GE Aerospace’s AI Hackathon Turns Hot Weather Challenge Into Opportunity in the Middle East
January 27, 2025 | by GE Aerospace Staff
If you ask Ali Farah, director of the GE Aerospace Middle East Technology Center (MTC) in Dubai, he’ll tell you in no uncertain terms that the hot, dusty, and humid environment in the Middle East is “both a curse and a good thing.” While harsh weather forces engines to work harder and can impede durability, it also breeds innovation. “With necessity as the mother of invention, what we learn and develop here eventually benefits customers everywhere,” he says.
GE Aerospace established the MTC in 2015 to address engine durability issues in hot and harsh environments and develop innovative predictive maintenance technologies for commercial airlines throughout the Middle East. In the decade since, the center has developed a whole range of solutions that are now deployed across the globe. One example is analytics-based maintenance (ABM) — physics-based software models that help airlines ensure better fleet stability by predicting when engines should be brought in for servicing.
This solution is valuable for many engine types, but none more so than the fast-growing fleet of more than 750 CFM LEAP* engines that are flown by over 20 airlines in the region, including Etihad Airways, Gulf Air, Kuwait Airways, Pegasus Airlines, Turkish Airlines, Qatar Airways, Saudia, Air Arabia, Flynas, Jazeera Airways, Egyptair, Air Cairo, Flyadeal, and SalamAir.
Tapping Into FLIGHT DECK, a Global Network, and AI
As these fleets grow, the MTC aims to speed up delivery of insights that bring value to customers. This ambition is aligned with GE Aerospace’s proprietary operating model, called FLIGHT DECK, which is designed to help drive continuous improvement. Case in point: The MTC has begun to leverage artificial intelligence (AI) in its predictive maintenance practices while keeping humans always in the loop to ensure oversight.
To get the AI ball rolling, Farah invited Senior Director of Software Engineering Sama Kanbour and her team to Dubai for a “sprint” to refine what customers are really after. (Mohamed Ali, senior vice president of engineering at GE Aerospace, dropped by during the sprint to help motivate the team.) A few weeks later, a group of 12 GE Aerospace customer advocates and software developers participated in an AI-focused hackathon. The intense five-day period was focused on delivering an AI-enabled solution to speed up the ABM analysis.
“Our goal was to use AI technology to improve our turnaround time by driving human productivity, while not compromising safety — always our top priority — or quality,” says Farah.
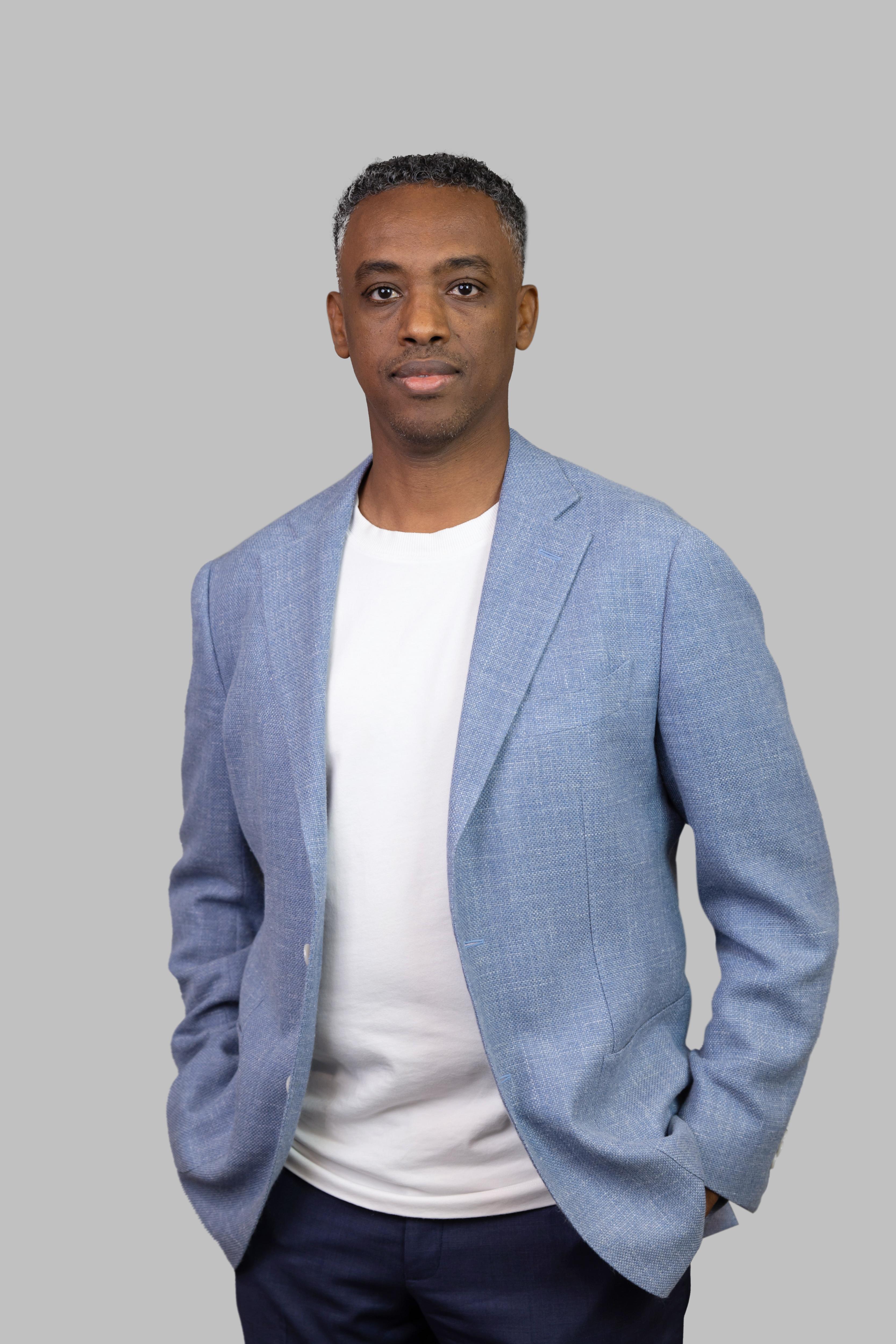
Experts from across the company participated in the hackathon, including developers based in Cincinnati, Bengaluru, and Dubai. Divided into a customer advocate team and a software developer team, the hackers used a series of half-day cross-functional development sprints to rapidly iterate a solution. “At the end of each sprint, we would get together, see what we learned, test what was developed, make new requests, and then develop new tasks for the next four hours,” explains Dan Kamen, the lean operations leader on the FLIGHT DECK Transformation Team, based in New York, who helped facilitate the hackathon.
“The power of the hackathon was its ability to bring experts together where they could focus on this one goal,” says Sundar Krishnaswami, consulting engineer in analytics and data science at GE Aerospace’s John F. Welch Technology Centre (JFWTC) in Bengaluru. “This builds a strong connection between the customer team and the programmers, all sitting around one table. With instant communication of both customer expectations and software possibilities, there is mutual appreciation of what can be done and what needs to be done.”
“A Geek at Heart”
The hackathon was rewarding for everyone involved. But for Andrea Casallas, whose day job is in analytics engineering at the MTC, it was a whole new experience. For years, Casallas explains, she dabbled in computer programming as a hobby, taking her time to create software in various coding languages. “I’m a geek at heart,” she says.
Last year, Casallas graduated with a master’s degree in computer science, with a focus on artificial intelligence. Naturally, she says, “I begged my boss to let me put into practice what I had learned.” She got what she wanted: a spot on the software development team. But “because this is my first hackathon, it was very intense for me,” she says. “We were working for 10 to 12 hours straight, and then at home I would continue thinking about it. For the whole five days, all my thoughts were about the hackathon. I was even dreaming about it!”
Now, she adds, “I look back and say it was exciting. Brainstorming with these experts was amazing. Going back and forth, discussing all the different ideas, translating them into code — that was the fun part. And in the end, I was able to produce something, point to this section of the code, and say, ‘This is my baby. This is a piece of me!’”
More Than 60% Time Reduction
The five-day event was a success. The teams came up with a Minimum Viable Product software program that trimmed 22 steps from the process, added 10 new features, and used AI to help reduce ABM response times by more than 60%. The solution is currently going through further testing, and the plan is to deploy it in the field later this year.
“What the team accomplished was to automate a bunch of repetitive tasks formerly done by humans, thereby allowing engineers to focus on interpretation and insights processing for customers,” says Krishnaswami.
No matter how hot, humid, or dusty the weather, the hackathon solutions could give airlines faster access to more updated maintenance planning insights for their engines. “[This] demonstrates what happens when we deploy FLIGHT DECK and bring global and local teams together to solve problems that matter to our customers,” says Farah.
*CFM International is a 50-50 joint company between GE Aerospace and Safran Aircraft Engines.