A Look at GE’s F110 Engine with Former Fighter Pilot Lt. Gen. (retired) Sam Angelella
June 19, 2020 | by Cole Massie
U.S. Air Force fighter pilot Lt. Gen. (retired) Sam Angelella had one question at the end of his F110 engine transition course: “What are the throttle restrictions?”
“What do you mean?” The instructor replied.
“You know, the throttle restrictions,” Angelella clarified, based on his experience as a pilot. “High and slow, corners of the envelope…”
The instructor cut Angelella off before he could get any further: “There are no throttle restrictions.”
Hearing something like “no throttle restrictions” is certain to capture a fighter pilot’s full attention. And for Angelella, it was his introduction to the power and capability offered by GE’s F110 engine, the engine that powered many of his flights in the F-16C/D.
“I flew F110-powered F-16s on combat missions in Operation Desert Storm with a full complement of air-to-air and air-to-ground munitions, two full external fuel tanks, and a 600-pound ECM pod,” Angelella said. “Never once had to worry about power, never once had to worry about the throttle, and never once had to worry about the engine.”
https://www.youtube.com/watch?v=pdiCfriRC9U&feature=youtu.be
Nearly 30 years after his first experience with the F110, Angelella now touts its capabilities, among other GE military products and services, leading GE Aviation’s military customer programs team from Washington, D.C. Roughly 2,800 hours flying GE-powered military aircraft makes him a uniquely qualified person to work with military customers and bring the next generation of power to the Warfighter.
One of the most exciting opportunities Angelella sees coming up is the U.S. Air Force’s planned acquisition of the Boeing F-15 Advanced Eagle, the most advanced F-15 to date. The F110-GE-129 is currently the only engine certified for the F-15 Advanced Eagle, and it brings along a stellar track record.
Backed by a continuous infusion of new technology, the F110 family of engines surpassed 10 million flight hours in 2019, with the -129 demonstrating 6,000 total accumulated cycle intervals and averaging more than 750 hours time-on-wing between shop visits.
The F110-GE-129 also has applications on advanced F-15s around the globe, including Saudi Arabia, Singapore, South Korea, and Qatar (beginning in 2021). The F110 production line is currently active and delivering new engines with the help of skilled workers at GE sites across the United States.
“The F110 is a cost-effective, high-performance engine,” Angelella explained. “Its safety and reliability ultimately increase mission capability rates and readiness—absolutely critical aspects of supporting our customers’ mission requirements.”
One such mission requirement that has increasingly come into focus is sustainment. GE Aviation’s vice president and general manager of large combat and mobility engines, Shawn Warren, constantly looks for avenues to more effectively help the Air Force sustain military engines like the F110.
“The first step in sustainment is maximizing engine time-on-wing and eliminating removals,” Warren said. “That’s why we introduced the Service Life Extension Program for the F110, which incorporated commercial technology and upgraded the combustor and high-pressure turbine. It’s brought 25 percent improvement in cost-per-flying hour and tripled time-on-wing. Those are significant benefits to the Warfighter.”
Warren added that if an engine removal is required, the second step in sustainment — spare parts availability — is essential. That’s where GE Aviation’s “Captains of Industry” partnership with the Defense Logistics Agency has played a key role. Since the partnership’s inception five years ago, spare parts availability has increased from 85 percent to 96 percent between GE’s F110, F101, and F118 engines at Tinker Air Force Base in Oklahoma.
Thanks to these improvements, GE F110-powered aircraft like the F-16 and upcoming F-15 Advanced Eagle for the U.S. Air Force remain on aircraft longer and are returned to service faster. It translates to, as Warren pointed out, better Warfighter readiness.
Read more on how GE Aviation is helping the Air Force sustain its fleet.
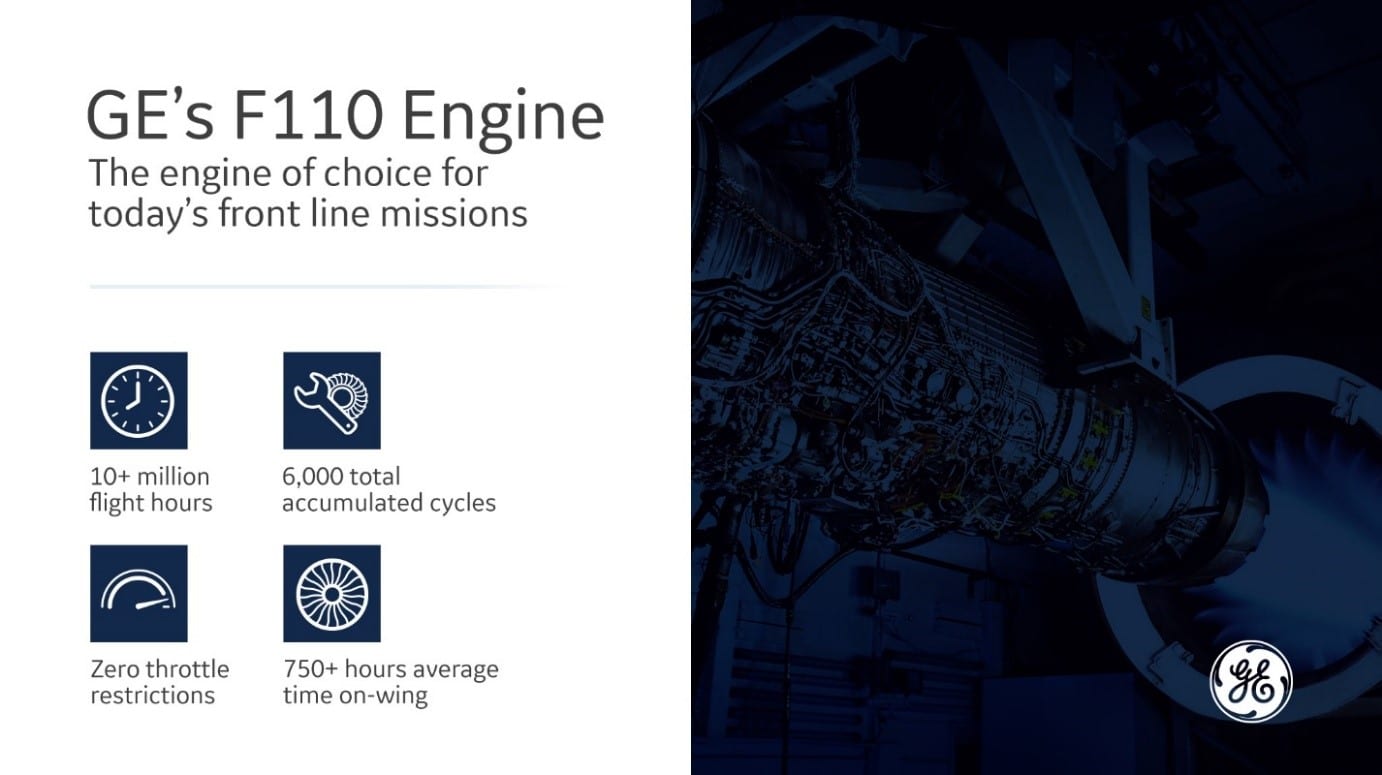
Looking back to his days as a three-star general in the Air Force, Angelella believes the writing was on the wall in regard to joining GE Aviation. He’s an engineer at heart and an avid fan of the technology behind the supersonic fighter jets he once flew.
“When I think back to my flying days, it’s the F110-powered F-16s that get me most excited,” Angelella said. “It’s easy for me to go talk about the product because I have first-hand experience with its performance. So, I really look at it from an operator’s point of view.”
In his discussions with customers, Angelella says he sees excitement from their end too. “They’re looking forward to the next generation of power, whether that’s our newest engines or engines that have been upgraded over their lifetimes, like the F110.”
Products like the T901 turboshaft engine and Adaptive Cycle Engine (ACE) are integral parts of the newest generation, integrating core technologies like additive manufactured parts and ceramic matrix composites (CMCs) from GE’s renewed commercial engine portfolio. And while a product like the F110 has been operating in excess of three decades, the engine is constantly receiving upgrades to extend service life and improve performance characteristics.
“I put my trust in the technology as a pilot, I put my trust in the technology as a commander,” Angelella remarked. “And that’s why I trust GE’s technology today to deliver the power and capability needed for tomorrow’s missions.”
“What do you mean?” The instructor replied.
“You know, the throttle restrictions,” Angelella clarified, based on his experience as a pilot. “High and slow, corners of the envelope…”
The instructor cut Angelella off before he could get any further: “There are no throttle restrictions.”
Hearing something like “no throttle restrictions” is certain to capture a fighter pilot’s full attention. And for Angelella, it was his introduction to the power and capability offered by GE’s F110 engine, the engine that powered many of his flights in the F-16C/D.
“I flew F110-powered F-16s on combat missions in Operation Desert Storm with a full complement of air-to-air and air-to-ground munitions, two full external fuel tanks, and a 600-pound ECM pod,” Angelella said. “Never once had to worry about power, never once had to worry about the throttle, and never once had to worry about the engine.”
https://www.youtube.com/watch?v=pdiCfriRC9U&feature=youtu.be
Nearly 30 years after his first experience with the F110, Angelella now touts its capabilities, among other GE military products and services, leading GE Aviation’s military customer programs team from Washington, D.C. Roughly 2,800 hours flying GE-powered military aircraft makes him a uniquely qualified person to work with military customers and bring the next generation of power to the Warfighter.
One of the most exciting opportunities Angelella sees coming up is the U.S. Air Force’s planned acquisition of the Boeing F-15 Advanced Eagle, the most advanced F-15 to date. The F110-GE-129 is currently the only engine certified for the F-15 Advanced Eagle, and it brings along a stellar track record.
Backed by a continuous infusion of new technology, the F110 family of engines surpassed 10 million flight hours in 2019, with the -129 demonstrating 6,000 total accumulated cycle intervals and averaging more than 750 hours time-on-wing between shop visits.
The F110-GE-129 also has applications on advanced F-15s around the globe, including Saudi Arabia, Singapore, South Korea, and Qatar (beginning in 2021). The F110 production line is currently active and delivering new engines with the help of skilled workers at GE sites across the United States.
Above: The first GE-powered F-16s went into service in 1987. (Photo credit: U.S. Air Force) Top: A Royal Saudi Air Force F-15SA, powered by GE’s F110 engine. (Photo credit: David Lilienthal)
“The F110 is a cost-effective, high-performance engine,” Angelella explained. “Its safety and reliability ultimately increase mission capability rates and readiness—absolutely critical aspects of supporting our customers’ mission requirements.”
One such mission requirement that has increasingly come into focus is sustainment. GE Aviation’s vice president and general manager of large combat and mobility engines, Shawn Warren, constantly looks for avenues to more effectively help the Air Force sustain military engines like the F110.
“The first step in sustainment is maximizing engine time-on-wing and eliminating removals,” Warren said. “That’s why we introduced the Service Life Extension Program for the F110, which incorporated commercial technology and upgraded the combustor and high-pressure turbine. It’s brought 25 percent improvement in cost-per-flying hour and tripled time-on-wing. Those are significant benefits to the Warfighter.”
Warren added that if an engine removal is required, the second step in sustainment — spare parts availability — is essential. That’s where GE Aviation’s “Captains of Industry” partnership with the Defense Logistics Agency has played a key role. Since the partnership’s inception five years ago, spare parts availability has increased from 85 percent to 96 percent between GE’s F110, F101, and F118 engines at Tinker Air Force Base in Oklahoma.
Thanks to these improvements, GE F110-powered aircraft like the F-16 and upcoming F-15 Advanced Eagle for the U.S. Air Force remain on aircraft longer and are returned to service faster. It translates to, as Warren pointed out, better Warfighter readiness.
Read more on how GE Aviation is helping the Air Force sustain its fleet.
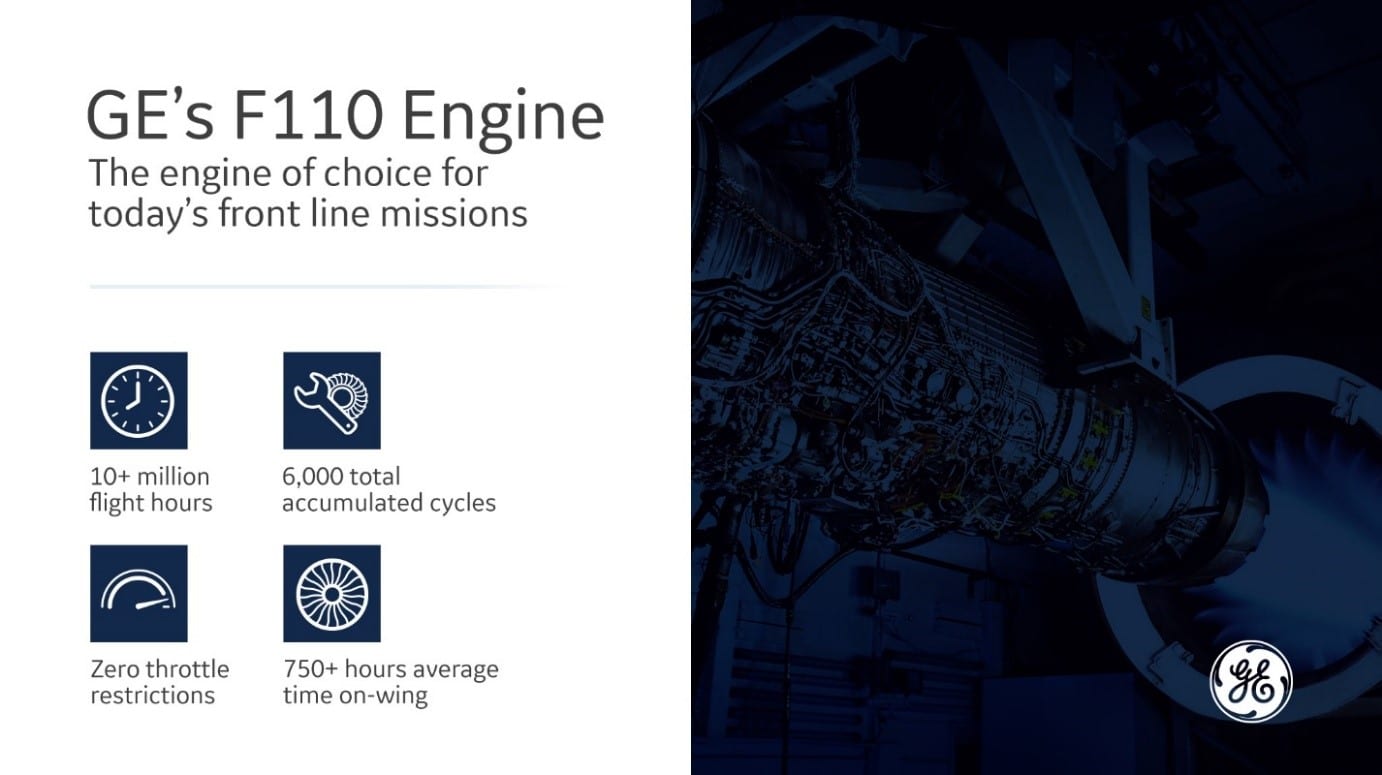
Looking back to his days as a three-star general in the Air Force, Angelella believes the writing was on the wall in regard to joining GE Aviation. He’s an engineer at heart and an avid fan of the technology behind the supersonic fighter jets he once flew.
“When I think back to my flying days, it’s the F110-powered F-16s that get me most excited,” Angelella said. “It’s easy for me to go talk about the product because I have first-hand experience with its performance. So, I really look at it from an operator’s point of view.”
In his discussions with customers, Angelella says he sees excitement from their end too. “They’re looking forward to the next generation of power, whether that’s our newest engines or engines that have been upgraded over their lifetimes, like the F110.”
The F-15SG is powered by the F110-GE-129 for the Republic of Singapore Air Force. (Photo credit: Boeing)
Products like the T901 turboshaft engine and Adaptive Cycle Engine (ACE) are integral parts of the newest generation, integrating core technologies like additive manufactured parts and ceramic matrix composites (CMCs) from GE’s renewed commercial engine portfolio. And while a product like the F110 has been operating in excess of three decades, the engine is constantly receiving upgrades to extend service life and improve performance characteristics.
“I put my trust in the technology as a pilot, I put my trust in the technology as a commander,” Angelella remarked. “And that’s why I trust GE’s technology today to deliver the power and capability needed for tomorrow’s missions.”
Lt. Gen. (retired) Angelella and his wife in front of his F110-powered F-16 following his final F-16 flight on May 13, 2015. (Photo credit: Sam Angelella)