Subtracting with additive: A deep dive into the development of GE's next-gen turboprop
July 26, 2017
General Electric’s new 1,300 SHP-rated Advanced Turboprop (ATP) is the first entry in GE’s new family of turboprop engines aimed at Business and General Aviation aircraft in the 1,000-1,600 SHP range. The ATP engine will power the new Cessna Denali aircraft built by Textron Aviation.
GE Aviation has chosen Europe as the home for this incredible engine to be built. The ATP is in fact an all-European project: its design and product development team is based in Italy, Poland, Czech Republic and Germany.
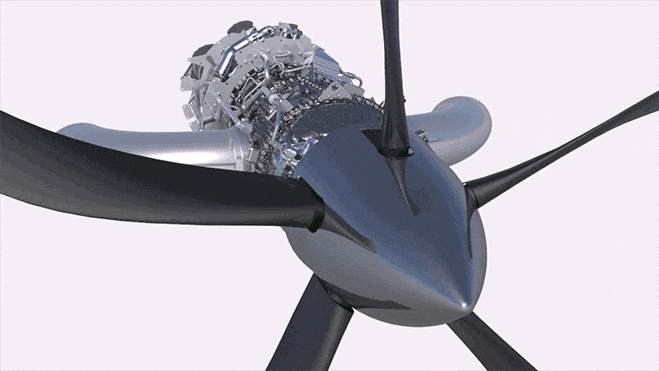
The development activities are coordinated from the operations room in Rivalta, Italy, while the assembly and test of the engine will be carried out in Prague, Czech Republic. It was also recently decided that the additive manufacturing components of the engine will be manufactured in Brindisi, Italy, where dedicated machines will be installed on site in 2018 and the first production activities will begin by 2019.
Some of the ATP’s advantages come from the use of additive manufacturing, which simplifies the engine's design: the engine features fewer parts and solutions not feasible with conventional technologies, resulting in a lighter, more compact engine.
GE Aviation is a pioneer of additive technology and has been working in the additive space for the past decade, developing various components for new generation engines such as the CFM LEAP and GE9X and adopting processes including Electron Beam Melting and Direct Metal Laser Melting.
ATP has gone much further: it is the first turboprop to include 3D-printed parts. Thirteen components, ranging from the combustion chamber to various structural elements, have reduced the total number of parts in the engine by about 30%. “This is not a matter of simply replacing one production method with another, but of reinventing the way aviation engines are conceived and designed” said Giorgio Abrate, Avio Aero engineering leader.
Additionally, the Italian Government is also considering additive manufacturing as one of the most important enabling technologies to address the objectives pursued under the National Industry 4.0 Plan launched at the end of 2017. The Italian Ministry of Economic Development has undertaken actions to support Avio Aero's initiative in Brindisi as part of a broader and more significant contribution to the digital transformation of the manufacturing industry in Italy.
The main Avio Aero responsibilities include engine systems, control systems and software, combustion systems and both the power and accessory gearboxes.
https://www.youtube.com/watch?v=D9-Jjs5D4kM
ATP power gearboxes are the first Avio Aero-produced gearbox featuring an additively manufactured main housing. The use of additive allowed the design engineers to explore new design methods not previously available with traditional manufacturing techniques. “These include the use of new alloys because some of the typical manufacturing trade-off from the past (e.g. weight vs. cost) doesn’t exist with additive. Now, new solutions can be found to benefit both weight and cost efficiencies at the same time,” claims Luca Bedon, senior engineering section manager for aero dynamics at Avio Aero.
The ATP combustor has been designed by the Avio Aero engineers around a “reverse flow” configuration to minimize its length and to improve overall engine weight and installation. In this case, additive has proven to be a real game changer. In addition to the flexibility introduced in the mechanical and thermal design, additive allowed Avio Aero to prototype and test a number of design concepts that conventional manufacturing processes would not allow within the program schedule. With additive manufacturing, Avio Aero’s engineers were able to validate design experimentally, learning from each iteration.
The mechanical design of the 2-stage high pressure turbine (HPT) and the 3-stage power turbine (PT) as well as the high pressure compressor (HPC) are carried out by the Engineering Design Center (EDC) located in Warsaw, Poland. The team is supported by the GE Aviation team in Munich, Germany, who support the overall mechanical design process and, in particular, supported the design of the HPC. The Prague, Czech Republic team is responsible for the assembly, instrumentation, test and certification of the ATP.
The ATP engine earned another record: it will be the first “digital native” aviation engine because it was developed using advanced 3D modeling. Sensors in the engine will gather data and allow users to build a so-called digital twin of the ATP. This virtual model of the engine will factor in on real conditions, helping operators predict the right time for maintenance and increasing efficiencies of the engine and overall aircraft.
GE's new turboprop engine sets the bar high for what can be achieved through additive manufacturing. What will additive transform next?
https://youtu.be/KqcRm-maZrM
GE Aviation has chosen Europe as the home for this incredible engine to be built. The ATP is in fact an all-European project: its design and product development team is based in Italy, Poland, Czech Republic and Germany.
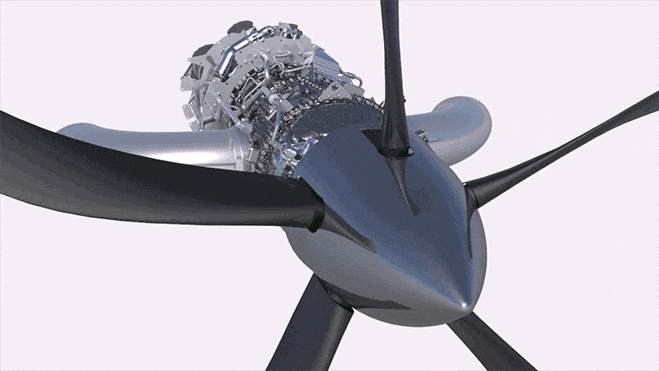
The development activities are coordinated from the operations room in Rivalta, Italy, while the assembly and test of the engine will be carried out in Prague, Czech Republic. It was also recently decided that the additive manufacturing components of the engine will be manufactured in Brindisi, Italy, where dedicated machines will be installed on site in 2018 and the first production activities will begin by 2019.
Some of the ATP’s advantages come from the use of additive manufacturing, which simplifies the engine's design: the engine features fewer parts and solutions not feasible with conventional technologies, resulting in a lighter, more compact engine.
GE Aviation is a pioneer of additive technology and has been working in the additive space for the past decade, developing various components for new generation engines such as the CFM LEAP and GE9X and adopting processes including Electron Beam Melting and Direct Metal Laser Melting.
ATP has gone much further: it is the first turboprop to include 3D-printed parts. Thirteen components, ranging from the combustion chamber to various structural elements, have reduced the total number of parts in the engine by about 30%. “This is not a matter of simply replacing one production method with another, but of reinventing the way aviation engines are conceived and designed” said Giorgio Abrate, Avio Aero engineering leader.
Additionally, the Italian Government is also considering additive manufacturing as one of the most important enabling technologies to address the objectives pursued under the National Industry 4.0 Plan launched at the end of 2017. The Italian Ministry of Economic Development has undertaken actions to support Avio Aero's initiative in Brindisi as part of a broader and more significant contribution to the digital transformation of the manufacturing industry in Italy.
The main Avio Aero responsibilities include engine systems, control systems and software, combustion systems and both the power and accessory gearboxes.
https://www.youtube.com/watch?v=D9-Jjs5D4kM
ATP power gearboxes are the first Avio Aero-produced gearbox featuring an additively manufactured main housing. The use of additive allowed the design engineers to explore new design methods not previously available with traditional manufacturing techniques. “These include the use of new alloys because some of the typical manufacturing trade-off from the past (e.g. weight vs. cost) doesn’t exist with additive. Now, new solutions can be found to benefit both weight and cost efficiencies at the same time,” claims Luca Bedon, senior engineering section manager for aero dynamics at Avio Aero.
The ATP combustor has been designed by the Avio Aero engineers around a “reverse flow” configuration to minimize its length and to improve overall engine weight and installation. In this case, additive has proven to be a real game changer. In addition to the flexibility introduced in the mechanical and thermal design, additive allowed Avio Aero to prototype and test a number of design concepts that conventional manufacturing processes would not allow within the program schedule. With additive manufacturing, Avio Aero’s engineers were able to validate design experimentally, learning from each iteration.
The mechanical design of the 2-stage high pressure turbine (HPT) and the 3-stage power turbine (PT) as well as the high pressure compressor (HPC) are carried out by the Engineering Design Center (EDC) located in Warsaw, Poland. The team is supported by the GE Aviation team in Munich, Germany, who support the overall mechanical design process and, in particular, supported the design of the HPC. The Prague, Czech Republic team is responsible for the assembly, instrumentation, test and certification of the ATP.
The ATP engine earned another record: it will be the first “digital native” aviation engine because it was developed using advanced 3D modeling. Sensors in the engine will gather data and allow users to build a so-called digital twin of the ATP. This virtual model of the engine will factor in on real conditions, helping operators predict the right time for maintenance and increasing efficiencies of the engine and overall aircraft.
GE's new turboprop engine sets the bar high for what can be achieved through additive manufacturing. What will additive transform next?
https://youtu.be/KqcRm-maZrM