Get Smart: GE Aerospace Unveils Plan for Smart Factory, Scores Big Thai Airways Order at Singapore Airshow
February 26, 2024 | by Jay Stowe
GE Aerospace’s Engine Services facility in Singapore (GEAESS) has chalked up a series of impressive credits in its time. Here are three, for starters: It’s the company’s largest maintenance, repair, and overhaul (MRO) site for engine components, it handles more than 60% of the company’s component repairs by volume, and in 2021 it became the first MRO site to use additive manufacturing technology to repair commercial engine parts.
This week, at the Singapore Airshow, it announced another significant advance: an $11 million investment to transform the facility into a state-of-the-art “Smart Factory” that will leverage lean manufacturing processes and innovative technologies to revolutionize engine repair and expand workforce skills.
While GE Aerospace has been operating in Singapore for more than 40 years, the support it received from the Singapore Economic Development Board has been crucial to getting the Smart Factory concept off the ground. In an effort to meet surging growth in component demand, the Smart Factory will initially be developed within the company’s plant at Seletar Aerospace Park and eventually expand to two other plants located at Loyang Industrial Park. The concept is to combine technology, automation, digitalization, and lean practices to transform component repair. Ultimately, the goal is to achieve higher productivity, better quality control, reduced costs, shorter lead times, and to improve customer satisfaction.
“Our Smart Factory investment represents the next chapter in our longstanding partnership with the Singapore Economic Development Board,” said Russell Stokes, president and chief executive officer of commercial engines and services at GE Aerospace. “This facility will support the government’s broader economic goal of job creation while driving our innovation and competitiveness in the global MRO market to a new level.”
GEAESS was the first MRO facility in the world to implement new additive manufacturing technology to repair commercial jet engine airfoil components (the rows of concentric blades that rotate inside an engine’s compressor and turbine sections). The Smart Factory will expand the site’s additive capabilities, focusing initially on high pressure compressor airfoils for GEnx and CFM LEAP engines, and eventually CFM56, CF6, and CF34 engine models. (CFM LEAP and CFM56 engines are products of CFM International, a 50-50 joint company between GE Aerospace and Safran Aircraft Engines.)
Plans call for the Smart Factory to develop and implement a number of advanced technologies, including automated inspection systems (for measuring and detecting dimensional and surface defects), 3D-printing machines (to build additive parts on-site), and material removal processes (to polish, shape, and reprofile the leading edges of airfoil blades). The new Smart Factory will also integrate robotics, cloud storage, data analytics, and Internet of Things technology to create a highly connected and intelligent production environment.
“With its strategic location at the heart of the Asia-Pacific, Singapore is well-positioned to benefit from the growth potential of aerospace-related activities, especially MRO,” says Iain Rodger, managing director and executive site leader of GE Aerospace’s Component Repair facility in Singapore. “GE Aerospace is proud to be a leading partner in Singapore’s aerospace journey and we anticipate our growth opportunities in additive manufacturing, digitalization, automation, and robotics will all drive more technically skilled jobs.”
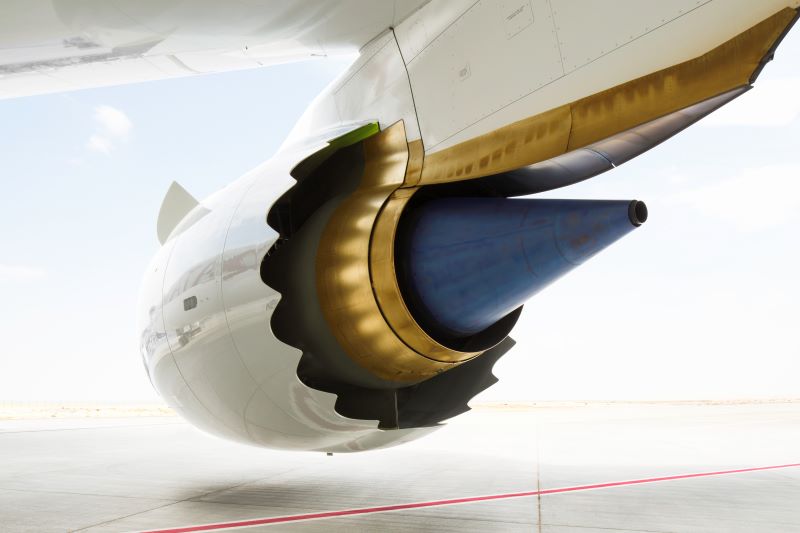
GE Aerospace had more good news to share on the first day of the Singapore Airshow: Thai Airways placed an order to power 45 new Boeing 787 Dreamliners with GEnx-1B engines, making GEnx the cornerstone of the airline’s long-term plan to open new markets while meeting its environmental commitments. The announcement came on the heels of a big year in which the GEnx product line added both LATAM Airlines and Riyadh Air as brand-new customers. What’s more, the GEnx engine family recently surpassed 52 million flight hours since entry into service in 2011, making it the fastest-selling high-thrust engine in company history with nearly 3,000 engines in service and on backlog, including spares.
The GEnx powers two out of every three 787 aircraft in service, providing a 1.4% fuel burn savings for the typical 787 mission compared to its competition. Like all GE Aerospace engines, the GEnx can operate on approved blends of sustainable aviation fuel (SAF).
“To accomplish the company’s carbon neutral goals by 2050, the 45 new Boeing 787 Dreamliners will be equipped with GEnx engines, which are known for their cutting edge technology and reduced environmental impact,” said Chai Eamsiri, chief executive officer of Thai Airways.
GE Aerospace celebrated one more auspicious first at the airshow. A China Eastern Airlines COMAC C919 narrowbody airliner made its international debut, flying over the Changi Exhibition Center powered by CFM LEAP-1C engines. It was the Chinese-made jet’s first flight outside of Chinese territory. The airshow, which ran from February 20 to 25, set a new attendance record, drawing close to 60,000 trade delegates over the first four days.