Outside the Box: How GE Aviation Entered the Brave New World of Additive Manufacturing
August 08, 2019 | by Rick Kennedy
GE Aviation is recognized worldwide as a leading proponent of additive manufacturing, a revolutionary technology that has been pursued at the parent company’s research laboratories for four decades. Indeed, since the 1980s, the GE Global Research Center (GRC) in Niskayuna, New York, has been heavily involved in additive manufacturing research, going so far as to create a dedicated laboratory in 2011. Nevertheless, practical applications of the technology proved elusive.
That changed in 2012. GE Aviation’s aggressive entry into this brave new world began that year with the acquisition of a small additive company—Morris Technologies, based north of Cincinnati, Ohio—and soon led to the first complex component made “additively” for a production jet engine. It was a breakthrough in the truest sense of the word: it transformed the company’s approach to designing and manufacturing some of the most complex parts in a jet engine.
Additive manufacturing—otherwise known as 3D printing—involves taking digital designs from computer-aided-design (CAD) software and building a component by laying horizontal cross-sections layer by layer. Additive components are typically lighter and more durable than traditional parts, because they only put material where it is needed and require less welding and machining. Freed of traditional restrictions, additive manufacturing dramatically expands design possibilities for engineers while reducing wasted material.
GE Aviation and Morris Technologies had a long history together. In the 1990s, the company worked with Morris on the rapid prototyping of engine components in early development. Co-created by Cincinnati brothers Greg and Wendell Morris, along with Bill Noack, it had emerged as a world-leading “job shop” where additive manufacturing machines were used to produce advanced components for several industries, from medical to jewelry. With small factories in the Cincinnati suburbs of Sharonville and West Chester, Morris Technologies had become one of the largest operators of additive machines.
By 2003, GE Aviation had developed a new fuel nozzle injector (later incorporated into the best-selling LEAP engine) with a complex design nearly impossible to produce conventionally because of its elaborate interior geometries and miniscule passages. If produced using conventional casting methods, every injector inside the fuel nozzle would require at least 20 parts welded and brazed together. That was a daunting and expensive proposition for a high-volume part. GE Aviation was forced to think “outside of the box” for a new manufacturing method.
Led by GE combustion engineer Marie McMasters, the company initiated a secret project with Morris Technologies to additively produce the complex fuel injector. Morris employees had to sign proprietary agreements like it was a classified program. The work continued quietly for years.
By 2005, Morris and GE achieved a significant breakthrough: a fuel injector made of the superalloy cobalt chromium. “We used this alloy for dental and medical products,” Greg Morris recalled. “GE was not familiar with it, and there was skepticism at first. But it proved highly durable.”
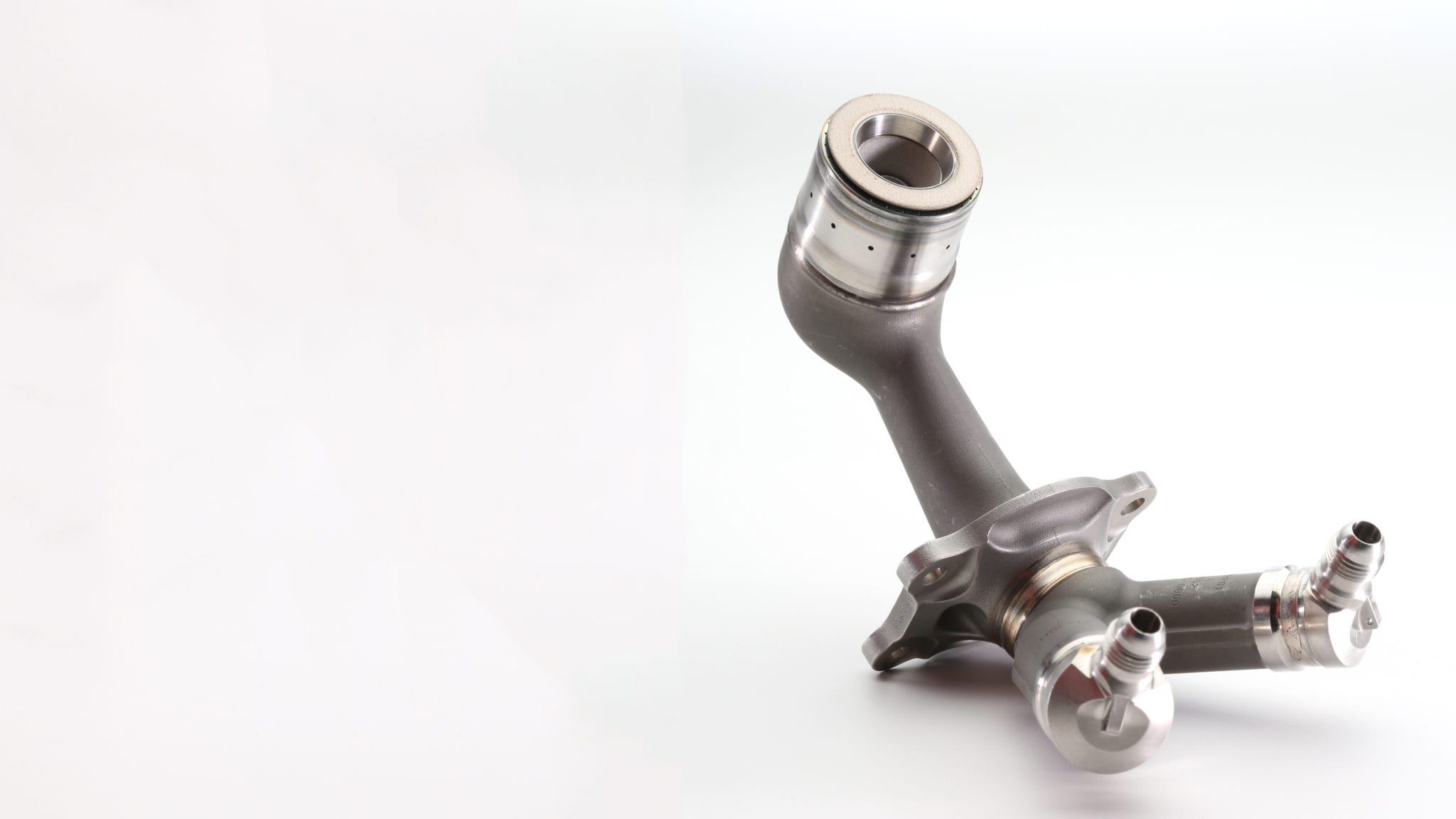
In 2012, Morris and GE developed the additive process parameters for mass-producing 19 fuel nozzle injectors for each LEAP engine, the new turbofan being developed for the single-aisle aircraft market by CFM International, a 50/50 venture owned jointly by GE and Safran Aircraft Engines. Two Aviation leaders at the time—Robert McEwan, a manufacturing general manager, and Mohammad Ehteshami, vice president of engineering—strongly advocated for an outright purchase of Morris Technologies. It was time to bring the innovative company into the GE family.
“When I saw what they could do with the nozzle, it was an epiphany,” recalled Ehteshami. “I think the first thing out of my mouth was ‘Buy them!’ ” Even when the purchase was disclosed in late 2012, GE kept mum about the years of secret additive development work on the LEAP fuel nozzle injector.
GE Aviation’s acquisition intrigued the aviation industry. As GE Aviation President and CEO David Joyce frequently asked his leadership team at the time, “Do you want to be on the inside, or the outside, of this [additive] revolution?”
That same year GE Aviation created the Additive Technology Center north of Cincinnati. The plant consolidated research equipment and additive machines acquired from Morris Technologies and intensified its research and development proficiencies from there. “The idea was to co-locate our most forward-thinking engineers in the additive world with R&D equipment, like they do in Silicon Valley or at the automotive headquarters in Detroit,” said Greg Morris, the center’s first manager.
The ATC began working closely with both GE Aviation and Avio Aero in Italy, which had also been recently acquired, to incorporate more additive components into engine designs. At the same time, GE Aviation’s Auburn, Alabama, plant was designated for large-scale additive manufacturing. Within a few years, rows of additive machines were installed at the Auburn site, producing thousands of fuel nozzle injectors for the LEAP engine.
In 2016, through two bold acquisitions, GE Aviation suddenly became a leading provider of the technology when it acquired two additive firms in Europe—Arcam AB and Concept Laser—and turned them into a new business: GE Additive. Based in Mölndal, Sweden, Arcam AB, inventor of electron beam melting (EBM) machines for metal-based additive manufacturing, is also a leading producer of advanced metal powders. At the time of the acquisition, Arcam already had a strong relationship with Avio Aero, which has been heavily engaged in EBM technology for several years.
https://www.youtube.com/watch?v=CUeDevI6kyE
Concept Laser, based in Lichtenfels, Germany, pioneered metal additive manufacturing with laser additive machines capable of processing various powder materials, including titanium, nickel-base, cobalt-chromium, and precious metal alloys, as well as hot-work and high-grade steels and aluminum. Immediately after the acquisitions, GE invested heavily in Arcam AB and Concept Laser operations to bolster their product lines and customer field support.
GE Aviation is using this new capability to drive additive opportunities across the jet engine portfolio. A classic example is GE’s new Catalyst turboprop engine launched in 2015. The Catalyst has more components designed and produced using additive manufacturing than any previous aviation engine, more than 25 percent of the overall engine. It doesn’t hurt that the additive parts also reduce weight and improve fuel consumption.
The company has come a long way since 2012. Yet it’s hard to imagine where GE Aviation would be today without that strategic acquisition of a small but innovative company just up the road in suburban Cincinnati.
“Morris Technologies led us to get into the market and develop our own additive machines and powder,” said Gary Mercer, vice president of engineering. “This technology is unique and has the promise of lower cost, while being lighter and more efficient. No technical trades—this is a win, win, and win.”
https://www.youtube.com/watch?v=55Yx2UBNUI4
That changed in 2012. GE Aviation’s aggressive entry into this brave new world began that year with the acquisition of a small additive company—Morris Technologies, based north of Cincinnati, Ohio—and soon led to the first complex component made “additively” for a production jet engine. It was a breakthrough in the truest sense of the word: it transformed the company’s approach to designing and manufacturing some of the most complex parts in a jet engine.
Additive manufacturing—otherwise known as 3D printing—involves taking digital designs from computer-aided-design (CAD) software and building a component by laying horizontal cross-sections layer by layer. Additive components are typically lighter and more durable than traditional parts, because they only put material where it is needed and require less welding and machining. Freed of traditional restrictions, additive manufacturing dramatically expands design possibilities for engineers while reducing wasted material.
GE Aviation and Morris Technologies had a long history together. In the 1990s, the company worked with Morris on the rapid prototyping of engine components in early development. Co-created by Cincinnati brothers Greg and Wendell Morris, along with Bill Noack, it had emerged as a world-leading “job shop” where additive manufacturing machines were used to produce advanced components for several industries, from medical to jewelry. With small factories in the Cincinnati suburbs of Sharonville and West Chester, Morris Technologies had become one of the largest operators of additive machines.
By 2003, GE Aviation had developed a new fuel nozzle injector (later incorporated into the best-selling LEAP engine) with a complex design nearly impossible to produce conventionally because of its elaborate interior geometries and miniscule passages. If produced using conventional casting methods, every injector inside the fuel nozzle would require at least 20 parts welded and brazed together. That was a daunting and expensive proposition for a high-volume part. GE Aviation was forced to think “outside of the box” for a new manufacturing method.
Led by GE combustion engineer Marie McMasters, the company initiated a secret project with Morris Technologies to additively produce the complex fuel injector. Morris employees had to sign proprietary agreements like it was a classified program. The work continued quietly for years.
By 2005, Morris and GE achieved a significant breakthrough: a fuel injector made of the superalloy cobalt chromium. “We used this alloy for dental and medical products,” Greg Morris recalled. “GE was not familiar with it, and there was skepticism at first. But it proved highly durable.”
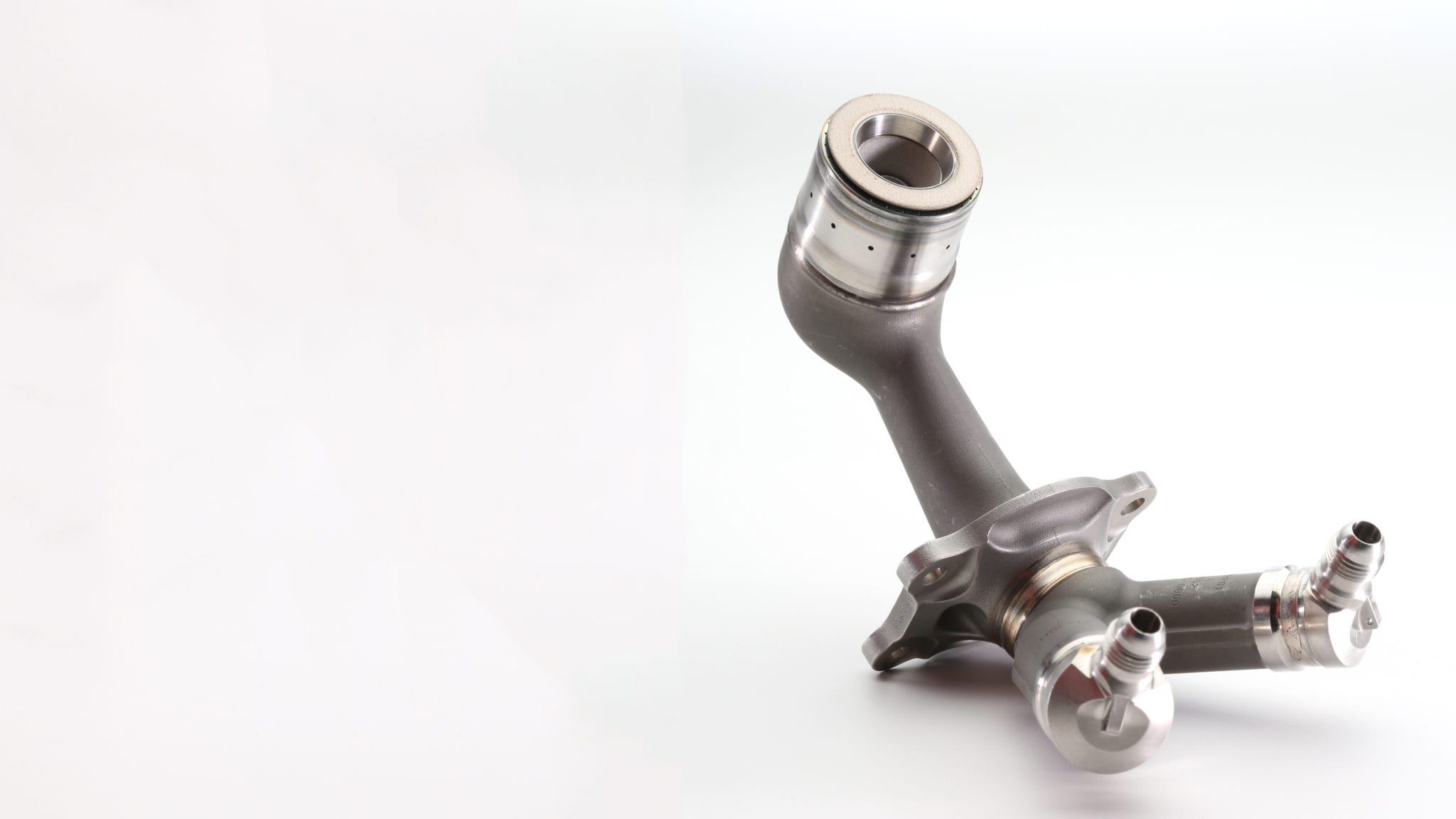
In 2012, Morris and GE developed the additive process parameters for mass-producing 19 fuel nozzle injectors for each LEAP engine, the new turbofan being developed for the single-aisle aircraft market by CFM International, a 50/50 venture owned jointly by GE and Safran Aircraft Engines. Two Aviation leaders at the time—Robert McEwan, a manufacturing general manager, and Mohammad Ehteshami, vice president of engineering—strongly advocated for an outright purchase of Morris Technologies. It was time to bring the innovative company into the GE family.
“When I saw what they could do with the nozzle, it was an epiphany,” recalled Ehteshami. “I think the first thing out of my mouth was ‘Buy them!’ ” Even when the purchase was disclosed in late 2012, GE kept mum about the years of secret additive development work on the LEAP fuel nozzle injector.
GE Aviation’s acquisition intrigued the aviation industry. As GE Aviation President and CEO David Joyce frequently asked his leadership team at the time, “Do you want to be on the inside, or the outside, of this [additive] revolution?”
That same year GE Aviation created the Additive Technology Center north of Cincinnati. The plant consolidated research equipment and additive machines acquired from Morris Technologies and intensified its research and development proficiencies from there. “The idea was to co-locate our most forward-thinking engineers in the additive world with R&D equipment, like they do in Silicon Valley or at the automotive headquarters in Detroit,” said Greg Morris, the center’s first manager.
The ATC began working closely with both GE Aviation and Avio Aero in Italy, which had also been recently acquired, to incorporate more additive components into engine designs. At the same time, GE Aviation’s Auburn, Alabama, plant was designated for large-scale additive manufacturing. Within a few years, rows of additive machines were installed at the Auburn site, producing thousands of fuel nozzle injectors for the LEAP engine.
In 2016, through two bold acquisitions, GE Aviation suddenly became a leading provider of the technology when it acquired two additive firms in Europe—Arcam AB and Concept Laser—and turned them into a new business: GE Additive. Based in Mölndal, Sweden, Arcam AB, inventor of electron beam melting (EBM) machines for metal-based additive manufacturing, is also a leading producer of advanced metal powders. At the time of the acquisition, Arcam already had a strong relationship with Avio Aero, which has been heavily engaged in EBM technology for several years.
https://www.youtube.com/watch?v=CUeDevI6kyE
Concept Laser, based in Lichtenfels, Germany, pioneered metal additive manufacturing with laser additive machines capable of processing various powder materials, including titanium, nickel-base, cobalt-chromium, and precious metal alloys, as well as hot-work and high-grade steels and aluminum. Immediately after the acquisitions, GE invested heavily in Arcam AB and Concept Laser operations to bolster their product lines and customer field support.
GE Aviation is using this new capability to drive additive opportunities across the jet engine portfolio. A classic example is GE’s new Catalyst turboprop engine launched in 2015. The Catalyst has more components designed and produced using additive manufacturing than any previous aviation engine, more than 25 percent of the overall engine. It doesn’t hurt that the additive parts also reduce weight and improve fuel consumption.
The company has come a long way since 2012. Yet it’s hard to imagine where GE Aviation would be today without that strategic acquisition of a small but innovative company just up the road in suburban Cincinnati.
“Morris Technologies led us to get into the market and develop our own additive machines and powder,” said Gary Mercer, vice president of engineering. “This technology is unique and has the promise of lower cost, while being lighter and more efficient. No technical trades—this is a win, win, and win.”
https://www.youtube.com/watch?v=55Yx2UBNUI4