Shhhhhh … Can You Hear It Yet? The X-59 Is One Step Closer to Takeoff
February 28, 2024 | by Jay Stowe
As the deputy propulsion lead for NASA’s X-59 supersonic jet, a one-of-a-kind experimental aircraft that will fly faster than Mach 1 and higher than most high-performance airplanes, Paul Dees has no end of tasks to keep him busy. On a macro level, he oversees the integration, testing, and operations of the jet’s F414-GE-100 engine. Day to day, that means working with a team of three engineers at NASA’s Armstrong Flight Center in Edwards, California, four engineers at NASA’s Glenn Research Center in Cleveland, Ohio, their counterparts at the Lockheed Martin Skunk Works facility in nearby Palmdale, and a support team from GE Aerospace in Lynn, Massachusetts. It’s a mixture of hands-on work — installing, testing, and preparing systems for eventual flight — and big-picture planning for the future. “Some of being a deputy is looking at the forest, if you will, instead of the trees,” he says.
But in early January, when NASA and Lockheed at last revealed the X-59 for the first time with a “rollout” ceremony at the Skunk Works, Dees was happy to see that one particular “tree” his team had been working hard on for months was finally in place. “This may sound silly, but as far as challenges we’ve had, specifically with engine integration, probably the biggest one is just making it fit,” he says.
The Quesst mission began in 2014 as a design study for commercial supersonic technology research within NASA’s aeronautics program. The plane’s distinctive shape — approximately 100 feet from tip to tail, with a needle-shaped, 38-foot nose and a nearly 30-foot swept wingspan reminiscent of the Concorde — has been devised for a specific purpose: to reduce the noise that supersonic aircraft create when they break the sound barrier. When it comes to the plane’s design, “everything goes back to shaping the sonic boom,” says Dees. “The key to the X-59 is, can we make a quiet sonic thump?”
To achieve that, the X-59 has an even more distinctive design element: a “top-aft mounted” engine. The F414-GE-100 inlet sits on top of the aircraft at the base of the tail, a rarity in terms of high-performance aircraft design. As Dees explains, at speeds greater than Mach 1 (767 miles per hour), one of the biggest sources of a sonic boom is the inlet of a supersonic engine. “The inlet shock is a very, very strong shock. It creates a lot of pressure differential, which is really just what the ear hears, a change in pressure,” he says. To significantly decrease that effect, “we put the inlet on top, so that the shock would go up instead of down towards the ground.”
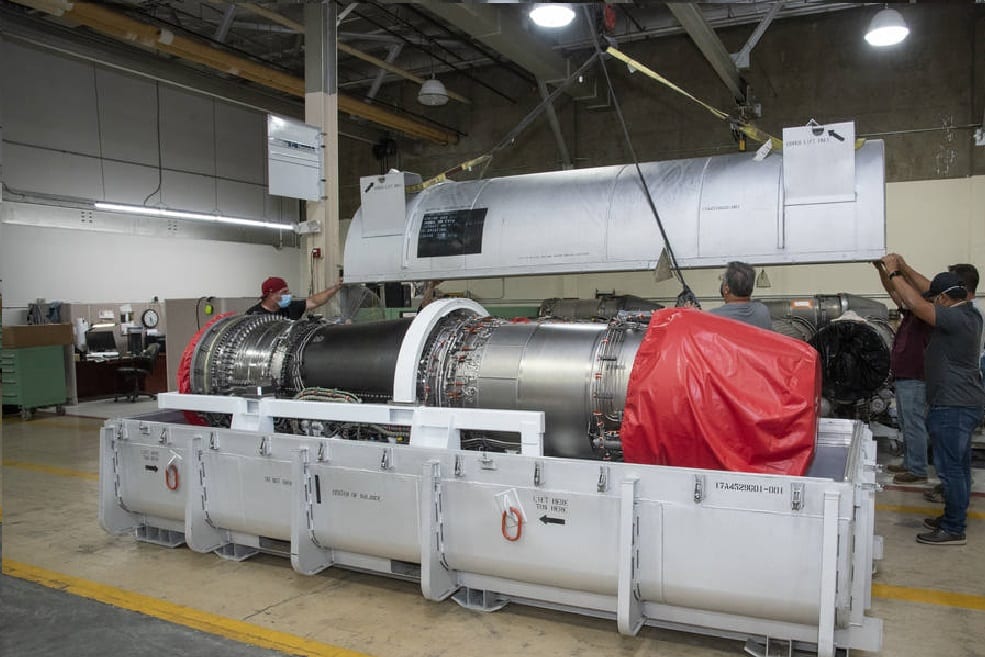
When it came to the actual installation of the engine, Dees and his team were sweating a little. “To get the shape, the outer mold line, that the aircraft needed, we had to build a very, very tight engine bay,” he says. “We knew it was going to be close.”
Ultimately, it took them only four hours to lift the engine and set it into place. “We had four to five people on both sides of the engine and people [crawling] in the inlet and out the back,” he says. “It was a fun process.”
While previous X-planes have originated in military programs, the X-59 has been designed and built using existing systems, such as F-16 landing gear, an aft cockpit from the T-38 Talon training jet, and a new variant of the F414 fighter-jet engine, which powers the U.S. Navy’s F-18 Super Hornet. (Dees acknowledges that they sometimes call it a “Frankenplane.”)
NASA contracted GE Aerospace to develop a unique engine to meet the X-59’s exacting performance and reliability needs. Anthony Hazlett, GE Aerospace’s X-59 demo model engineer based in Lynn, led the group that designed the engine. “We had developed a single-engine version of the F414 for Sweden’s Saab JAS 39E Gripen fighter that we determined would work for the X-59 with some modifications, so we derived a new engine model, the F414-GE-100,” he says. The new engine, which was built and initially tested at the company’s facility in Lynn, is nearly 13 feet long and 3 feet in diameter, and can produce 22,000 pounds of thrust, which will enable the X-59 to accelerate and climb to a cruising altitude of 55,000 feet.
Why so high? That’s the altitude at which the X-59 will test its theory and turn that sonic boom into a quiet “thump.” Dees emphasizes that it’s not just the engine placement; the whole plane has been designed to mitigate the shock. “The way to make weaker shocks is to have a more gentle change in aircraft cross-sectional area,” he says. The X-59’s long, thin nose gradually gets larger from fore to aft to create lots of weak shocks; as a result, the cockpit is situated 38 feet back from the tip. “That’s how long the nose is to get to a place where there’s enough space to put a human,” he adds.
One other thing about that cockpit: It doesn’t have a forward-facing windscreen. Instead, NASA has developed an “eXternal Vision System,” or XVS, which relies on two external cameras (one out front on top and the other underneath the plane) to feed high-resolution data into a display that allows the pilot to see forward. The image, says Dees, is “very, very crisp.”
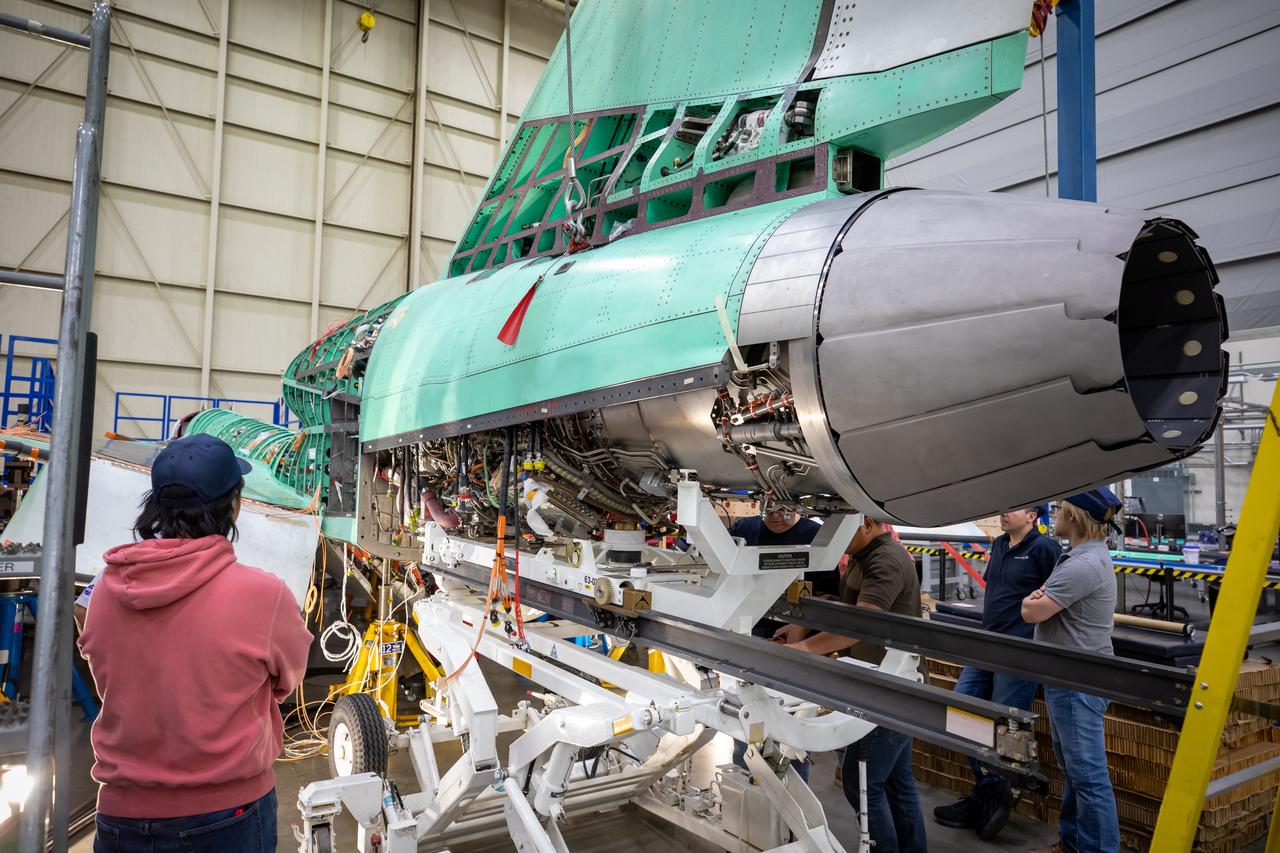
Next up: more testing. Dees and his team are currently running through system checkouts to make sure the engine and the plane are fully integrated. Once those are completed, they will conduct a structural coupling test, ground tests, a taxi test (sending the plane down the runway), and, finally, flight tests, which will take place over nine months.
Dees says there are three phases to the flight tests: first to make sure the plane operates safely; second to confirm a reduced sonic thump; and third to get the X-59 out into national airspace and measure the public reactions to the noise it creates. The data NASA collects will go to the Federal Aviation Administration and the International Civil Aviation Organization with the aim of adjusting rules for noise levels, which could help open a new commercial market for supersonic flight over land. (Currently there is a ban on supersonic travel over land in the U.S.) Dees describes it as “changing from a speed limit to a sound limit.” The end goal isn’t just getting the plane to fly, he says. It’s getting the test data into the hands of the regulators “to help affect a change in aviation for the rest of time.”
“This is a unique program overall and certainly a new platform for the F414,” said Dave Prescott, senior services program manager for the F414 at GE Aerospace. “We’re leveraging the proven performance of the engine and allowing it to showcase its versatility.”