Keep the Line Moving: GE Aerospace’s Lynn Facility Is Using FLIGHT DECK to Put Safety First
January 07, 2025 | by Jay Stowe
Imagine you’re an environmental, health, and safety (EHS) leader at a GE Aerospace site and, on the last Friday of the quarter, you get a call from a team member informing you that a key overhead crane used every day in the engine assembly area has to be shut down — immediately — for safety reasons.
At GE Aerospace’s jet engine production facility in Lynn, Massachusetts, that’s exactly what happened last spring. And what transpired is a great example of the team using FLIGHT DECK, the company’s proprietary lean operating model, to maintain safety protocols while also finding a solution that enabled them to keep delivering for the customer.
What happened: Safety first, driven by FLIGHT DECK
The Lynn facility has been up and running for 130 years, a true testament to its heritage at GE Aerospace and the vital role it plays in the defense aviation industry. “Our plant is recognized as a U.S. Department of Defense facility that designs, produces, assembles, and tests military and commercial aircraft engines and components,” says Lynn Site Leader John McCarron. So when an arch beam crane is suddenly flagged for safety reasons, it gets your attention.
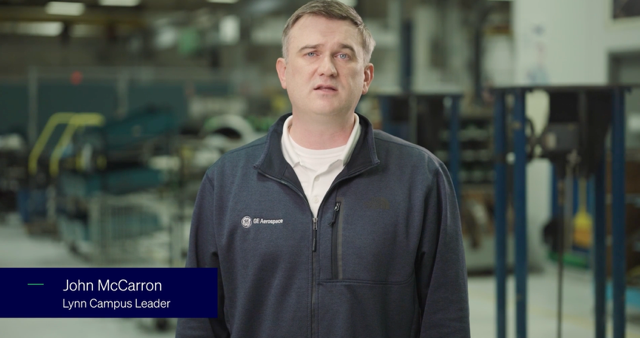
After quickly reviewing the situation, it was “determined that we needed to safely shut down the cranes per the original equipment manufacturer recommendation,” says Matt Allen, combustors and structural components (CSC) infrastructure leader and EHS leader at the site. “To John’s credit, he immediately made a decision to shut down the crane system across the campus.”
But now they needed to find a solution to keep the assembly line operating. Enter Bobby Eldridge, a servicer in Lynn’s assembly and test operations and executive board member of the IUE-CWA Local 201. When Allen and McCarron told him what happened, he thought it was an April Fools’ prank. “I really thought they were joking,” he recalls. “But they were 100% right. Safety first, but also getting the engines out to the customer is a second priority.” In the spirit of continuous improvement and being customer-driven — two FLIGHT DECK fundamentals — Eldridge quickly identified another crane that could be shifted into position and put to use, and within 10 minutes they had operations running again. “We didn’t miss [shipping] an engine,” he says.
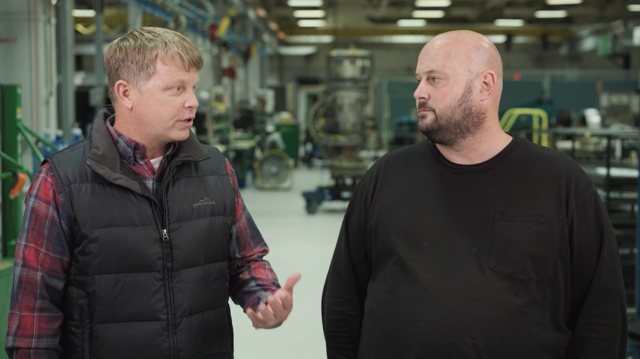
Why it matters: Continuous improvement mindset is helping the GE Aerospace team get a little bit better every day
After carrying out some enhanced inspection protocols, Allen says they were able to safely restart the cranes in question. But in the long term, the plan is to replace all of the arch beam cranes across the Lynn campus by the end of 2025. As McCarron points out, collaborative problem-solving like this, coupled with a continuous improvement mindset, has helped the facility bring its illness and injury rate down by 55% since 2022.
Watch the video below to get the full story of how the team at Lynn is using FLIGHT DECK to keep the production line moving safely.