GE Aviation’s 100th anniversary year wouldn’t have been complete without a stop at the company’s biggest partner in the commercial aircraft engine business, Safran Aircraft Engines.
Throughout the past year, groups of GE Aviation employees who don’t normally visit customers during their normal workday were selected to attend special anniversary trips to see, firsthand, how the company’s products resonate in the field.
At the Safran facility in Villaroche, France, LEAP engines were lined up along production queues for final touches. Once a final wrench turn indicated the engine was ready for quality inspection, robots verified whether the world’s fastest-selling commercial jet engine was ready to be transported for aircraft installation. It wasn’t the every-day scene some of the visiting GE Aviation employees, including Beccy Mintram, Gianluca Longo and Gareth Jenkins, were used to.
“It was great to connect with other GE employees who I had never met, even employees from the same GE site! I think we had colleagues from more than five sites and all of us were working in different areas and on different projects—it just goes to show what a massive business GE Aviation is,” said Beccy, customer order and fulfillment specialist in Cheltenham, United Kingdom.
See, even though Beccy, Gianluca and Gareth work for GE Aviation, one of the world’s leading jet engine makers along with Safran, the company also makes electrical systems, power generation parts and other components at its facilities in Cheltenham, where Beccy and Gareth work. In Torino, Italy, GE Aviation’s Avio Aero manufactures engine accessory gearboxes where Gianluca works. They don’t normally walk by steel frames tilted in all directions and holding LEAP engines on the way to their desks.
More so, for Beccy, Gianluca and Gareth, they had never seen a whole commercial aircraft engine up close—front fan, core and all—before the commemorative November trip to close partner Safran.
“Working in Avio Aero, I only have the opportunity to see gearboxes. Seeing this component assembled with thousands of others, forming the whole engine, is really impactful,” Gianluca said.
Other participants in the 100 Flights program who had seen assembled jet engines before still left impressed by Safran’s use of automation and other technologies to help production meet unprecedented demand. More LEAP engines will need to be assembled each week by CFM International employees at GE and Safran than the pace at which the industry’s workhorse CFM56 engine was ever built.
Dave McCarthy, an aircraft mechanical engineer at GE’s Wales overhaul location in the United Kingdom, noticed vast differences between the Safran shop producing new engines compared to his shop conducting engine repairs. He was “very impressed by the scale … and the quality of advanced mechanical attachments to improve and assist the build process.”
Safran “had familiar sights to GE, for example, shadow boards for tools, but had enhanced these with technology where operators scan their tools in and out so they can track where any missing tools may have got to,” described Beccy Mintram. “Augmented reality was something I had not seen before and I was really surprised it could be used in this environment.”
Magdalena Malecka, GE mechanical components subsection manager in Warsaw, Poland, found the experience of seeing engines on the shop floor “incomparable” to drawings viewed on a computer screen.
While GE’s Aviation unit marked in 2019 100 years since a GE-made turbosupercharger launched the company, the CFM International joint venture isn’t quite half as old. However, the 50-50 company has sold more turbofans than any other civil jet engine manufacturer in history, including GE and Safran individually.
As CFM itself celebrated the 45th anniversary of the partnership in 2019, its ubiquitous CFM56 product line reached 1 billion flight hours powering travelers across the globe. The LEAP engine, the company’s newest product, has garnered approximately 19,000 orders and commitments to date from more than 100 airlines and leasing companies around the world.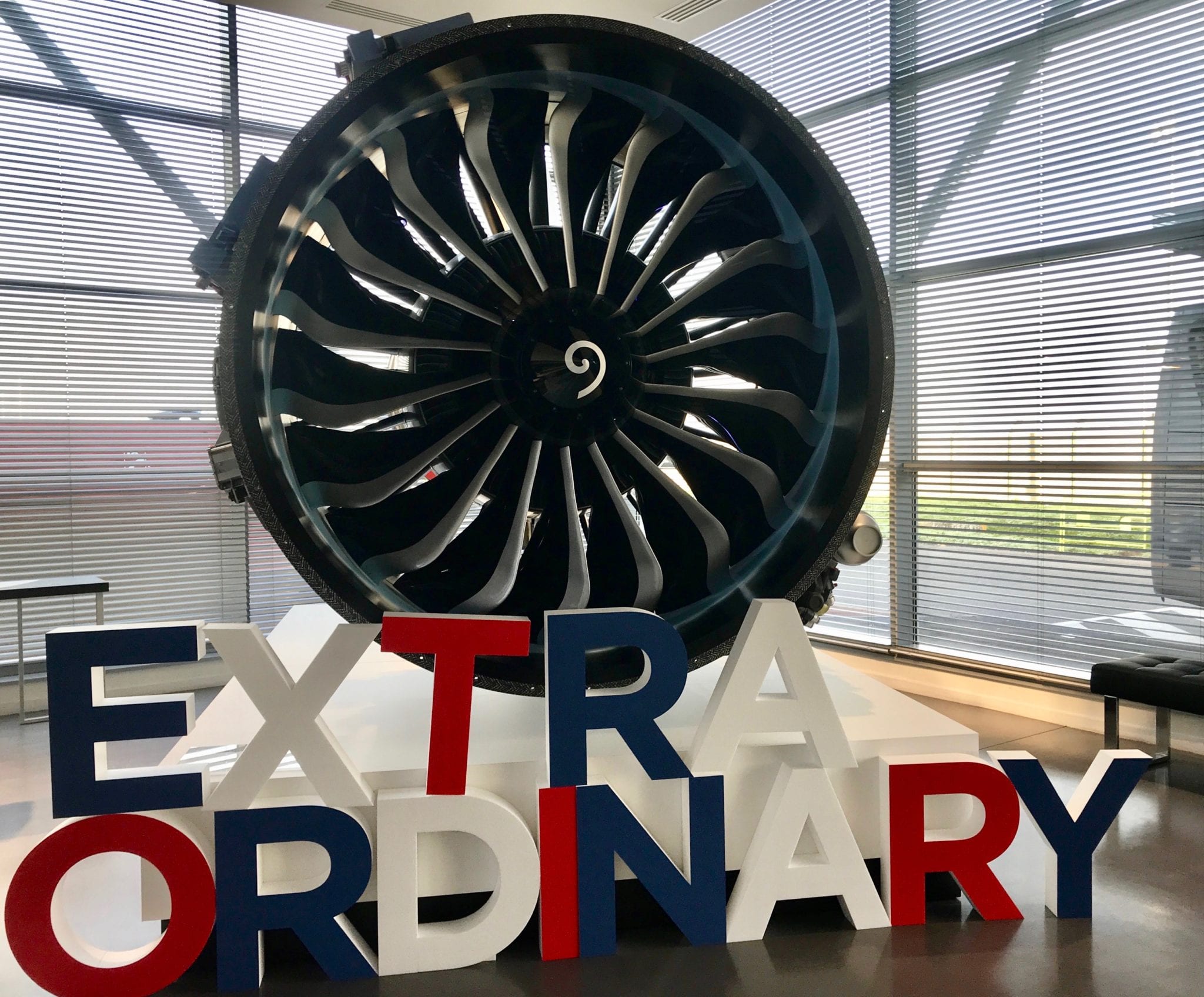
“Extraordinary Together” signs greeted the GE Aviation group upon its arrival to Safran’s Villaroche production plant.
“The key learning I am bringing back to the business is the realization and recognition of the partnership moto, which is evident right across our own business. [It is] perhaps forgotten too easily, but the same is true,” said Gareth Jenkins, business change manager in the Avionics Engineering Operations team at Cheltenham.
“Our incredible people continue to build the groundbreaking things only a very different partnership can create. This has great importance in line with the knowledge-sharing program and culture we are looking to expand and establish, but also on a personal level through the partnerships I can build across the organisation in order that we continue to make groundbreaking things and changes,” Gareth said.
Throughout the past year, groups of GE Aviation employees who don’t normally visit customers during their normal workday were selected to attend special anniversary trips to see, firsthand, how the company’s products resonate in the field.
At the Safran facility in Villaroche, France, LEAP engines were lined up along production queues for final touches. Once a final wrench turn indicated the engine was ready for quality inspection, robots verified whether the world’s fastest-selling commercial jet engine was ready to be transported for aircraft installation. It wasn’t the every-day scene some of the visiting GE Aviation employees, including Beccy Mintram, Gianluca Longo and Gareth Jenkins, were used to.
Gareth Jenkins, who works for GE Aviation.
“It was great to connect with other GE employees who I had never met, even employees from the same GE site! I think we had colleagues from more than five sites and all of us were working in different areas and on different projects—it just goes to show what a massive business GE Aviation is,” said Beccy, customer order and fulfillment specialist in Cheltenham, United Kingdom.
See, even though Beccy, Gianluca and Gareth work for GE Aviation, one of the world’s leading jet engine makers along with Safran, the company also makes electrical systems, power generation parts and other components at its facilities in Cheltenham, where Beccy and Gareth work. In Torino, Italy, GE Aviation’s Avio Aero manufactures engine accessory gearboxes where Gianluca works. They don’t normally walk by steel frames tilted in all directions and holding LEAP engines on the way to their desks.
More so, for Beccy, Gianluca and Gareth, they had never seen a whole commercial aircraft engine up close—front fan, core and all—before the commemorative November trip to close partner Safran.
“Working in Avio Aero, I only have the opportunity to see gearboxes. Seeing this component assembled with thousands of others, forming the whole engine, is really impactful,” Gianluca said.
Top and above: Teams from GE Aviation, Safran and Avio Aero came together for GE Aviation's 100-year anniversary.
Other participants in the 100 Flights program who had seen assembled jet engines before still left impressed by Safran’s use of automation and other technologies to help production meet unprecedented demand. More LEAP engines will need to be assembled each week by CFM International employees at GE and Safran than the pace at which the industry’s workhorse CFM56 engine was ever built.
Dave McCarthy, an aircraft mechanical engineer at GE’s Wales overhaul location in the United Kingdom, noticed vast differences between the Safran shop producing new engines compared to his shop conducting engine repairs. He was “very impressed by the scale … and the quality of advanced mechanical attachments to improve and assist the build process.”
Safran “had familiar sights to GE, for example, shadow boards for tools, but had enhanced these with technology where operators scan their tools in and out so they can track where any missing tools may have got to,” described Beccy Mintram. “Augmented reality was something I had not seen before and I was really surprised it could be used in this environment.”
Petra Cerno and Beccy Mintram.
Magdalena Malecka, GE mechanical components subsection manager in Warsaw, Poland, found the experience of seeing engines on the shop floor “incomparable” to drawings viewed on a computer screen.
While GE’s Aviation unit marked in 2019 100 years since a GE-made turbosupercharger launched the company, the CFM International joint venture isn’t quite half as old. However, the 50-50 company has sold more turbofans than any other civil jet engine manufacturer in history, including GE and Safran individually.
As CFM itself celebrated the 45th anniversary of the partnership in 2019, its ubiquitous CFM56 product line reached 1 billion flight hours powering travelers across the globe. The LEAP engine, the company’s newest product, has garnered approximately 19,000 orders and commitments to date from more than 100 airlines and leasing companies around the world.
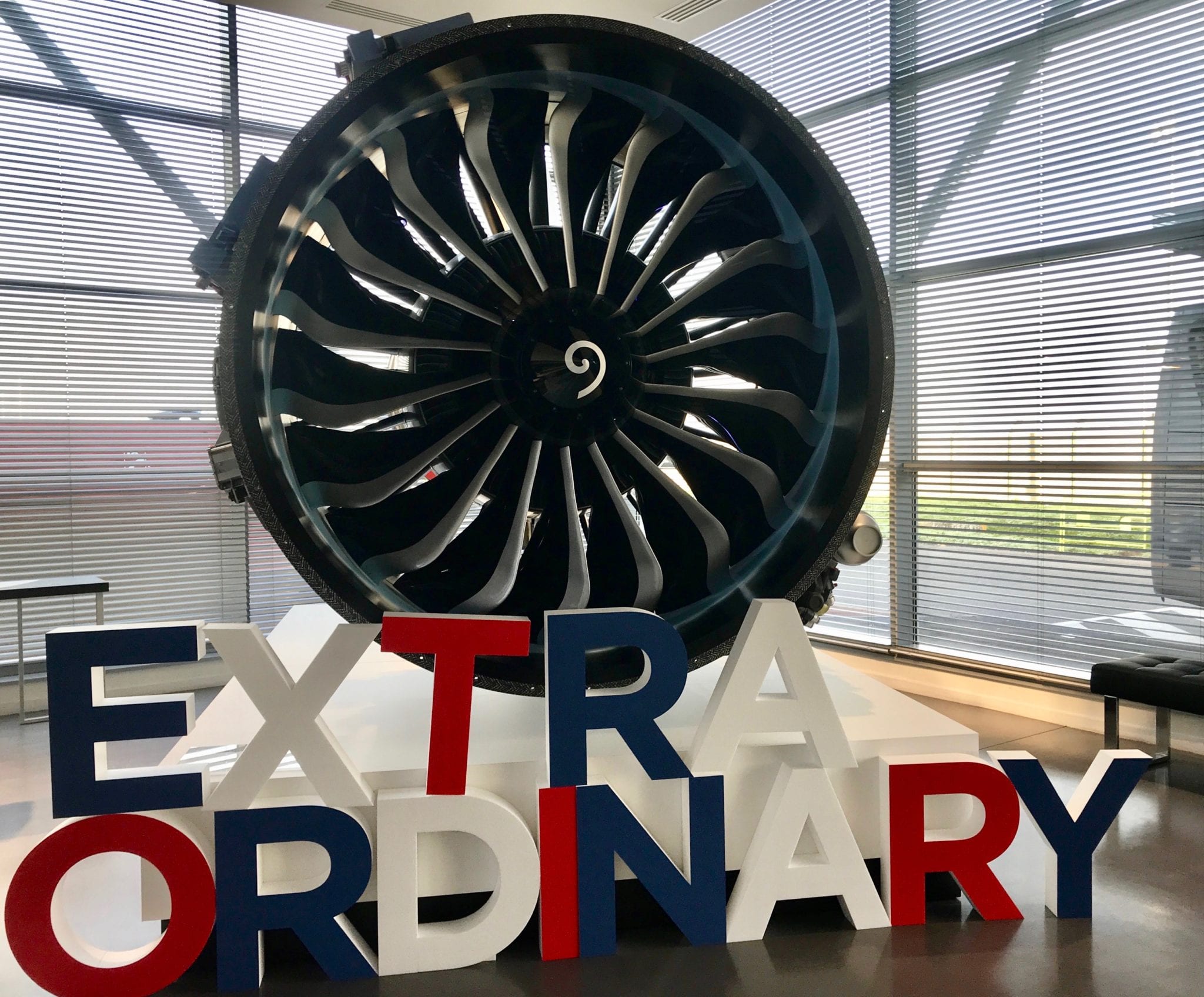
“Extraordinary Together” signs greeted the GE Aviation group upon its arrival to Safran’s Villaroche production plant.
“The key learning I am bringing back to the business is the realization and recognition of the partnership moto, which is evident right across our own business. [It is] perhaps forgotten too easily, but the same is true,” said Gareth Jenkins, business change manager in the Avionics Engineering Operations team at Cheltenham.
“Our incredible people continue to build the groundbreaking things only a very different partnership can create. This has great importance in line with the knowledge-sharing program and culture we are looking to expand and establish, but also on a personal level through the partnerships I can build across the organisation in order that we continue to make groundbreaking things and changes,” Gareth said.