In the drive for innovative new solutions to meet the global aviation industry’s desire for fewer emissions, there’s an all-hands-on-deck approach behind the Revolutionary Innovation for Sustainable Engines (RISE) technology development and demonstration program. The words sound simple enough, but the challenge to the global aviation industry is enormous — and it’s driving the all-hands-on-deck approach behind the Revolutionary Innovation for Sustainable Engines (RISE) technology development and demonstration program. Unveiled in 2021 by CFM International, a 50-50 joint company between GE Aerospace and Safran Aircraft Engines, the RISE program is advancing technologies to support a future aircraft engine that aims to be 20% more fuel-efficient, with 20% lower carbon emissions, than current commercial engines.
The good news — confirmed by CFM executives at a recent CFM-sponsored webinar hosted by Aviation Week — is that the RISE program continues to make real progress, thanks to efforts by a global team of more than 2,000 CFM engineers, multiple industry collaborations, and ongoing research partnerships with public sector agencies in the U.S. and Europe.
“Sustainability is a team sport. We can only cross the finish line if we are working together across the industry,” said Delphine Dijoud, vice president engineering deputy for commercial engines at Safran Aircraft Engines, who presented the webinar alongside Arjan Hegeman, general manager of future of flight technology at GE Aerospace.
Both presenters reiterated their confidence in Open Fan technology as the way forward. “Over the past 50 years ducted engines have steadily improved, but they are now approaching the limits in terms of efficiency,” while unducted engine architecture is “just beginning to climb a new S curve of potential in terms of propulsive efficiency,” said Dijoud.
They also expressed excitement at the advances made possible by RISE program technologies. “It truly is one of the most ambitious demonstrator programs in the history of our company,” Hegeman said. “There’s a need to get to a 2050 net zero industry, and RISE plays a very important part of getting to that milestone.”
Here are five things to know about the RISE program.
1. Open Fan engine architecture has come a long way, baby.
The experimental GE36 engine, developed by GE Aerospace in the 1980s, showed off the benefits of Open Fan (aka unducted) engine architecture. While the engine delivered unprecedented fuel efficiency, with two sets of exposed, counter-rotating fan blades, the GE36 was heavy and loud. Fast-forward to now, when a much simpler design leverages 21st-century technologies to eliminate weight and noise issues and achieve improved fuel efficiencies.
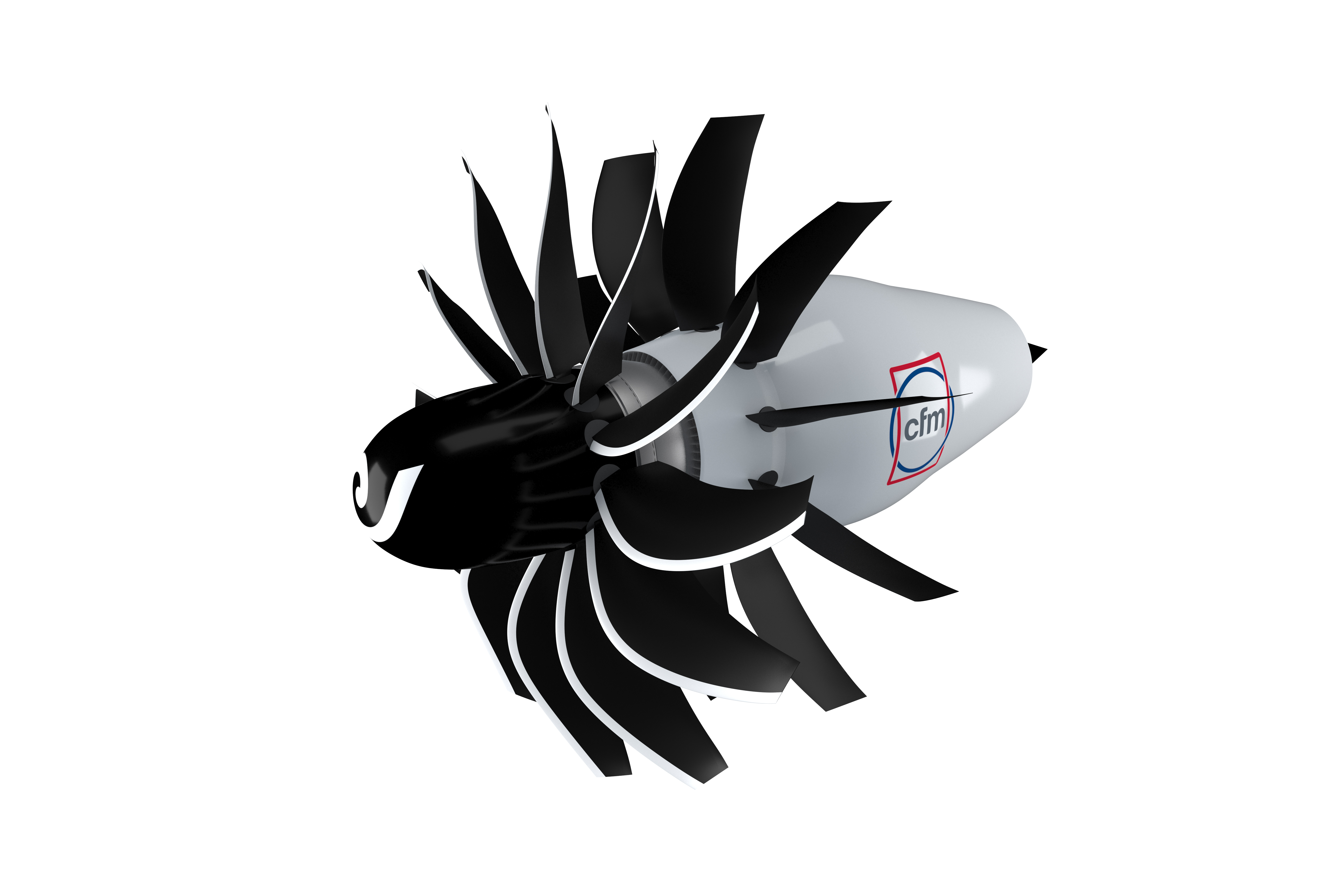
The single-stage Open Fan engine is key to achieving a bypass ratio more than five times greater than tomorrow’s most advanced ducted engines. It will also be equipped with carbon-fiber composite blades for weight reduction, superior strength, and durability. Meanwhile, using the power of supercomputing to analyze aerodynamics at a microscopic level, RISE program engineers have come up with a fan design that minimizes noise while maximizing efficiency.
“The computational capabilities, our code, and the GPU clusters themselves truly have enabled our teams to understand the detailed aerodynamics and optimize the system, moving it from a counter-rotating fan to a very simple, single-stage fan that meets the acoustics requirements that everybody has come to expect,” said Hegeman. (Read about GE Aerospace’s latest supercomputing project here.)
2. Advanced compact core technologies are also crucial to achieving RISE program goals.
While Open Fan technology — arguably the most high-profile feature of the RISE demonstrator program — will lead to double-digit gains in fuel efficiency, it won’t achieve the more than 20% target on its own. Development of a lightweight compact core, which houses the compression and combustion modules, is being re-engineered to be smaller and optimize thermal efficiency, with an advanced cooling system and materials that can withstand extremely high temperatures. The core is being designed for compatibility with next-generation fuels, including unblended sustainable aviation fuel (SAF) and hydrogen, as well as with hybrid electric systems like the ones GE Aerospace is currently developing with NASA. It also uses adaptive engine technologies, also known as variable bypass architecture, to boost performance while allowing safe and efficient operation at every stage of a flight. “It’s a technology that [can] vary the bypass and allow more thrust demand when it is needed, say during a takeoff or a climb, and much more bypass during a cruise-type environment,” Hegeman said.

Validation of RISE core technology was completed last year, and tests are now centered on endurance, a key consideration as more efficient engines are pushed to operate at higher air pressures and temperatures. “Long before we even build the actual demonstrator engine, we’re already taking components and subsystems through the durability basis,” he explained, referring to the standard that measures how long a part can function before maintenance or repair. “It’s an example of how serious we take the durability and safety of these engines.”
3. The progress is real — and the pace is accelerating.
The CFM RISE program has completed more than 250 tests and the pace continues to accelerate, with rigorous testing and research continuing around the world. “It’s not just within CFM,” Hegeman said. “We have a lot of partnerships and collaboration — within the U.S., with NASA, the FAA, the Department of Energy; within Europe, with Clean Aviation, with ONERA, with DLR and more.”
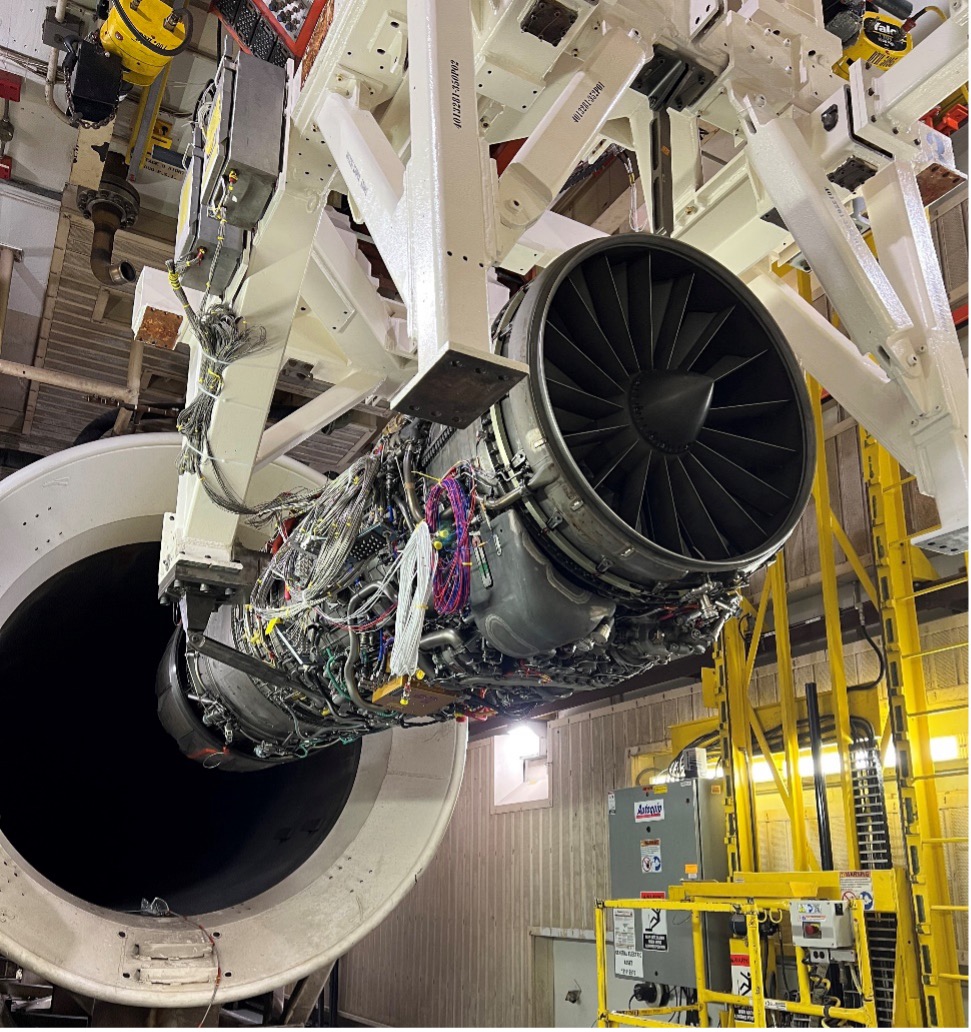
In 2024, the first 300-plus hours of wind tunnel testing were completed at a facility run by ONERA, the French national aerospace research center, using a one-fifth scale model of the Open Fan turbine. At two other sites, endurance tests on the high-pressure turbine (HPT) are being run on an F110 engine, with over 2,000 cycles accumulated. Next, Hegeman said, “we’ll switch to the same number of cycles one more time, but in an emulated environment where there is dust ingestion, which makes it even tougher.”
“We are investing in facility improvements and even in a brand-new facility to support this huge testing effort,” Dijoud said. “It’s becoming more real every day, with the first full-scale demonstrator parts that are now manufactured.”
4. The RISE program is advancing the world’s understanding of the science of non-CO2 emissions.
As RISE program engineers and technologists work to lower carbon emissions associated with air travel, they’re also making important discoveries related to non-CO2 emissions, such as nitrous oxide (NOx) emissions — gases produced during the combustion process that contribute to air pollution and the formation of airplane contrails.
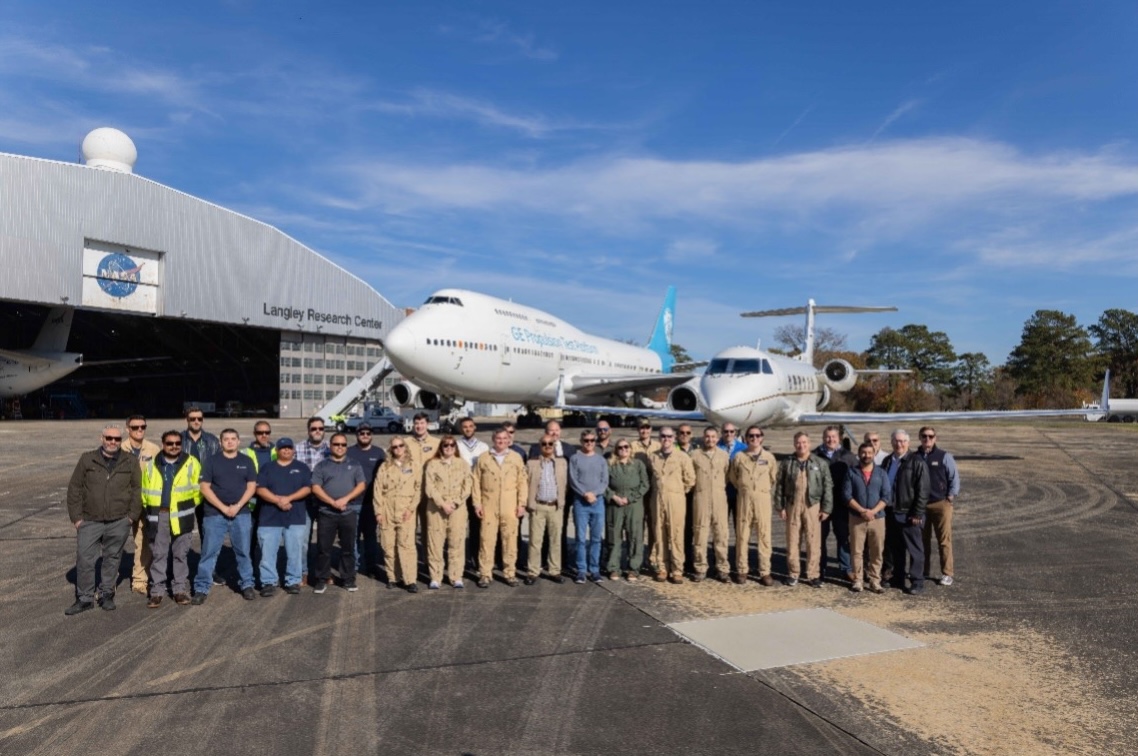
The program’s next-generation combustion technologies expand on components first developed for the GEnx engine. And GE Aerospace recently partnered with NASA to conduct groundbreaking contrail analysis tests using state-of-the-art lidar (light detection and ranging) technology to produce three-dimensional images that provide information about how contrails form and behave.
5. Multiple ground and flight tests set to take place this decade.
All systems remain go for ground and flight tests to begin in the coming years. CFM is collaborating with Airbus on an Open Fan flight demonstration, planned for later this decade, and actively working with the airframe manufacturer to “optimize the engine-to-aircraft integration through tests and simulations,” Dijoud said. Flight tests are important to advance understanding of engine performance, safety, noise, and aerodynamics in a real flight scenario — a key step before a groundbreaking engine can be developed.
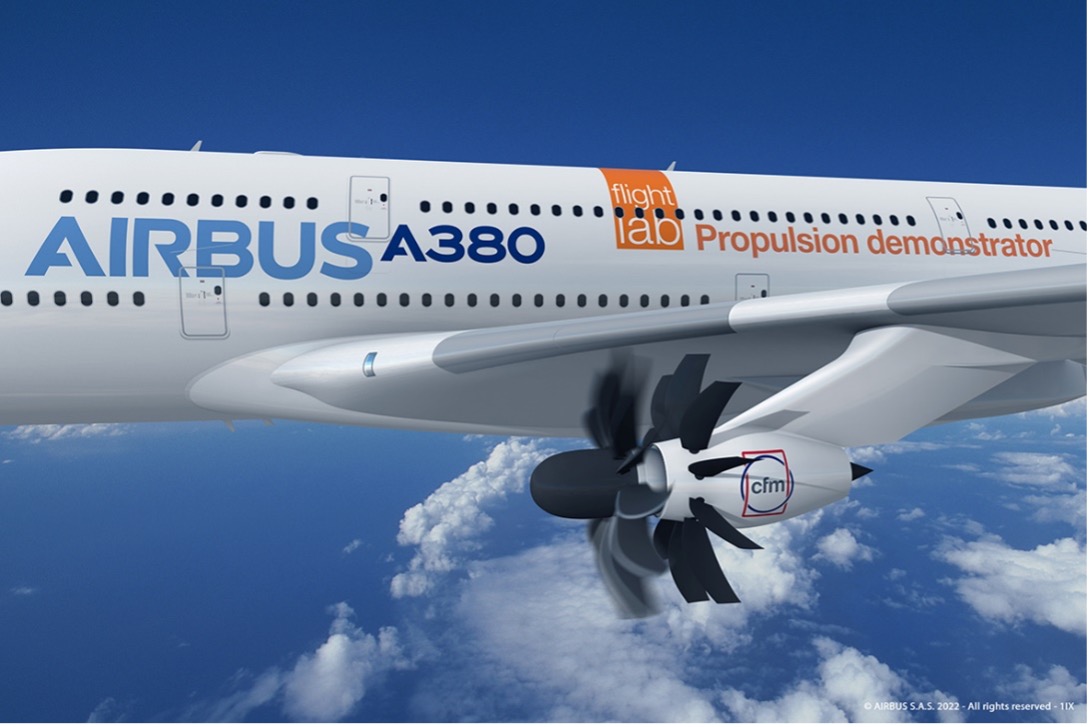
Both Dijoud and Hegeman expressed continued confidence in the RISE program technologies and key concept — that Open Fan technology is the way of the future. “The value proposition of RISE is that you get double-digit fuel efficiency coming out of the propulsive system,” Hegeman said. “Which means you don’t need to stress and tax the hot part of the engine as much to get to that 20% [efficiency] number. A ducted engine can never get to the 20% number without massively compromising its durability.”
“We keep learning, innovating, pushing the boundaries with every test, every simulation, every design tweak,” Dijoud said. “We continue to explore multiple pathways in order to shape this more sustainable future for aviation.”
To view the complete webinar, register at this link.