosswinds.
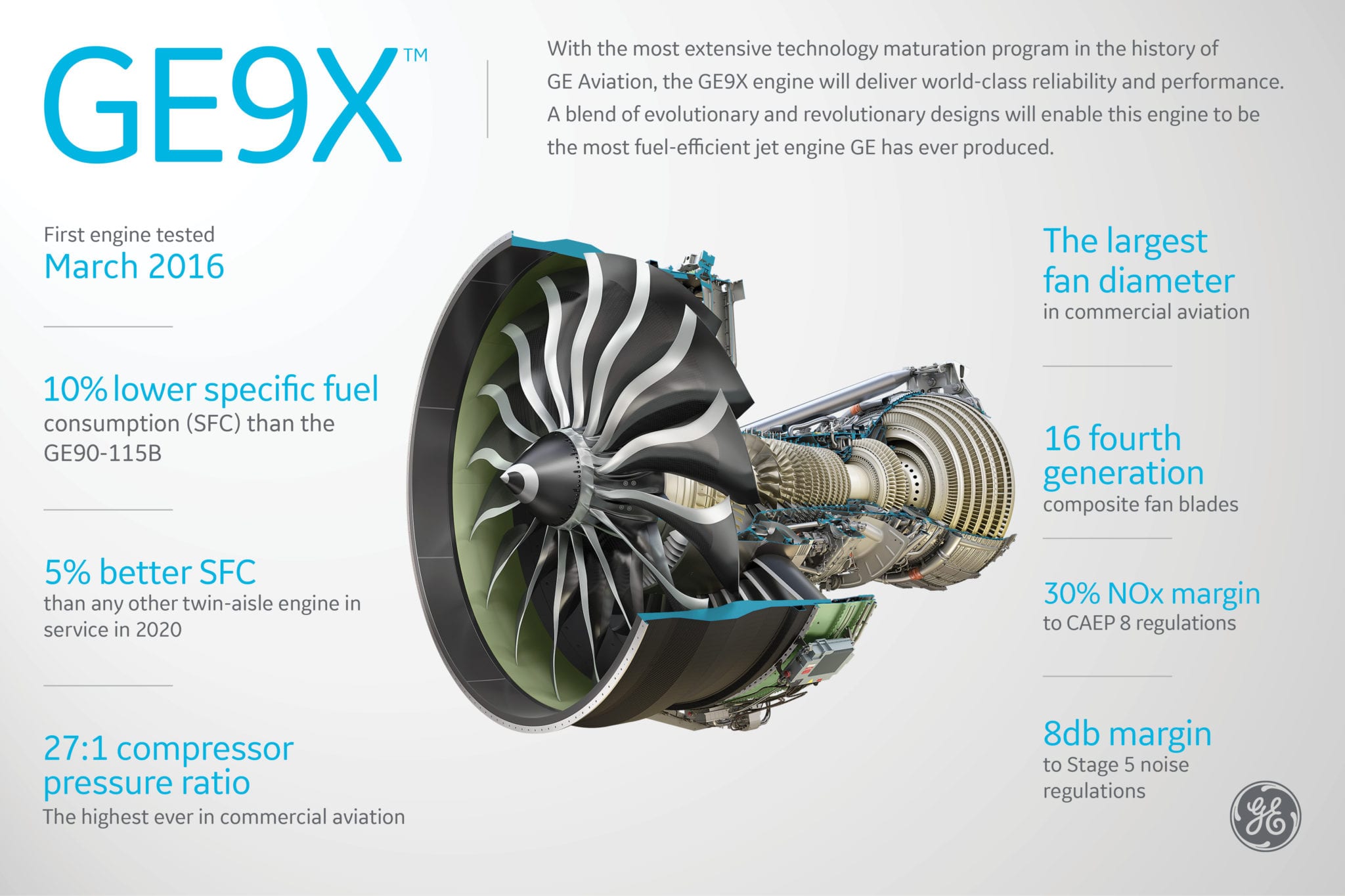
At roughly 11 feet in diameter — wide as the body of a Boeing 737 — the giant fan is the engine’s most distinctive feature. It holds 16 sleek fan blades made from the latest generation carbon-fiber composite that is tough but lighter than titanium. The blades are so well engineered that New York’s Museum of Modern Art included its first generation, which GE developed for GE9X’s predecessor GE90 engine, in its design collection. The fan and other technology inside the engine, including 3D-printed parts and space-age materials called ceramic matrix composites, allow it to generate 100,000 pounds of thrust — several times more than many fighter jets and the rocket used in America’s first manned space flight. GE engineers developed the engine for Boeing’s new passenger jet, the 777X.
The GE9X engine and the plane it was designed for, the 777X, will be 20% more fuel-efficient than their predecessors. Recently that powerfully efficient engine got one step closer to service when the Federal Aviation Administration certified it. The certification, a key milestone, means GE can start making GE9X engines for commercial service.
So what is it like to fly one of these giant engines? Jon Ohman, who flew F-18 fighter jets before becoming GE Aviation’s chief test pilot, has firsthand experience with the GE9X. He spent 2018 and 2019 testing it in the skies above Victorville, California. It’s where GE keeps its Flying Test Bed, a modified Boeing 747 powered by three GE CF6 jet engines and, right now, the giant GE9X.
So, how exactly do Ohman and the test engineers account for the size, weight and thrust differentials? It’s one of the questions GE Aviation’s social media followers most wanted to know. We sat down with Ohman, the first person to fly a GE9X-powered jet, to find out the answer to this and other inquiries. Here’s an edited version of our conversation.
Ohman, based in Victorville, CA, has captained test campaigns for LEAP-1A and LEAP-1B, GEnx-1B, and the GE9X engine programs.
How do you balance the test plane with something as big as the GE9X engine on the wing? (The GE9X features world’s largest fan ever produced for a commercial aircraft at 134 inches (3.35 meters) in diameter.)
We use fuel as ballast to balance the weight of the GE9X and the unique pylon that mounts it to the wing. Our 747-400 is modified with a manual fuel transfer system that we can control from the cockpit. With the GE9X on the left wing we keep the number 3 reserve tank (in the right wing) full and the number 2 reserve tank (in the left wing) empty. This keeps weight relatively balanced laterally.
Why does GE Aviation test engines on a 747?
The 747 is an ideal test platform for our developmental jet engines, both big and small. With a test engine on the number 2 station, the three production CF6 engines and their associated engine driven systems (fuel pumps, hydraulic pumps, bleed air, electrical generators) provide plenty of redundancy for safe operations. With a small test engine, the three production engines provide enough power to reach all parts of the operational envelope. With a large test engine, we can use the two production engines on the opposite wing to counter the thrust of the large test engine and keep the overall thrust relatively symmetrical. Likewise, the large tail of the 747 combined with the long length of the fuselage (therefore a longer lever arm) allows us to better control the aircraft during situations with asymmetric thrust from a large engine like the GE9X.
A peak under the hood of the GE9X engine.
The GE9X is the largest commercial aircraft engine in the world. Is it louder than other engines?
Although the GE9X is the world’s largest aircraft engine, it is designed to be quieter, cleaner, and 10 percent more efficient than its predecessor, the GE90, which currently powers the Boeing 777. The massive fan of the GE9X actually helps keep it quieter.
How do you balance performance calculations with one engine producing differential thrust?
For planning purposes, Boeing provides us with performance calculations for the unique configuration of our 747 with the variety of test engine we fly. With the GE9X producing significantly more thrust than a production CF6 engine, our takeoff and climb performance is excellent. With the GE9X and full takeoff thrust we actually have to reduce the thrust of the number 1 engine to ensure adequate directional control in the event of a failure of the number 4 engine. Cruise performance with respect to overall fuel burn is slightly higher than normal mainly due to additional drag from our asymmetric configuration.
Is it possible for a 747-8 to operate on two GE9Xs? Are the GE9Xs more powerful than four of the 747-8 GEnx engines?
The GE9X is currently rated at 105,000 lbs thrust. The four GEnx-2B engines on the 747-8 are rated at 66,500 lbs thrust each, so two GE9Xs would not provide the same thrust. Also, the 747-8 is designed as a four-engine airplane with redundant electrical, hydraulic, and bleed air systems powered by each of the four engines.
A close-up of the specially designed GE9X pylon for the Flying Test Bed.
The GE9X engine hangs low on the test plane, how does ground clearance work with this configuration?
Mounting an engine of this size to our 747-400 is a challenge. The engine is mounted on a unique pylon that cantilevers the engine out in front of the wing and tilts it upward by approximately 7 degrees. Also, we over-service our landing gear struts to extend them more than normal and provide an additional 4 inches of clearance. The result is about 18 inches of clearance between the bottom of the nacelle and the ground when the airplane is sitting stationary. Given the relatively small clearance we are very careful during landings, particularly in crosswinds.
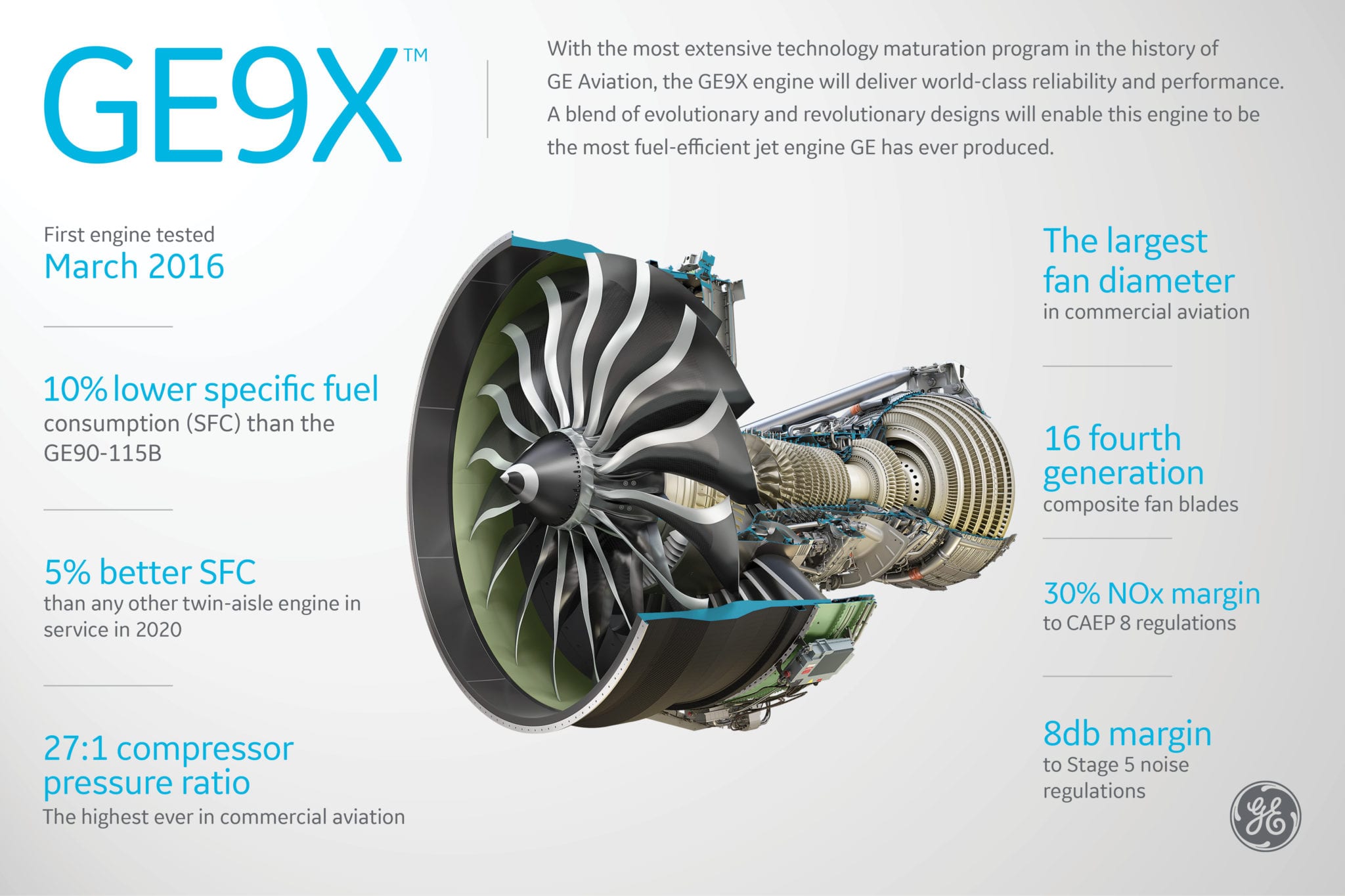