A Great Leap Forward: Celebrating the CFM LEAP Engine’s Legacy of Innovation
February 29, 2024 | by Jay Stowe
This being Leap Day, it seems appropriate to celebrate one of the most popular commercial aircraft propulsion systems on the market today: the CFM LEAP engine. Built to fit all variants of Airbus A320neo, Boeing 737 MAX, and COMAC C919 passenger jets, the LEAP engine entered service in 2016 and quickly made good on its promise to increase fuel efficiency, reduce noise and CO2 emissions, and enable high aircraft utilization rates. To date, it has maintained a 15% to 20% improvement in fuel efficiency over its immediate predecessor (the CFM56 engine) and has delivered best-in-class departure reliability rates for commercial operators around the world. In fact, the engine’s double-digit fuel efficiency gains allow planes to fly farther on a single tank of fuel while lowering carbon and nitrogen oxide emissions. (CFM56 and LEAP engines are products of CFM International, a 50-50 joint company between GE Aerospace and Safran Aircraft Engines.)
The LEAP engine program is off to a fantastic Leap Year, with several highlights in the first two months of 2024:
Last week at the Singapore Airshow, a China Eastern Airlines COMAC C919 narrow-body airliner made its international debut, flying over the Changi Exhibition Center powered by CFM LEAP-1C engines. It was the Chinese-made jet’s first flight outside of Chinese territory. At the air show, Tibet Airlines finalized an order for 40 COMAC C919 aircraft.
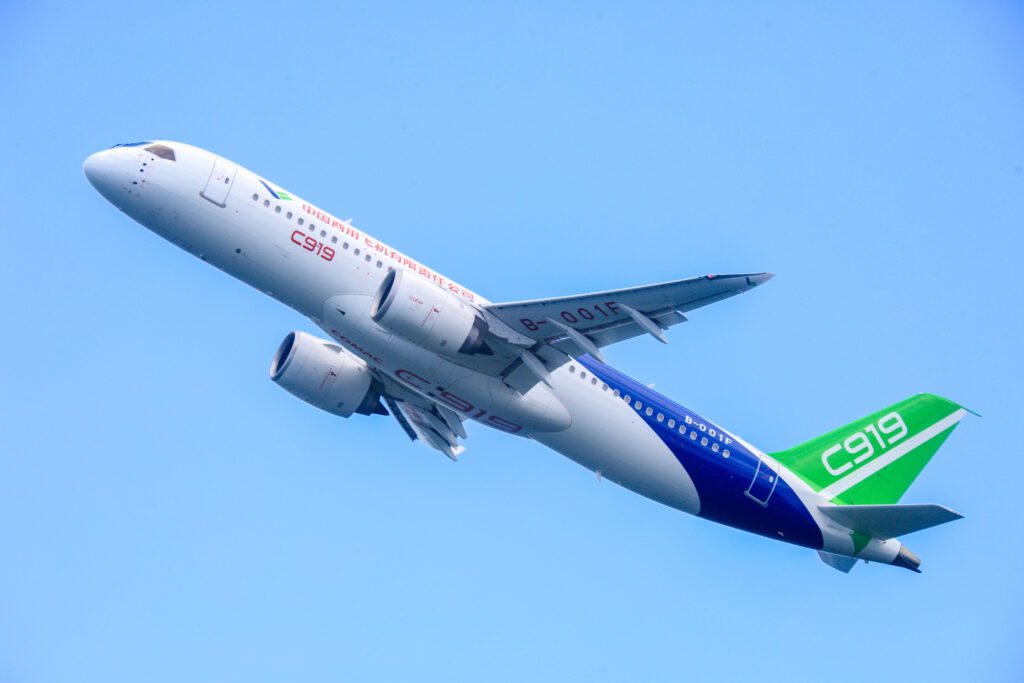
In January, CFM scored two significant new deals that represent a vote of confidence in LEAP performance and reliability. First, easyJet, a low-cost carrier with a strong presence in Europe, ordered more than 300 CFM LEAP-1A engines to power its fleet of 56 Airbus A320neo and 101 Airbus A321neo aircraft. Then Akasa Air, based in India, agreed to purchase more than 300 CFM LEAP-1B engines for its fleet of 150 Boeing 737 MAX jets.
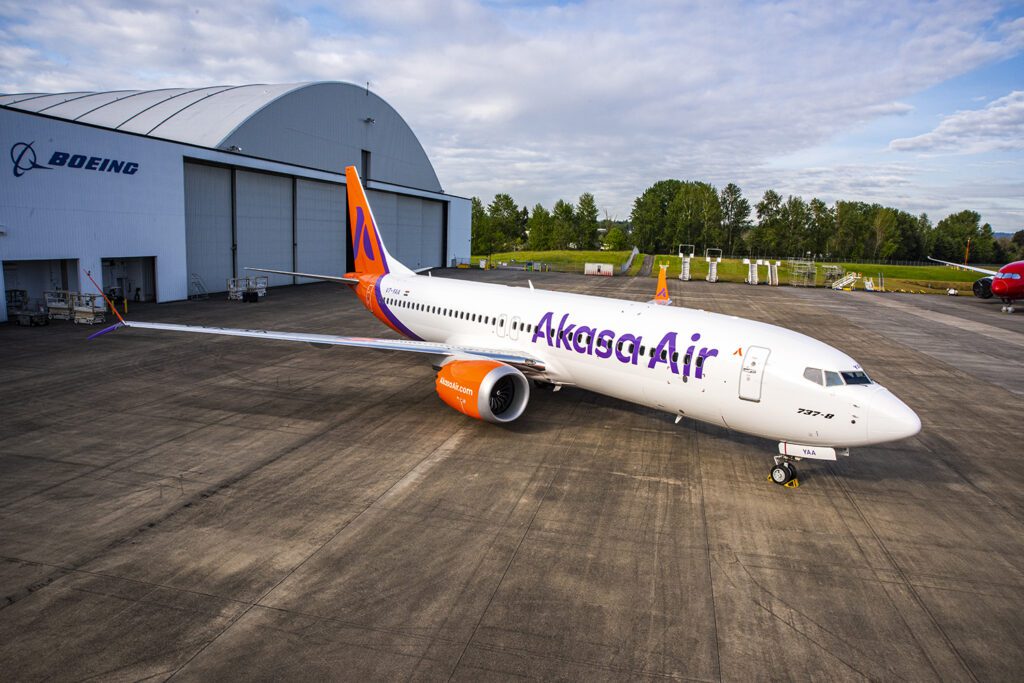
In hot and harsh climates like the Middle East, fine particulate matter floating in the air can wear down the inner workings of a jet engine over time. To combat this perennial challenge, GE has taken research conducted over the past 15 years and developed its own homemade testing powder (which the engineers affectionately call “pixie dust”) to blow into engines in test cells. Combined with advanced analytics on millions of hours of LEAP engine field experience, the company has run thousands of hours of dust ingestion tests that have been able to exactly replicate what customers have been seeing in service. “Our dust testing has shown that our more durable turbine blade design is working as intended,” says Natalie Stone, director of LEAP material solutions at GE Aerospace. “With LEAP-1A testing complete and LEAP-1B testing just started, we’re on track to introduce the improved blade to our customers later this year.”
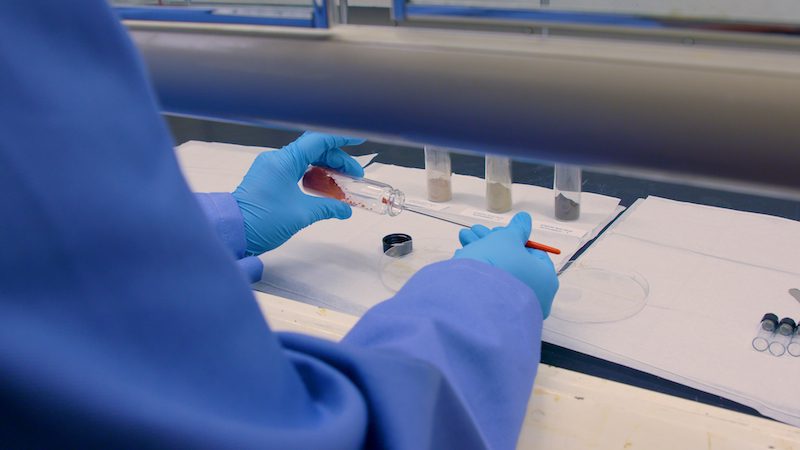
In addition to rigorous testing and a relentless focus on reliability, what’s the secret to the LEAP engine’s success? Years of research and development and the use of revolutionary materials, including additively manufactured (aka 3D-printed) parts such as fuel nozzle tips, turbine shrouds made of ceramic matrix composites (CMCs), and 3D-woven carbon-fiber composites in the fan blades and fan case. These technologies are at the heart of the engine’s impressive stats: As of the end of 2023, the LEAP family had logged more than 40 million flight hours on more than 3,000 aircraft flying with more than 150 operators.