Avio Aero’s facilities in Europe are ready for the unprecedented commitment in order to support CFM engines for next generation medium-range aircraft.
Everything is almost ready for entry into service of all versions of the LEAP engine: the brand-new engine based on state-of-the-art technologies and materials (including the 3-D printed fuel nozzles and the carbon fiber fan blade and case, the twin-annular, pre-swirl combustor, and the titanium aluminide (TiAl) low-pressure turbine blades).
The LEAP-1A is already in commercial service powering the Airbus A320neo family: the maiden flight from Istanbul to Antalya, with the Turkish owned Pegasus Airlines took place last August.
The LEAP-1C (the twin of the -1A, designed for the Chinese airliner COMAC C919) obtained EASA and FAA certification last December and will be ready to take off very soon.
The LEAP-1B, which powers the new Boeing 737 Max, also passed the certification tests last year with flying colors and is ready for entry into service.
The LEAP engine is a product of CFM International, a 50/50 joint company between GE and Safran Aircraft Engines. Nearly twelve thousand orders are in the books with more than 100 airlines around the world, and the volumes to be produced are considerable: over 500 engines in 2017, which will become 1,100 in 2018 and as many as 2,000 by 2020.
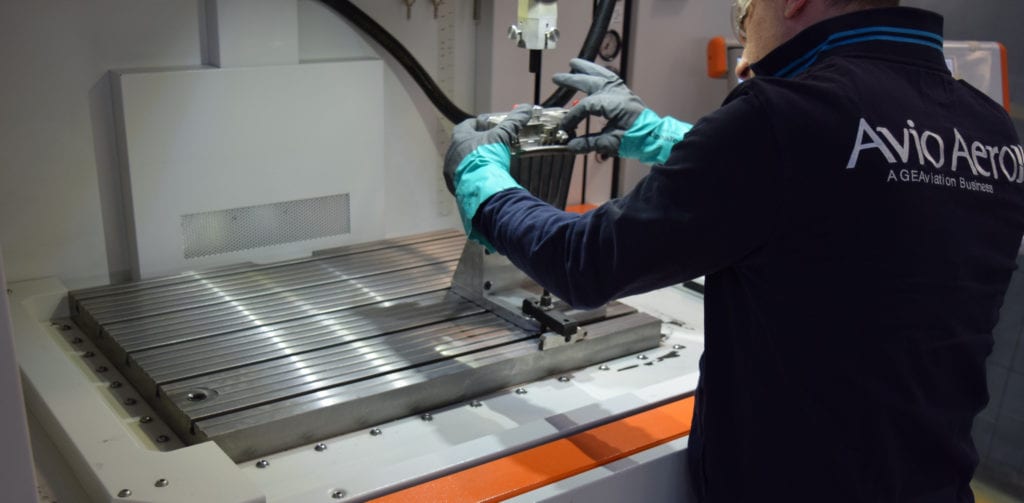
Avio Aero will support the LEAP program at all its facilities in Italy and at its center of excellence in Bielsko Biala (Poland) where it manufactures the nozzles for the low-pressure turbine and the stator stage 3, 4 and 5 turbine blades for all three versions of the engine (LEAP-1A, -1B and -1C).
Avio Aero also designed these components and owns the technological processes used to produce them, notably the EDM (electrode discharge machine) technology: this vastly reduces machine throughput time, significantly increases quality and improves overall cost-effectiveness.
In Italy, the biggest and most highly complex challenge, above and beyond the huge commitment in terms of the production volumes required from each Avio Aero facility - will be faced by the combustors & frames product center in Pomigliano (Naples).
For the first time ever, this center of excellence, which has made combustion systems (and their components) for well-known aircraft engines like the SaM146, CFM56, PW800 and PW308, will manufacture an entire combustor module with the innovative twin-walled (twin-annular) combustor exclusively for the LEAP engine. The internal and external components (inner and outer liners) of the combustor are unusual as the two parts are assembled rather than cast to form a single cylindrical component.
Even the combustion chamber walls are innovative: they present for the very first time the “shaped cooling holes" of a very special, unconventional form.
The combustor module is composed of about 27 assembled parts, nearly 10 of which are entirely made at the factory near Naples. Emanuela Genua, the manufacturing engineer at the Product Centre, told us: "The inner and outer liners, and the dome through which the flame passes, are certainly the most technologically advanced and complex parts we are working on, and perhaps have ever worked on, using processes such as laser drilling and plasma treatment, with six brand new processes introduced to the workshop by our skilled operators." In addition to the combustor module, this product center manufactures the seal between the combustor module and the turbine module.
Giovanni Ferrara, leader of the combustors & structures center of excellence, remarked: "We are going to deliver the first combustor for the LEAP-1A, the version that we'll focus on all year, and will start work on the -1B by the end of 2017. We are working tirelessly to meet this challenge and are savouring the opportunity: investing in new machines and dedicated production cells, using advanced models of lean manufacturing, dividing exceptional volumes of work between all the teams, and qualifying each new technological process developed by our engineers."
The contribution of the factories in southern Italy to the LEAP engine program is truly impressive. Significant technology investments, more than 250 engineers, technicians and operators: Avio Aero is set to take on the challenge.