The Shape of Things to Come: Open Fan Technology Championed at Airbus Summit 2025
April 03, 2025 | by Caroline Morris
Last week, Airbus hosted its third Summit in Toulouse, France, to share its latest progress for the future of flight through innovative design, advanced technologies, and novel engineering.
Key to this vision is the development of Open Fan engine architecture, which could help power a next-generation single aisle aircraft that might also incorporate foldable wings and hybrid electric batteries. During the Summit’s “Pioneering Technology for Future Aircraft” session, Mohamed Ali, senior vice president and chief technology and operations officer at GE Aerospace, joined Frank Haselbach, senior vice president of propulsion engineering at Airbus, to discuss how Open Fan technology could lead to a step change in fuel efficiency and durability in commercial aviation.
Ali pointed out that over the past 70 years, huge strides have been made in the efficiency of commercial jet engines. “If you reflect on it, our current newest engine at CFM, the CFM LEAP, is 15% better in fuel burn than its iconic predecessor, the CFM56 engine. And then the CFM56 on its own has been 15% to 20% better than its predecessor,” he said.
Yet for all of the improvements in engine design that have led to these reductions in fuel burn, the shape of the commercial jet engine has changed little. As Haselbach noted, the industry is at something of a crossroads. It can do something evolutionary by developing more ultra-high-bypass-ratio ducted engines. “Or we can actually look at something which is much more rewarding, much more challenging, much more revolutionary,” he said. “Which is Open Fan.”
What Is Open Fan?
Open Fan is a style of engine architecture that aims to provide the same level of safety, speed, noise, and power as current jet engines while delivering a significant reduction in fuel usage and carbon emissions. How will it do this? By shedding the “ducts” that traditionally encase the engine.
CFM International, a 50-50 joint company between GE Aerospace and Safran Aircraft Engines, is developing Open Fan (aka unducted) engine architecture as part of the Revolutionary Innovation for Sustainable Engines (RISE) technology development and demonstration program. Unveiled in 2021, the RISE program is advancing technologies to support a future aircraft engine that aims to be 20% more fuel-efficient than current commercial engines while meeting customer expectations for durability and reliability.
The engineering teams working on Open Fan across CFM have high hopes for the step change this new architecture will bring for fuel efficiency while also being designed to work with alternative fuels like sustainable aviation fuel (SAF) and hybrid electric systems, two other key initiatives currently being pursued by both companies to support the industry’s efforts to reduce flight emissions.
How Can Open Fan Change the Future of Flight?
“The next change, the next improvement in fuel burn to make it in that neighborhood of 20%, cannot happen without a fundamental change in the shape of the engine. And that’s just the laws of physics,” Ali said.
This is because of the “bypass ratio.” To improve fuel burn and efficiency, the approach has typically been to make the engine’s fan bigger. That fan scoops air and throws it to the back of the engine to generate greater thrust. But in that process, a portion of that air ends up burning with the fuel. Ideally, the amount of air that “bypasses” being burned with the fuel should be as high as possible to provide the thrust — the bypass ratio.
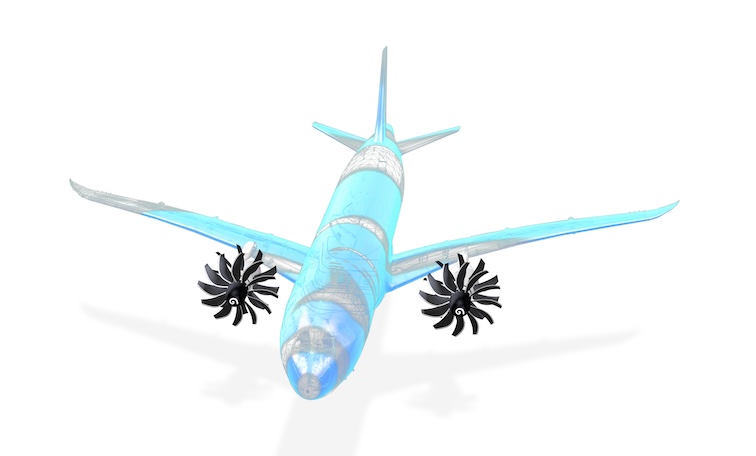
Seventy years ago, the bypass ratio for jet engines was about 2 to 1. Today it’s about 11 to 1. But as Ali noted, engineers can’t keep following the same formula to improve that ratio because of the ducts, which get bigger to support bigger fans, producing drag that eats at the fuel burn benefits. “There is a point that is not very far away from where we are today in which that duct is so big that it wipes out any gains that are coming from making the fan bigger,” he said.
This is where the Open Fan comes in. GE Aerospace’s current design aims to take the bypass ratio from 11 to 1 to 60 to 1. “That’s six-zero from where we are today,” Ali added. “That is the fuel burn opportunity that we are thrilled and excited about.”
Testing, Testing: Putting Open Fan Through the Paces
The RISE program has completed more than 250 critical field tests so far. Ali pointed to two wind tunnel tests in particular that simulated the integration of the Open Fan and the wing. The first 300-plus hours of tests were completed by Safran Aircraft Engines at a facility run by ONERA, the French national aerospace research center, in “the largest wind tunnel in the world,” using a one-fifth scale model of the Open Fan performing at cruising speed. This was followed by a second set of tests in collaboration with DNW in the Netherlands, performed at low speed to simulate an aircraft during takeoff, climb, and descent.
Ali called the results “extremely encouraging,” not only in terms of validating performance and noise but also the computational analysis that GE Aerospace has done with the help of Frontier, one of the world’s fastest supercomputers, maintained at the U.S. Department of Energy’s Oak Ridge National Laboratory. Last November, the company announced a new project it’s working on with Boeing, NASA, and Oak Ridge to use supercomputing to study the aerodynamics of an Open Fan architecture mounted on an aircraft wing in simulated flight conditions.
“Typically, when you get computational results and compare them to the wind tunnel [tests], there is a difference between the two. You spend a lot of time reconciling,” he said. But in this case, there was “no reconciliation.” He added: “These supercomputers’ capabilities are unprecedented in the ability to simulate the future.”
Next Steps for Open Fan
“We are in the middle of a lot of testing to validate durability, vibrations, endurance, and ingestion,” Ali explained. “And we’re doing all of these tests not just for the Open Fan, but there are lots of other technologies that are part of the RISE program that are behind the fan, whether it’s a more advanced core or hybrid electric.”
In fact, a lightweight compact core, which houses the engine’s compression, combustion, and high-pressure turbine modules, is being reengineered by the RISE program team to be smaller and optimize thermal efficiency, with an advanced cooling system and materials that can withstand extremely high temperatures. The core is being tested for compatibility with next-generation fuels, including unblended SAF and hydrogen, as well as with hybrid electric systems like the ones GE Aerospace is currently developing with NASA.
Flying Forward Together
The challenge of more efficient flight is not solved by one invention or company. It is about industry-wide innovation and collaboration.
“This is all leading up to the demonstration flight that we are going to be doing jointly with Airbus later in this decade,” said Ali. Acknowledging “the strong partnership” between CFM and Airbus, he added: “It’s really a reflection of what the technology wants us to do, which is a deeper, better integration between the engine and the aircraft.”
Watch the video of Mohamed Ali’s Open Fan discussion at Airbus Summit 2025 here.