A Journey of Continuous Improvement: The Transformation of On Wing Support in Shanghai
September 26, 2024 | by GE Aerospace News Staff
At the heart of Shanghai Lingang Aviation Industrial Park, where innovation meets industrial prowess, lies GE Aerospace’s On Wing Support (OWS) facility in Shanghai. Officially opened last July, the 69,000-square-foot (6,400-square-meter) facility is the youngest of the seven On Wing Support (OWS) sites in the world and the first quick-turn shop of its kind in China. With its establishment, GE Aerospace’s customers in China will be able to expect quicker engine repairs and reduced turnaround time, with significantly lower costs.
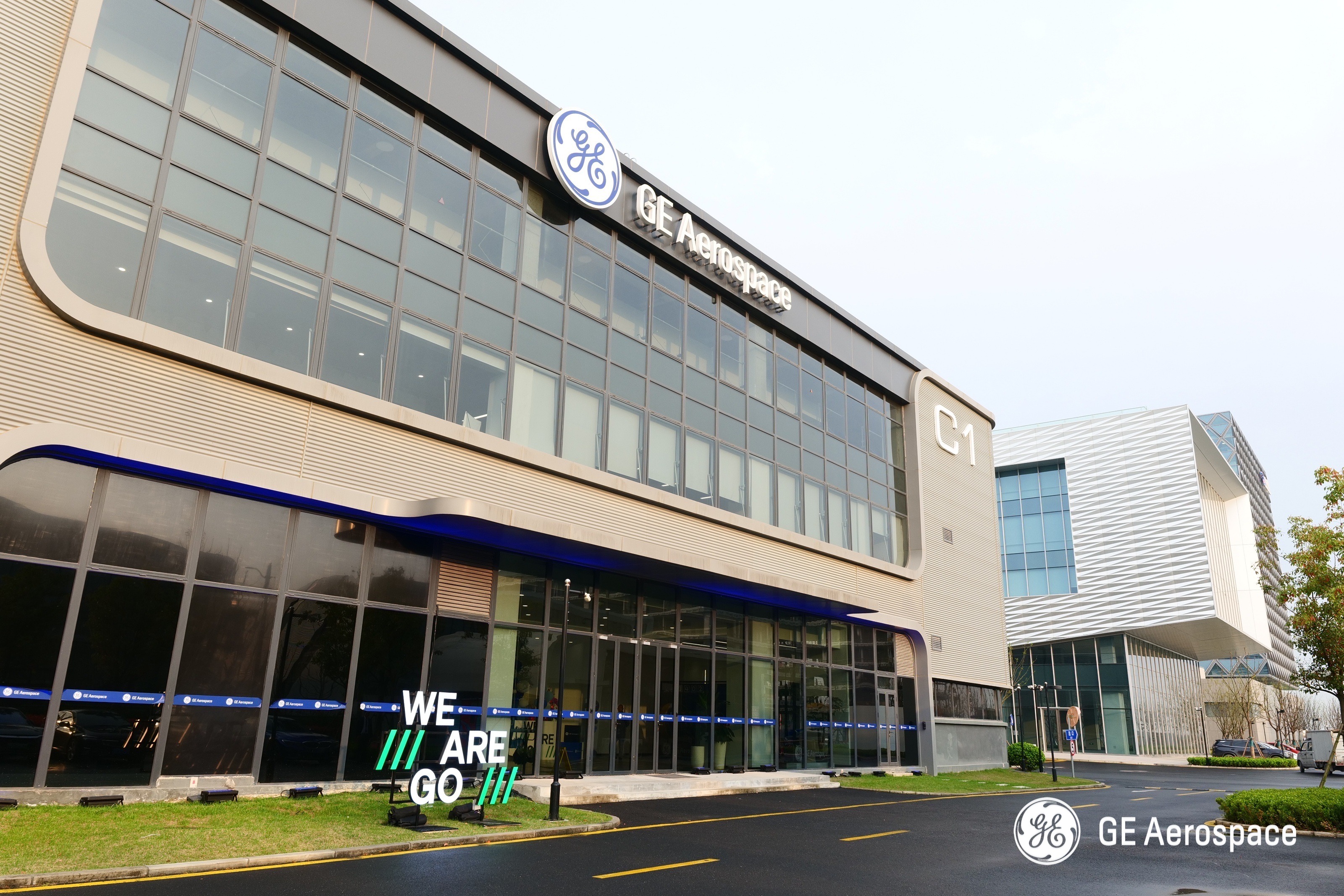
Building from the Ground Up: The Unique Challenges
As a newly established facility, the OWS facility in Shanghai had its work cut out for it. Unlike other OWS sites, the facility faced highly diverse customer needs in a complex market. Though the team had clear goals and had laid out plans to reach them, it encountered several challenges, including missing engine inputs, field job inefficiency, and extended billing turnaround times. And the trend was not heading in the right direction. Site Manager Wang Tao recognized that to solve the problems and drive results, his team would need to act quickly. So they turned to FLIGHT DECK, GE Aerospace’s proprietary lean operating system, which was launched in February.
After rounds of internal analysis, discussion, and preparation, the OWS team in Shanghai invited the GE Aerospace China Leadership Council, lean leaders from the Suzhou manufacturing plant, and cross-functional key process owners such as HR, Sourcing, the Custom and Transportation Organization, and Software Engineering to their shop floor for two business-process kaizen events in May and June. The 30 participants were divided into four groups focused on identifying and addressing key issues across safety, quality, delivery, inventory, and productivity, resulting in a total of 61 action items for improvement.
Central to those improvements was the rigorous implementation of standard work processes, particularly in the areas of safety and quality. “One of the problems that troubles me a lot is the time wasted during fieldwork, waiting for the right, compliant tools,” says Lu Jiangang, a field engineer who has been working at OWS Shanghai for 16 years. “And this happens a lot, not only to me.”
“Either the tools are not there or they don’t meet our safety standard,” adds his colleague Gao Zewen. After receiving employee input and analyzing potential causes, the group proposed an action item to create a checklist comprising both job preparation and environmental health and safety (EHS) for engineers to verify against before they start a field job for a customer. Only 49 days later, this action item was closed and the checklist became part of the Safety Management System. Now tool safety is verified before work begins, significantly reducing downtime and improving efficiency.
A total of 19 action items for safety improvement were proposed, including purchasing a electrical TOW cart for engine/module movements in the shop, to reduce ergonomic risk, and the modification of a forklift warning light to ensure better visibility and awareness. All the items were completed by July 5.
One of the most critical quality risks in the shop is foreign object debris (FOD), a serious circumstance that can delay engine delivery. After the team went to genba — a lean term meaning “the place where work is done” — they discovered a FOD-related risk. The employee workstation sits very close to the engines in the maintenance bay, and some workers were putting their personal items, like bags, on the desk. If those items fell to the floor near the engine, it could have resulted in a FOD incident. After seeing this, the team suggested temporary countermeasures, such as immediate removal of the personal items, and proposed to improve the genba checklist for FOD prevention.
“We will add ‘personal belonings’ to the existing FOD risk-and-management procedure and strengthen our 5S requirement,” Wang Tao said after hearing suggestions from the team. The facility’s break area now houses an entire row of cabinets that sit far from the maintenance bay. This improvement contributed to better organization and tidiness in the bay area, vastly reducing the chance of a FOD event and ensuring the high quality standards required in engine services.
As part of the quality-related action items, OWS Shanghai also introduced a “Monthly Most Valuable Quality Concern Reports” award and named its first winner, technician Li Shengjia, for his proactive approach in identifying and addressing quality concerns. The changes gradually taking place at OWS Shanghai underscore GE Aerospace’s unwavering commitment to continuous improvement.
The Power of FLIGHT DECK
The lessons learned from the kaizen events were clear: to ensure safety and quality while making rapid changes guided by standard work and problem-solving — two key FLIGHT DECK fundamentals in process conversion, shop layout, and personnel training. “Standard work” refers to demonstrated best practices for completing a given process. By embracing the standard process practices, the team has been able to adapt to market changes and complex customer needs quickly. For instance, the unexpected delay by Boeing in returning the 737 MAX to service disrupted the team’s original work plan, but thanks to standard practices they had already set up, after retooling and retrofitting the shop and maintenance bays, the team was able to quickly shift the unused capacity to unscheduled engine removals on the LEAP-1A and CFM56 engines. This agile approach ensures that the facility can remain resilient while capable of meeting the evolving needs of its airline customers.
The OWS facility in Shanghai has also been leveraging a new slot tracker platform, which is in place for customer program managers and the global OWS team to seamlessly share engine slot demands and availabilities between the two teams in real time. This innovation is already driving results in delivery, with nine engine inductions confirmed at the OWS facility in Shanghai in the third quarter alone — matching the total number of inductions achieved in the entire first half of the year.
Out of the 61 improvement actions identified during their kaizen events, 49 were completed within 60 days, and at their 90-day review, 58 had been carried out — a completion rate of 95%. FLIGHT DECK is helping the OWS team in Shanghai run their business better, and they have no plans to stop now.