Rebirth of a Classic: The F110 Engine Celebrates 40 Years of Continuous Production — and a Renaissance
December 03, 2024 | by Dianna Delling
In 1978, just one manufacturer was supplying engines for the U.S. military’s F-14, F-15, and new F-16 fighter jets — and it wasn’t GE Aerospace. But what became known as the “Great Engine War” of the 1980s changed that, launching GE Aerospace’s F110 engine, which continues to power new fighter jets around the world.
Using the GE F101 engine, originally built for the B-1 bomber, as a foundation, GE Aerospace engineers set out to develop a competitive power plant. By 1984 they had succeeded. That year, the U.S. Department of Defense awarded GE Aerospace a contract to power future fighter jets with its new F110 low-bypass afterburning turbofan.
“The Great Engine War showed that competition is the clear way to go to optimize outcomes for the warfighter and U.S. taxpayers,” says Sean Keith, executive product director for the F110, F101, and F118 engine programs at GE Aerospace. “The result of the competition was better engine performance at lower cost, with improved engine safety, maintainability, and durability.”
It also fueled development of one of the most enduring engines in military history. With more than 11 million flight hours under its wing and the most thrust in its class, the F110 now powers F-15s and F-16s for the U.S. military, along with jets in 16 allied nations, and has been selected to power some of the newest advanced combat aircraft in the world. As the F110 celebrates 40 years of continuous production and improvement, the iconic engine isn’t just maintaining position; it’s enjoying a major resurgence.
Not Your Father’s F110: GE Aerospace History
“We have been in continuous year-over-year production since 1984, and we are ramping production to meet strong market demand,” Keith says. In a somewhat unexpected turn, he explains, production levels for the F110 are expected to hit yearly levels not seen since 2009.
That’s partly due to orders for new highly advanced aircraft that are powered exclusively by the F110-129 engine — including Boeing F-15EX Eagle IIs purchased by the U.S. Air Force and other allied partners, and Türkiye’s fifth-generation combat fighter, the TAI Kaan. It’s also because more militaries are turning to proven, cost-effective planes like the F-15 and F-16 to complement fifth-generation fighters like the F-35. The F110 engine has won nearly all the F-15 and F-16 orders placed in the past eight years. (Military jets, like computers, are categorized by generation according to the ever-evolving technological advances they employ. Fifth-generation aircraft, the latest generation flying today, use technology developed in the 21st century for even more stealth and maneuverability than what’s found in fourth-generation planes like the F-15 and F-16.)
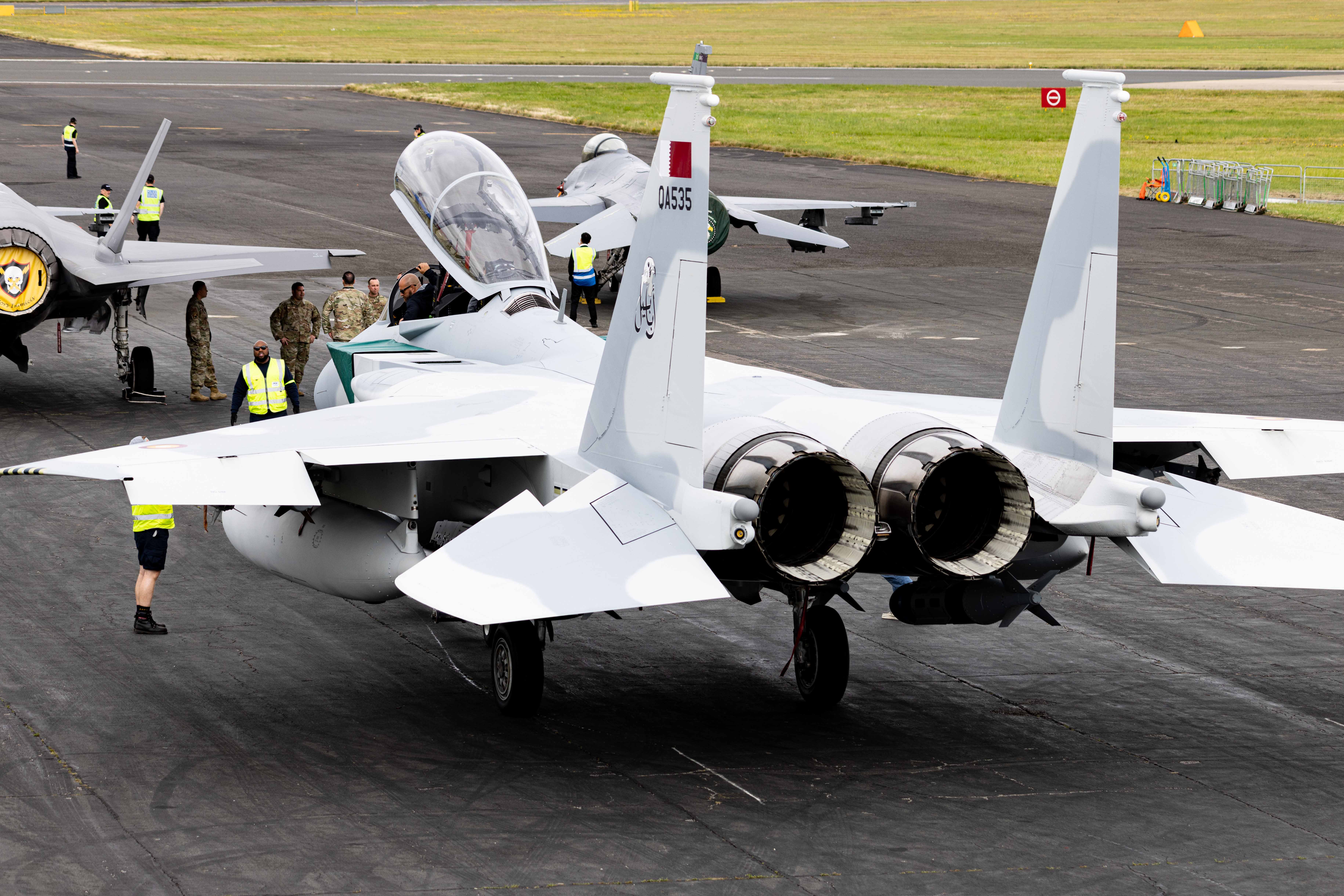
“To potentially still be hitting record engine volumes is both a testament to the great technology and the history of the platform, but also to the global environment and the rebirth of the fourth-generation market,” Shawn Warren, vice president and general manager of combat and trainer engines at GE Aerospace, recently told Aviation Week.
Of course, the F110 has been updated significantly since it first hit the market. “We like to say it’s not your father’s F110,” says Keith. “A full 92% of the parts have undergone some type of design change — whether it’s a new material, a new coating, or an improved manufacturing or inspection process.”
The F110-129 and F110-132 engine variants have been updated with Service Life Extension Program (SLEP) hardware upgrades, including many based on technologies developed in GE Aerospace’s commercial engine programs. Advanced cooling technologies adapted from CFM International’s LEAP* engines, for example, now provide superior performance in extreme conditions — what operators refer to as “hot and harsh environments.” Engine availability, or readiness, and reduced life-cycle costs have also been bolstered through updates that have increased the lifespan of major rotating parts.
Engine upgrades have not only enhanced performance but helped the F110 achieve an industry-leading standard for time on wing — the average hours flown before an engine is removed from an aircraft for maintenance — of 750 hours.
“The number one reason that our engine comes off wing is scheduled maintenance,” Keith says. “That’s exactly what you want.” Keith added that the engine is designed so that 90% of all maintenance can be performed on-wing and at an on-site facility as opposed to a central depot. “It’s all about readiness. As one of our Air Force customers likes to say, ‘Time on wing wins wars.’”
Back to the Future: Military Aviation
With a combat-proven track record few military engines can match, the F110 has already earned its place in military aviation history. Yet GE Aerospace engineers continue to work on expanding its capabilities.
A modified version of the engine is currently being tested at GE Aerospace’s Evendale facility. The engine is undergoing a 6,000-cycle accelerated mission test to validate additional capability and durability improvements, and results are expected in 2025.
“With these advanced engines, the F110 likely has another 40 to 50 years of runway, which is just a remarkable statement to think about,” says Keith. “It has even more latent capability that could be tapped into if needed, including thrust, range, and horsepower extraction.”
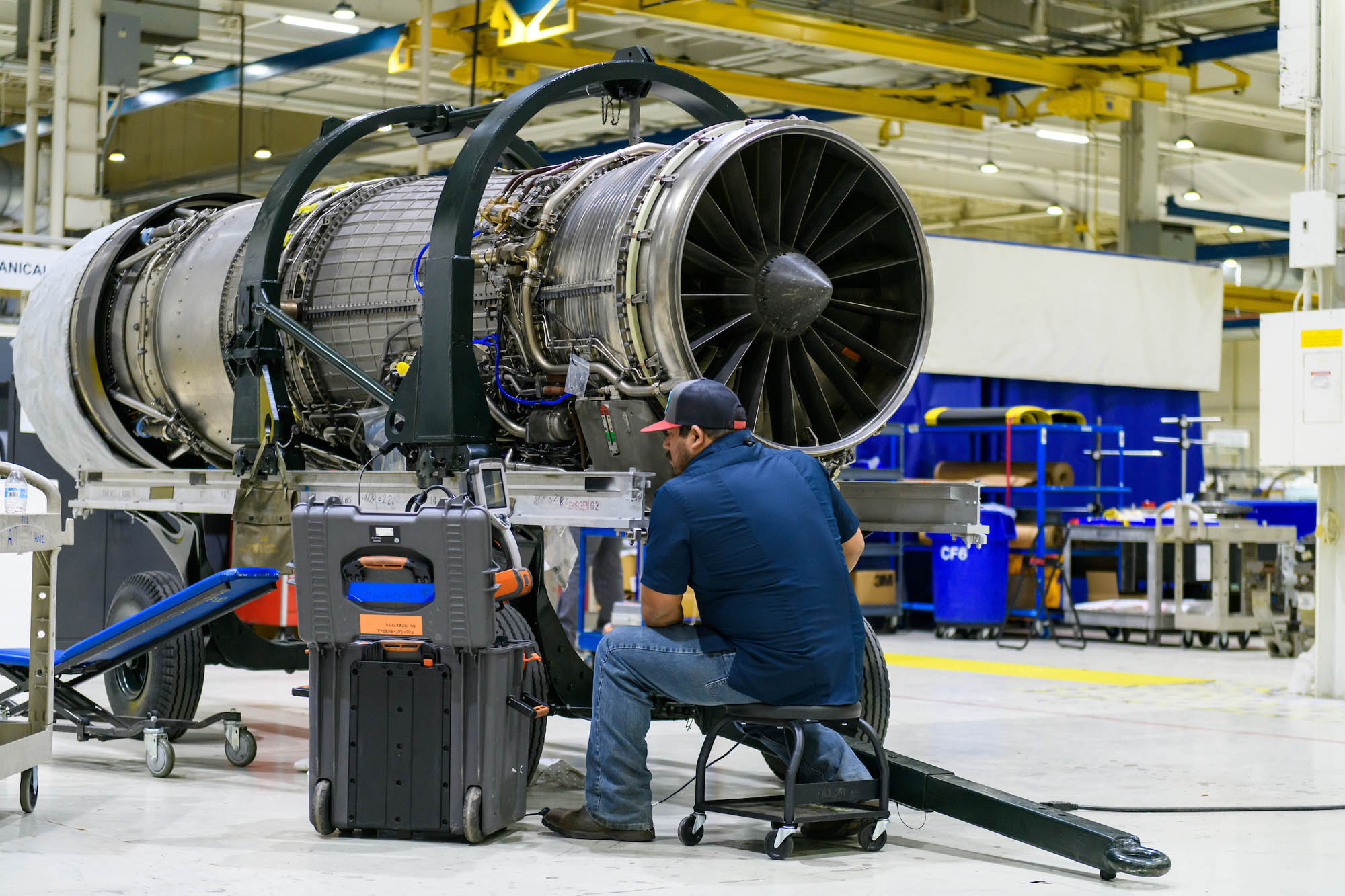
It’s also a source of pride for Keith, who started his career at GE Aerospace as a turbine blade designer in the F110 program in 1990. He worked on the engine for the first seven years of his career, leading the redesign of a low-pressure turbine blade that’s still an integral component of the engine. Returning to the F110 team in 2020, when he took on his current position, has given him a unique perspective on the engine’s evolution.
“It’s been fun for me to be back where I started and to see how strong the engine is performing in the field and in its segment, with such a bright future,” he says. “Engine safety, performance, and reliability — these are the things that really have stood the test of time and made the F110 the engine of choice for our customers. Seeing this renaissance, this renewed interest in the F110, is extremely rewarding, to say the least.”
* LEAP engines are produced by CFM International, a 50-50 joint company between GE Aerospace and Safran Aircraft Engines.