Skills Wanted: GE Aerospace Expands Apprenticeships to Grow Talent and Boost Customer Support
January 29, 2025 | by Chris Norris
This January, GE Aerospace’s 300,000-square-foot manufacturing plant in Lafayette, Indiana, is rolling out something newer than but just as crucial as the CFM LEAP* and Passport engines it’s been assembling since it opened a decade ago: its first cohort of apprentice graduates to work on some of the most in-demand jet engines customers need.
The three graduates of Lafayette’s Powerplant Technician Apprentice program, founded in 2022, now have an FAA power-plant license after nearly three years of on-the-job training and classroom work at Purdue University. The Lafayette apprenticeship program, the newest for the company, is one of several to train machinists, mechanics, and other roles in the specialized skills needed to support an engine’s life at every stage.
“For someone who never went to college, this is one of the best decisions I could have made — by far,” says Taylor Riegle, one of the Lafayette apprentice graduates.
Learning the Art of Machining in Rutland
Many engine parts begin life at one of the company’s facilities in Rutland, Vermont, where their Machinist/Toolmaker Apprentice program just celebrated its 50th anniversary. In that time, the program has graduated nearly 350 individuals, transforming some — like Aaron Pratt, the program’s current administrator — from a high school grad to a craftsman working at the very core of the engine-building process.
Rutland is GE Aerospace’s third-largest manufacturing facility. It makes not only the compressor airfoils and other parts for nearly all the company’s commercial and military engines, but also the machines and tools that fabricate these parts. “It’s very hands-on, manual work because of all the gauging and tight tolerances we work with,” explains Pratt, who grew up 20 miles from the Rutland site and is one of the more than 150 former apprentices working there today, including 25% of its leadership team. The program combines semesters of academic work at night with daytime on-the-job training.
“You’re fully immersed in the tool room, learning basic fundamental machining,” says Pratt. “Mill, drill, grind, turning, blueprint reading, using inspection equipment — everything future machinists need to know.” These skills aren’t common, easily learned, or quickly mastered. But, Pratt says, “industries like ours will need them. Precision matters.” After graduating, Rutland apprentices stay local, he adds, “supporting every aspect of our operation.”
Teaching Engine Repair in Scotland
While critical engine parts are made in Rutland and all the parts are assembled in Lafayette, many engines are serviced at a site in Scotland that’s been training its own highly skilled apprentices for decades. Louise Collins is one. Raised outside Glasgow, Collins completed coursework in aeronautical engineering before joining the apprenticeship program at GE Aerospace’s Caledonian site in 2021. In her first two years, Collins spent two days a week studying physics, materials, production management, and other relevant subjects at nearby Ayrshire College; the remainder of the time she worked in a site that took her breath away the first time she set foot in it.
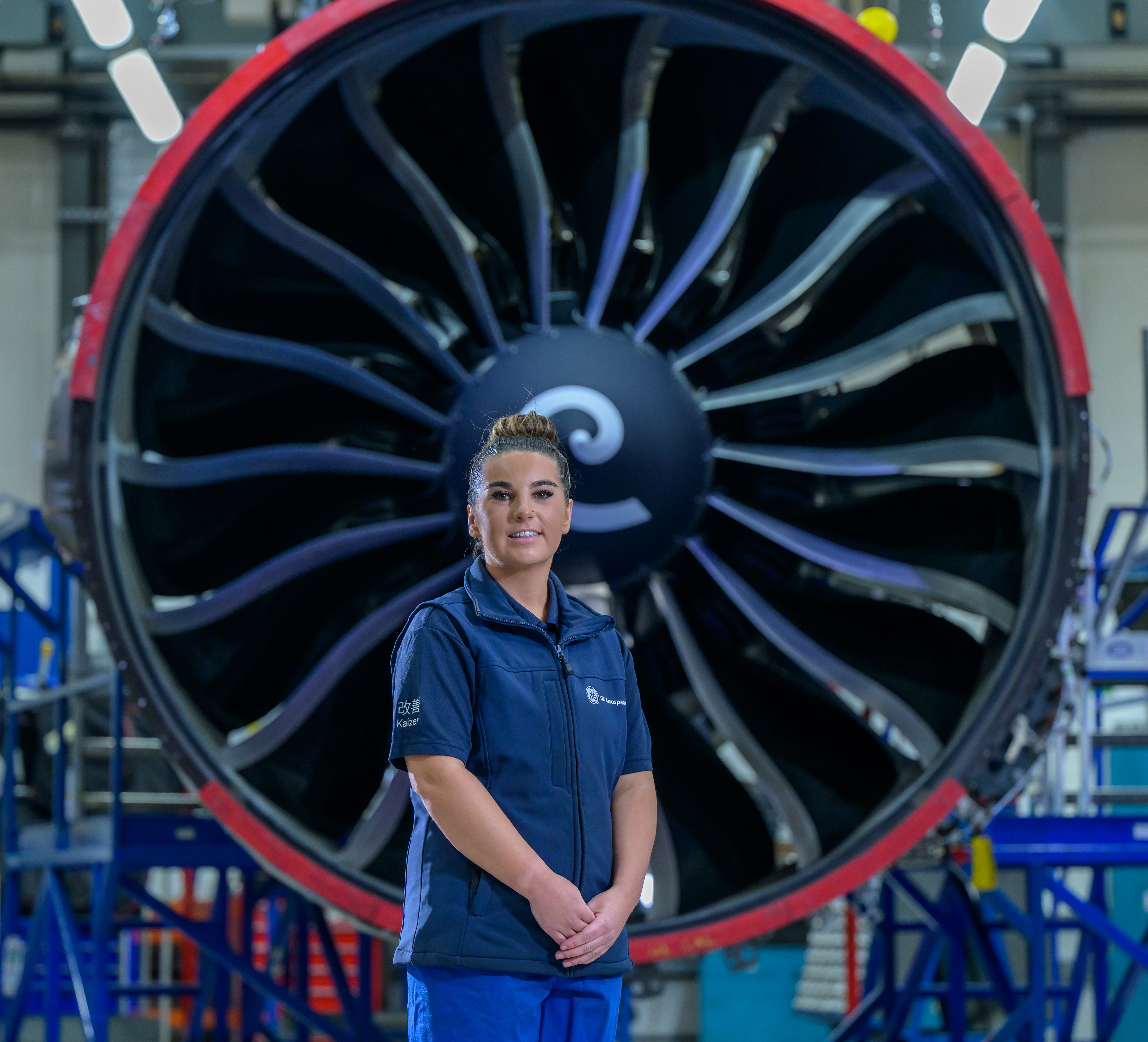
“Seeing the engines on the gantry was just: Wow!” Collins recalls. Before long she was either climbing into turbo cases to work on the GEnx engines that power some of Boeing’s largest jets or helping operate a test cell to replicate on-wing conditions. Once she learns the overall process — disassembly, cleaning, inspection, repair, reassembly, testing — Collins will be able to take apart and rebuild an engine on her own, ensuring that customers’ engines are reliable.
“Because there’s such a process in place of constant work and review, apprentices don’t even realize how many skills they’re acquiring over this time,” says Aidan McIntyre, leader of Caledonian’s apprenticeship program, which has trained more than 350 apprentices. Indeed, McIntyre fondly recalls seeing Collins’ own evolution from nervous apprentice to self-assured technician. “Louise’s confidence has just skyrocketed,” McIntyre says.
One of 14 apprentices in the 2021 cohort, Collins was honored as the company’s Apprentice of the Year last October, and was later short-listed as one of three finalists (out of 40,000 trainees nationwide) in Scotland’s multi-industry “Apprentice of the Year” awards.
Developing Careers: Growing Talent Locally and Organically
GE Aerospace’s Caledonian site, like Rutland and Lafayette, nurtures local talent. “We know that with three years of training, we’ll have 15 fully qualified, fully trained employees with the skill sets to meet the demands of our customers,” says McIntyre.
This August, as new crops of apprentices are set to begin at GE Aerospace facilities around the world, Collins will graduate as a fully qualified aircraft engine mechanic.
“You never know what problems you’re going to face when an engine comes in and something could be wrong with it,” she says. “I like the problem-solving aspect. Just being able to tackle whatever they put in front of you.”
While GE Aerospace has expanded its own apprenticeship and other certification training programs, it is also working to strengthen the workforce across the manufacturing industry. Last fall, the GE Aerospace Foundation and the company donated more than $2.3 million to organizations in the U.S. and internationally that train workers for highly skilled manufacturing jobs around the world.
*CFM LEAP engines are made by CFM International, a 50-50 joint company between GE Aerospace and Safran Aircraft Engines.