Investing in People: How a Pioneering Factory in India Is Building Its Workforce
June 20, 2024 | by Christine Gibson
In May 2014, less than two years after breaking ground, GE opened a $200 million state-of-the-art manufacturing plant on the outskirts of Pune, India. Its 250,000-square-foot shop was studded corner to corner with advanced equipment: electron-beam welding machines, vacuum furnaces, 3D laser trackers. But it would take a little longer to assemble the facility’s most important asset: its staff.
Over the next decade, the plant’s leaders built a skilled workforce from the ground up, training more than 5,000 local engineers and operators in precision aerospace manufacturing processes. As the employee rolls lengthened, output grew tenfold.
Today, GE Aerospace’s facility in Pune manufactures hundreds of different components for the company, serving all of its commercial jet engine lines, from the CF6 to the GE9X. As the aviation market expands in India and recovers abroad, orders for these engine parts are outstripping pre-pandemic levels, and the Pune site’s high performance has put it in a position to support a company-wide ramp-up.
To help meet demand, GE Aerospace is allocating $30 million to expand production at the Pune plant, part of a $650 million investment in the company’s global manufacturing sites and supply chain. The funding will allow the facility in Pune to build additional parts, some of which have never been made in India, and take advantage of pioneering manufacturing processes.
“This is a great recognition of our teams’ capabilities,” says Amol Nagar, the Pune facility’s managing director. “Every year we’re getting better — integrating advanced technology and enhancing our skill.”
A Homegrown Workforce
The investment is also a vote of confidence that the shop can adapt quickly to growth — whether that means taking on new projects or accelerating production on its existing lines. As one of GE’s first multimodal manufacturing sites, Pune was designed to be flexible. In a multimodal factory, teams can build multiple products using the same infrastructure and equipment, making it easier to respond to fluctuations in demand and get the most out of the space.
While the multimodal approach helps cut costs and maintain economies of scale, it also requires a highly skilled, versatile staff — which, in the early days at Pune, presented a significant obstacle. India has the largest engineering workforce in the world, but when the Pune plant opened, the nation’s aviation manufacturing sector was just starting to take off. For decades, government-owned R&D organizations and factories had dominated aerospace in India, and they focused mostly on military applications. As a result, the country didn’t have a ready-made pool of private-sector expertise. So the Pune leaders developed their own.
“We wanted to create a high-performance teaming culture where teams are empowered to make the decisions for their cell,” Nagar says. “We decided to train our own people to fulfill our vision.”
How did they do it? By creating an in-house aerospace manufacturing school designed to foster local talent. Following a curriculum drawn up especially for the Pune site by a university professor, the plant’s two-year apprentice program bridges theory and practice, illustrating how the concepts participants learned in college are applied in the industry. In addition to more formal classroom sessions, trainees gain hands-on experience by shadowing a mentor on the job.
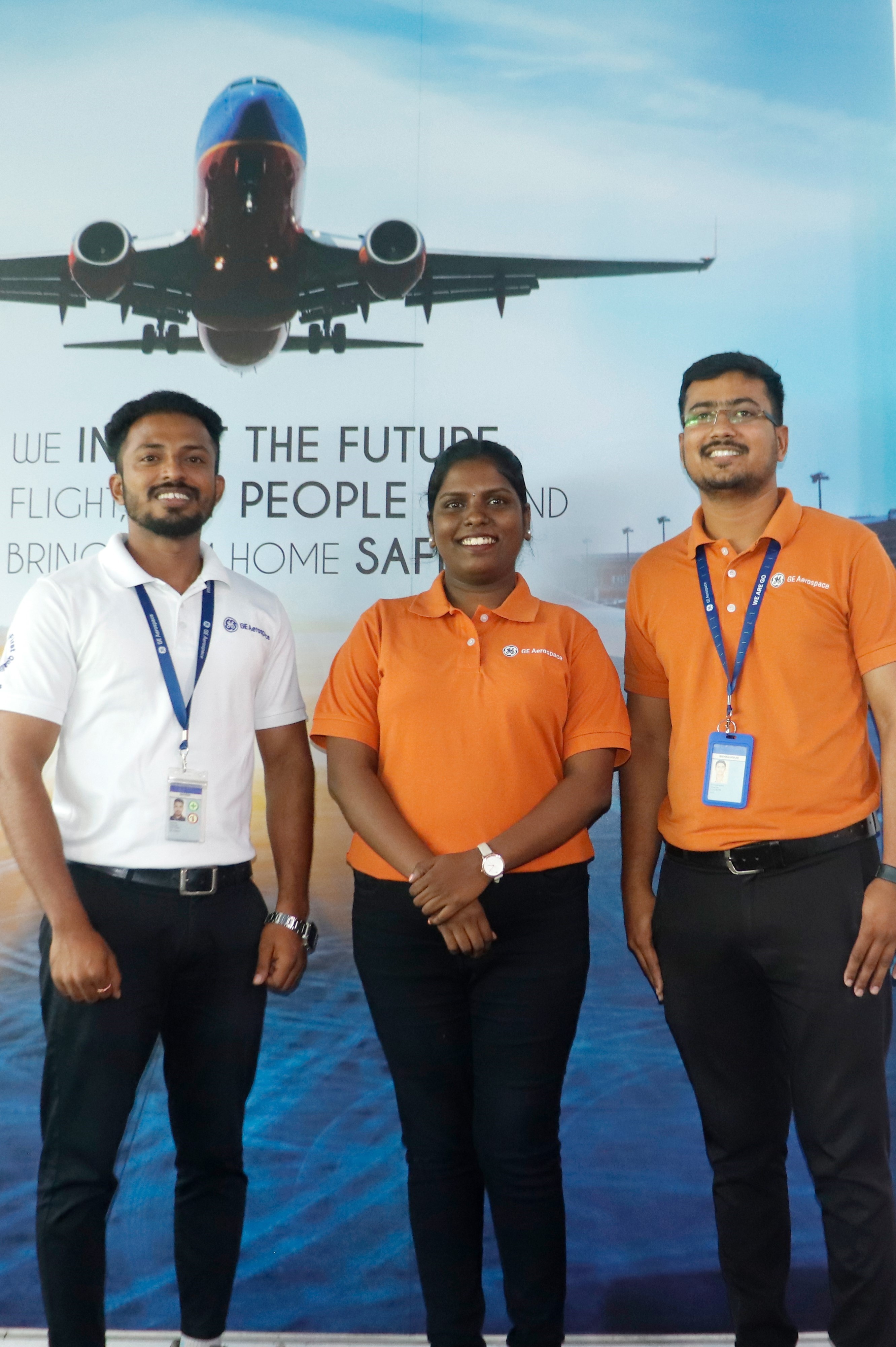
“GE gave me the foundational skills I needed to be a mechanical engineer,” says Namrata Motling, a member of the Pune plant’s first class of homegrown apprentices. Now a materials planning specialist, she says she joined the program as a “fresher,” Indian slang for a new graduate brimming with knowledge but lacking in experience. “They taught me CNC programming and routing,” she adds, referring to computer numerical control of automated manufacturing tools. “And when I was done, my team leader trusted me to run the machines for my team.”
Perpetual Learning
Motling’s training continued even as she grew more comfortable on the shop floor; junior engineers on the site’s high-performance teams are regularly instructed in safety and quality control practices specific to their projects. For example, Mahesh Hiremath, who also started as an apprentice, now leads a safety boot camp for new hires, demonstrating best practices in everything from chemical management to forklift operation to working at height.
“At GE Aerospace, safety is our priority, and as a part of EHS [environmental health and safety] training we have first aid and firefighting trainings imparted to our employees that help us grow informed and educated citizens within the community as well,” Hiremath says. “That’s why we’re taking extra time to educate our workers.”
More seasoned employees can apply to the Pune facility’s Emerging Leaders Program (ELP), a two-year introduction to the management tier. As they rotate through different leadership teams, participants gain a broader perspective of the business — vital when overseeing the operations of a multifunctional plant.
“ELP helped me understand what the other teams were doing,” says Bhimashankar Dhavle, a mechanical engineer who completed the ELP program in 2019. “What are their expectations? What are their challenges? How can I mitigate those challenges?” Dhavle, who was hired as an apprentice, earned his bachelor’s degree while working on the production line, but he found his calling during his final ELP rotation, in supply chain management. He’s now a master planner in materials and production, and he credits ELP with teaching him how to better serve his customers and colleagues.
For his part, Nagar, the managing director of the facility, takes pride in the fact that most of the new apprentices there are recruited by existing employees, drawn in by good word of mouth.
“I see that momentum, and it inspires me every day,” he says. “We are investing in people. Our intent is to spread this goodness, and in the process we can also build an organization that is learning, growing, and vibrant.”