The digital journey continues at Avio Aero’s industrial facilities, thanks to the collaboration efforts by digital teams and manufacturing specialists.
The four new “unmanned and digital” production lines for the CFM LEAP turbine cases at Avio Aero’s Brindisi site are just the first step in the digital journey for Avio Aero’s industrial facilities.
The previous experience with Smart Shop - a tool built on GE’s cloud platform, Predix, which makes real-time diagnostics on every production line or cell possible - has facilitated progress on the concept of the Internet of Things (IoT).
In practice, this tool – developed from the model by Baker Hughes, a GE Company – allows workers to handle the typical complexities of manufacturing diversification.
Smart Shop is currently in a phase of extension and enlargement, which will also make it more flexible and capable of adapting itself to the specific needs of different factories, possessing the possibility of managing differing schedules and working hours but based on a shared logic: interconnection and dialogue between machines.
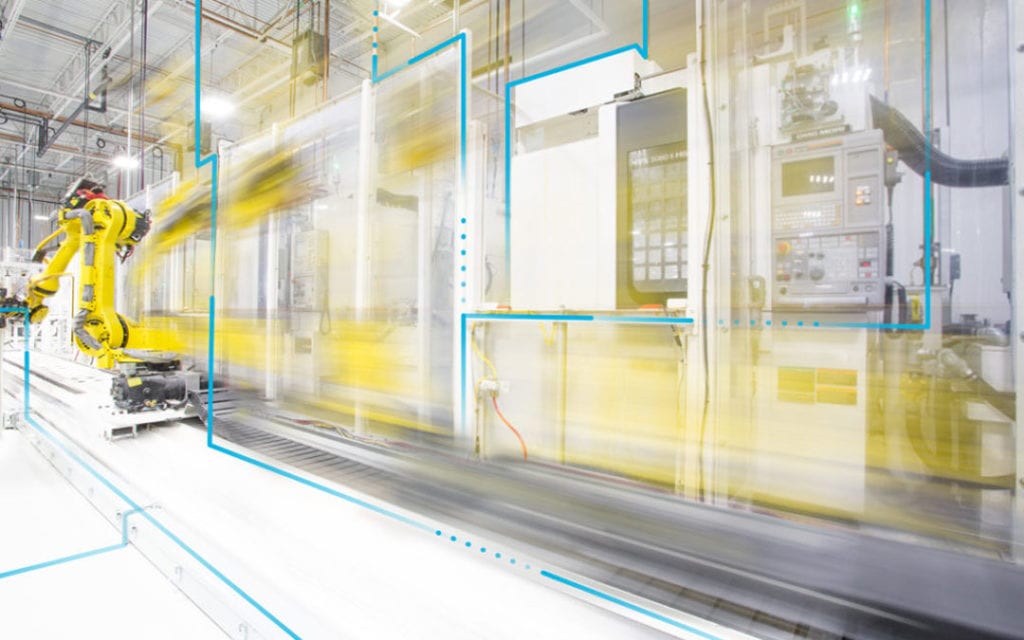
“The principal concept is that any piece of machinery equipped with mathematical control systems can be given the possibility of transmitting certain data to the company network”, explains one of the project managers, Giulio Marino, GE OMLP program engineer.
“What we have done over these last months is create communication channels between machinery and network, so that this data can be reused”, explains Giulio.
Now, both Avio Aero’s Rivalta and Pomigliano d’Arco plants have Smart Shop applications, which currently operate on 25 machinery units. And by mid-2018, machines at the Bielsko Biala plant in Poland will also be connected to the system.
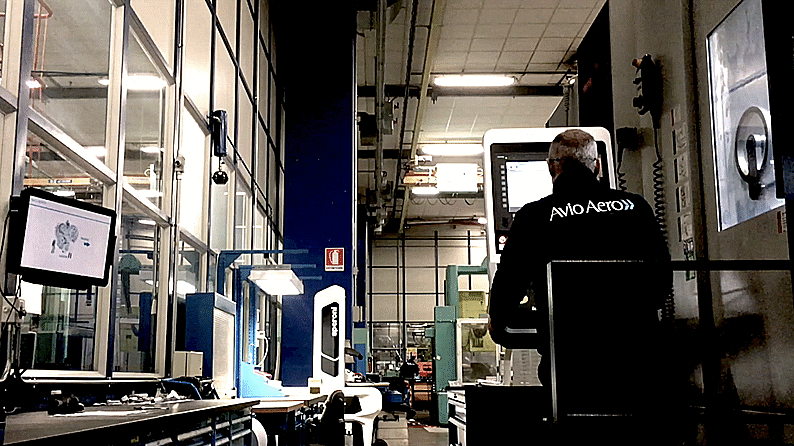
Meanwhile, the more this mission expands the more challenging it becomes. Each time new lines, new machinery or new plants are added, specialists are required to study the different equipment characteristics and architectures to harmonize them and allow them to communicate between each other.
GE Aviation facilities in the US – in Lynn (Massachusetts), Evendale (Ohio) and Asheville (North Carolina) – use a specific IoT communication standard which allows their machinery to have a “dialogue” with one another. As a result, Avio Aero teams are not only studying this language, they are also collaborating with these teams to build a shared technological skeleton for machines that will allow information-sharing between manufacturing lines, while also enabling data gathering and analysis between in-plant machinery with different languages.