We Spy With Our Little Eyes: How White Light Inspection Robots Are Bringing New Efficiency and More Consistency to the MRO Shop
August 27, 2024 | by Chris Norris
GE Aerospace technicians are about to have a powerful new set of hands — and eyes — on the team. Opening this fall, the Services Technology Acceleration Center (STAC), five miles from the Cincinnati headquarters, will be the first site to deploy AI-guided “white light robot” inspection in its maintenance, repair, and overhaul (MRO) shop. The quietly dazzling innovation brings revolutionary technology to some of the most crucial yet laborious work in aviation.
The product of a five-year joint effort by engineers at GE Aerospace Research in Niskayuna, New York, and GE Aerospace’s Global Automation and Robotics Center in Bromont, Quebec, this robotic inspection process will spearhead GE Aerospace’s broader, decade-plus-long AI development effort. “By using AI and robotics, service engineers can increase the speed and efficiency of part inspections while improving the consistency of their results,” says Jon Hootman, GE Aerospace’s engineering director of the Services Technology Acceleration Center. “This also represents the first time as a business that we’re able to fully capture, digitally, all characteristics of a part in service and catalog the data throughout the part’s lifetime in service in a centralized repository.”
Easier on the Eyes with AI
Some of an aircraft’s most critical parts are located at the very center of its power, like the exquisitely machined nickel-based disks that bear the blades of a jet engine’s high-pressure turbine (HPT). Spinning at tremendous speeds near the engine’s core, these high-precision HPT disks require painstaking scrutiny of their surfaces, accounting for every dent, fretting, scratch, or bit of corrosion. Even the most minor anomaly on such life-limited parts (LLP) requires professional eyes to determine which engineering disposition applies — whether it should be accepted, repaired, or rejected. But these eyes typically belong to a single human being, and it can be tiring.
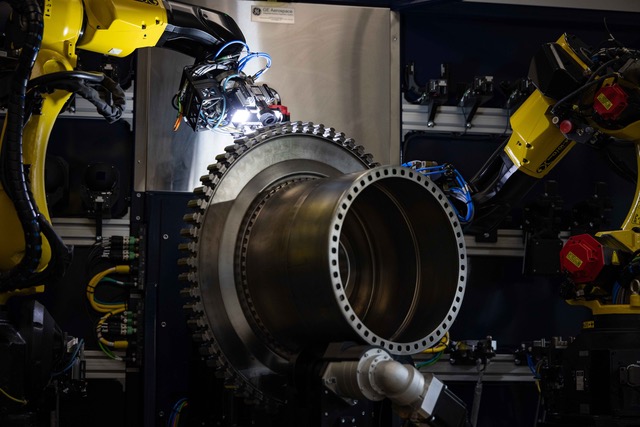
“First of all, staring at the same part or feature for 8 to 12 hours a day can make your head hurt,” says Sam Blazek, GE Aerospace services technology leader for white light inspection, who has worked at the company for seven years. Nor is the platform exactly ideal. “It’s a fixed rotational positioner that you can move up or down — that’s it,” says Blazek, who, prior to joining Hootman’s team two years ago, inspected parts “caveman style,” he says: by hand, with a flashlight and mirror. “You’re constantly twisting your head, eyes, and neck as you manipulate mirrors and flashlights to focus on each individual feature of the parts, and the interpretation of what the inspector sees is as variable as the humans doing the physical work.”
AI-guided white light robot inspection solves this seemingly intractable problem, while providing a path toward similar solutions in other realms of MRO. Standing in a universal workstation, two articulated industrial robots outfitted with white light optical scanners move closely over the entire surface of the high-precision part — say, a turbine disk for a GE-90 engine. Like two avant-garde dancers, the robots’ movements are carefully choreographed by human operators and use AI to capture and analyze data with optimum accuracy, speed, and consistency, simultaneously creating a digital record of the condition of the part.
By performing each inspection “mission” on a standard digital platform, they ensure a consistent flow and management of extremely fine-grained information. They record the part’s serial number (thus capturing provenance, location, and history), assign a numerical value to each anomaly found (crack, nick, dent, fretting), develop a consistent chronological narrative of the part (hosted in the cloud and instantly accessible anywhere in the world), indicate where new inspection limits or repairs might be developed in order to make the part serviceable, and provide a complete record of non-serviceable inspection findings that will point to more cost-effective solutions for future customers’ shop visits.
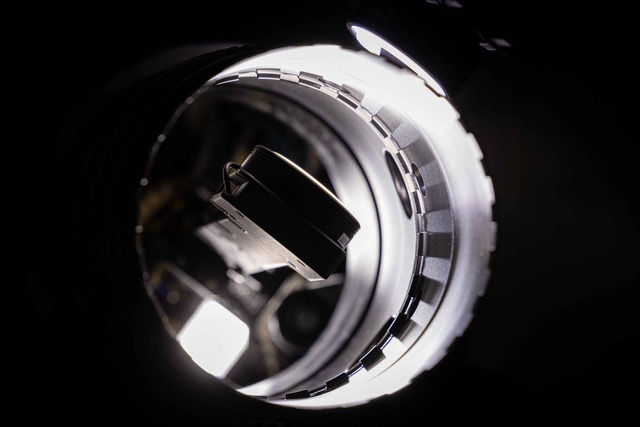
“The beauty is that all of this together now pulls in the entire value stream to eradicate inconsistencies in your interpretation,” says Hootman. “[It allows us] to make sure that we are applying the appropriate level of consistency and interpretation to the anomalies in question and give our customers a consistent experience, whether their asset is being overhauled in Malaysia or Brazil.”
Freeing Up Humans to Do What They Do Best
While the first generation of this technology captured images and digitally stitched them together, Hootman’s team soon turned to line-scan cameras developed at GE Aerospace Research, which provide a higher-quality, video-like stream that replicates what a human being can see, displayed on a computer monitor. When Blazek joined the team, his deep domain expertise helped them develop the policies and procedures that, along with AI’s sophisticated data storage, make it possible to scale and produce the second-gen system.
Once programmed and activated, the system doesn’t need to be scrutinized for its entire operation time. “The goal is to mount a part for inspection, hit ‘go,’ let the system run while you go do another job, and come back to monitor the inspection on a screen,” says Blazek. “A person still needs to be there to examine the screen and make the call. They just don’t need to physically huddle around the part for hours on end to collect the data. We use their expertise where it’s needed, which is in disposition.”
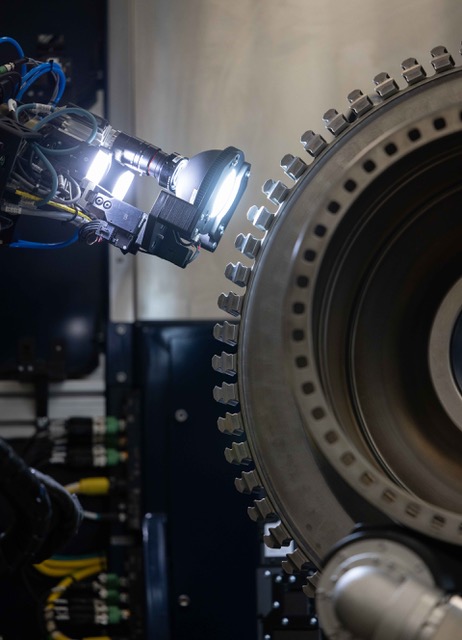
The white light robot inspection will reduce the noise from variations between human inspectors, whom it will also help to train. Rather than rely on predictions or simulations of an LLP’s likely wear and tear, this data provides high-resolution information about the actual part. “So it’s really the best leading indicator program on the face of the globe,” says Hootman.
It also holds promise to enable cost-effective automation solutions well outside of white light inspection, like cleaning, thermal spray, and blending operations. “As cool as the inspection robots are, the digitized inspection results at piece-part level are equally important,” says Hootman. “My ability to have high-quality, consistent, repeatable mapping of the inspection results on a specific part is the magic. It’s the enabler to simplify the programming and logic for all sorts of post-inspection automation opportunities that we could leverage in the future.”
Of course, it’s worth noting that none of this means an absolute total automation of aircraft part inspection, which will always remain too crucial to turn over to machines, even intelligent ones. “We’re not trying to replace humans with this technology,” Blazek says. “We want to replicate them. If we can automate some of the ‘easier’ repeatable, predictable aspects of this job, it frees our inspectors to focus on the technical issues that truly need our attention.”