Factory floor to classroom: GE Aviation managers in growing Auburn plant share teaching duties with Alabama State Training program
March 23, 2018
Joseph Moore works days on the shop floor at GE Aviation’s fast-growing jet engine factory in Auburn – then teaches his experiences at night in the classroom.
He’s one of several operations managers at GE’s Auburn site with a teaching role during the month-long vocational training sessions at Southern Union State Community College near Auburn to prepare GE’s growing foster of hourly workers.
About four sessions are held annually to handle the demand for more trained workers in the GE Auburn factory. In addition to the Southern Union instructors, the program includes Moore and his GE colleagues each leading a three-hour evening of instruction each week.
“I really enjoy the interaction,” says Moore, who teaches lean manufacturing, Six Sigma quality practices, and compliance. “Being part of the training also allows us to get a good look at the people we are evaluating for positions at the plant.”
The close cooperation between GE Aviation, Southern Union, and the Alabama Department of Commerce is another example of GE Aviation preparing workers for the skill sets required in its new modern factories across the U.S.
GE’s Auburn facility uses sophisticated equipment to machine advanced turbine airfoils and structural components for jet engines. Machine operators vying for positions are first trained at Southern Union with a curriculum developed by the Alabama Industrial Development Training (AIDT) division and by local GE plant leaders.
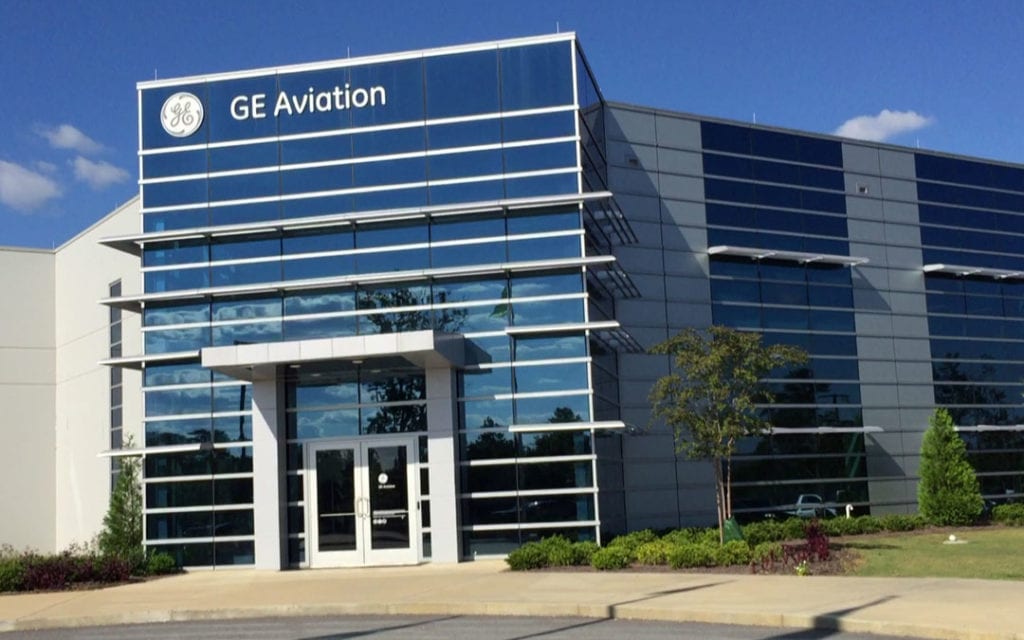
GE is actively involved in the training process because GE Auburn is ramping up fast. Employment reached 200 people in March and is expected to grow to 280 by year’s end, according to plant manager Ricardo Acevedo.
GE Auburn produces components for the fastest-selling jet engine in commercial aviation history, the “LEAP” engine for CFM International, the 50/50 joint company of GE and Safran Aircraft Engines of France.
More than 14,000 LEAP engines are on back order to power three airplanes: the Airbus Industrie A320neo, Boeing 737 MAX, and China’s COMAC C919. The Airbus and Boeing airplanes are now in airline service. The GE and Safran factories delivered 459 LEAP engines in 2017. The LEAP delivery goal for 2018 is up to 1,200 engines, and in the 1,800-engine range in 2019.
In addition to machining parts, the Auburn site this year will produce more than 34,000 fuel nozzle injectors for the LEAP engine using laser-powder, additive manufacturing machines. Auburn’s 37 additive machines is expected to grow to 45 by mid-year to handle the needed higher volume.
https://www.youtube.com/watch?v=kKQ5KwFwW_s
These employees require six weeks of in-house training. GE is looking at ways to engage the local community colleges in offering additive manufacturing as part of their curriculum. GE Aviation is also engaging with engineering students at Auburn University in additive manufacturing projects.
Training for GE’s Auburn employees is not limited to community college classes. The plant also offers training in non-destructive testing where employees become certified to evaluate jet engine components scanned in advanced X-ray machines. “There’s a skills shortage in this field,” says Tory Landry, the plant’s human relations leader. “It’s hard to find the people. We offer in-house training to candidates who can then experience a significant pay increase.”
Among the factors Acevedo attributes to high retention at the plant is the GE investment in training. “There are great careers in advanced manufacturing,” he says.
Over the past decade, GE Aviation has opened eight new facilities in the United States, including the new factory in Auburn. Other locations include Asheville, North Carolina; Lafayette, Indiana; and Huntsville, Alabama. Over the past seven years, GE Aviation has invested more than $4.5 billion in its U.S. manufacturing operations.
GE Aviation, an operating unit of GE (NYSE: GE), is a world-leading provider of jet and turboprop engines, components and integrated systems for commercial, military, business and general aviation aircraft. GE Aviation has a global service network to support these offerings.
https://www.youtube.com/watch?v=hXRJ_2s622E
He’s one of several operations managers at GE’s Auburn site with a teaching role during the month-long vocational training sessions at Southern Union State Community College near Auburn to prepare GE’s growing foster of hourly workers.
About four sessions are held annually to handle the demand for more trained workers in the GE Auburn factory. In addition to the Southern Union instructors, the program includes Moore and his GE colleagues each leading a three-hour evening of instruction each week.
“I really enjoy the interaction,” says Moore, who teaches lean manufacturing, Six Sigma quality practices, and compliance. “Being part of the training also allows us to get a good look at the people we are evaluating for positions at the plant.”
The close cooperation between GE Aviation, Southern Union, and the Alabama Department of Commerce is another example of GE Aviation preparing workers for the skill sets required in its new modern factories across the U.S.
GE’s Auburn facility uses sophisticated equipment to machine advanced turbine airfoils and structural components for jet engines. Machine operators vying for positions are first trained at Southern Union with a curriculum developed by the Alabama Industrial Development Training (AIDT) division and by local GE plant leaders.
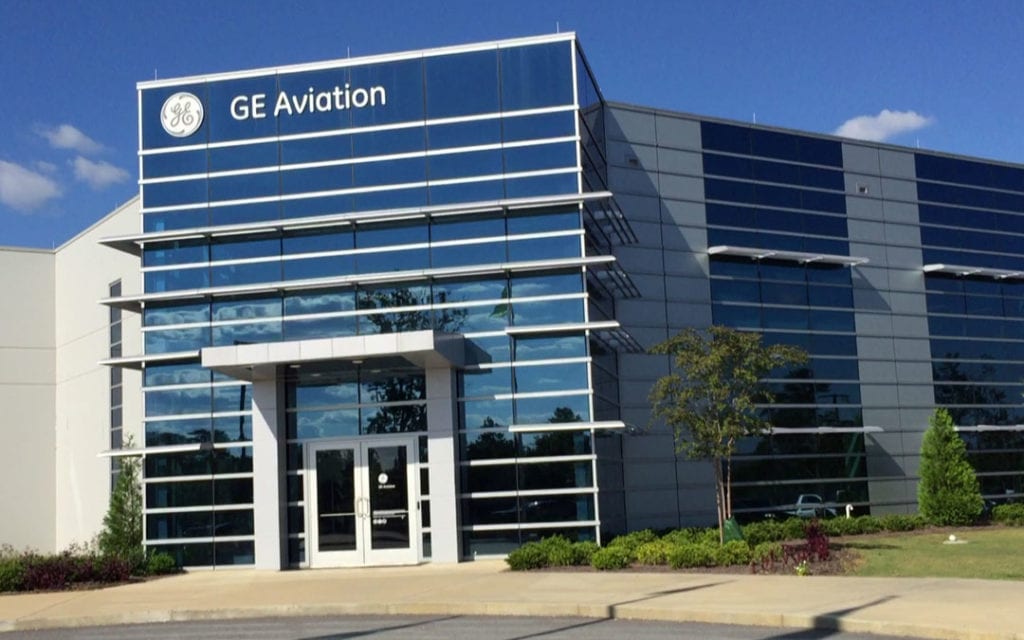
GE is actively involved in the training process because GE Auburn is ramping up fast. Employment reached 200 people in March and is expected to grow to 280 by year’s end, according to plant manager Ricardo Acevedo.
GE Auburn produces components for the fastest-selling jet engine in commercial aviation history, the “LEAP” engine for CFM International, the 50/50 joint company of GE and Safran Aircraft Engines of France.
More than 14,000 LEAP engines are on back order to power three airplanes: the Airbus Industrie A320neo, Boeing 737 MAX, and China’s COMAC C919. The Airbus and Boeing airplanes are now in airline service. The GE and Safran factories delivered 459 LEAP engines in 2017. The LEAP delivery goal for 2018 is up to 1,200 engines, and in the 1,800-engine range in 2019.
In addition to machining parts, the Auburn site this year will produce more than 34,000 fuel nozzle injectors for the LEAP engine using laser-powder, additive manufacturing machines. Auburn’s 37 additive machines is expected to grow to 45 by mid-year to handle the needed higher volume.
Learn more about additive manufacturing:
https://www.youtube.com/watch?v=kKQ5KwFwW_s
These employees require six weeks of in-house training. GE is looking at ways to engage the local community colleges in offering additive manufacturing as part of their curriculum. GE Aviation is also engaging with engineering students at Auburn University in additive manufacturing projects.
Training for GE’s Auburn employees is not limited to community college classes. The plant also offers training in non-destructive testing where employees become certified to evaluate jet engine components scanned in advanced X-ray machines. “There’s a skills shortage in this field,” says Tory Landry, the plant’s human relations leader. “It’s hard to find the people. We offer in-house training to candidates who can then experience a significant pay increase.”
Among the factors Acevedo attributes to high retention at the plant is the GE investment in training. “There are great careers in advanced manufacturing,” he says.
Over the past decade, GE Aviation has opened eight new facilities in the United States, including the new factory in Auburn. Other locations include Asheville, North Carolina; Lafayette, Indiana; and Huntsville, Alabama. Over the past seven years, GE Aviation has invested more than $4.5 billion in its U.S. manufacturing operations.
GE Aviation, an operating unit of GE (NYSE: GE), is a world-leading provider of jet and turboprop engines, components and integrated systems for commercial, military, business and general aviation aircraft. GE Aviation has a global service network to support these offerings.
Get to know GE Aviation's additive production facility in Auburn, Alabama:
https://www.youtube.com/watch?v=hXRJ_2s622E